Im Rahmen des vom Bundesministerium für Wirtschaft und Klimaschutz (BMWK) geförderten Verbundprojekts »UniFix« entwickelten die Expertinnen und Experten für Automatisierung und Produktionstechnik des Fraunhofer-Instituts für Fertigungstechnik und Angewandte Materialforschung IFAM in Stade gemeinsam mit Kooperationspartnern sowie Airbus Operations GmbH (Stade) als assoziiertem Projektpartner u.a. ein einzigartiges mobiles Spannfeld, das diverse Großbauteile, wie Flugzeug-Seitenleitwerke und -Landeklappen, in unterschiedlichsten Typen bis zu acht Metern Länge flexibel aufnehmen, formgebend exakt und nachhaltig ausrichten sowie transportieren kann. (Video: https://s.fhg.de/SS6)
Fokussiert auf Bearbeitungsprozesse im Produktionsablauf ist dieses Spannfeld in der Lage, eine Bearbeitungsanlage von zeitaufwendigen, nichtwertschöpfenden Nebentätigkeiten erheblich zu entlasten, indem es im Vorfeld mit den optimal und exakt ausgerichteten Großbauteilen verschiedene Prozessstationen passiert, an denen vorbereitende Arbeiten parallel und simultan erfolgen können.
Ein Meilenstein, denn in der zunehmend zu automatisierenden Fertigung, Bearbeitung und Montage von Großbauteilen aus gewichtsparenden carbonfaserverstärkten Kunststoffen (CFK) steht derzeit in der Flugzeugproduktion der Übergang von einer manuell getakteten Fertigung hin zu einer Flow-Line-Production bevor. Wie auch in anderen Branchen, z . B. dem Automobilbau, ermöglicht diese flussorientierte Fertigung, die Durchlaufzeiten zu reduzieren und damit die Produktivität, Effizienz und Wirtschaftlichkeit, somit die Konkurrenzfähigkeit im internationalen Markt, zu steigern. Die Vorteile der fließenden Fertigung liegen vor allem in Reduktion von manuellen Handlingsoperationen und Nebenzeiten. Dazu kommen Effizienzsteigerungen durch Spezialisierung der einzelnen Anlagen, verringerte Durchlaufzeiten aufgrund harmonisierter Taktzeiten sowie eine damit einhergehende Reduktion von Pufferbeständen und schnellere Reaktion auf Prozessabweichungen.
Herausforderungen bei der Herstellung von CFK-Großstrukturen
Sowohl das Seitenleitwerk als auch die Landeklappen eines Flugzeugs werden aus großen flächigen Schalenelementen zusammengefügt, welche durch Rippen versteift sind. Vor dem Fügen der Schalenelemente ist es nötig, sie durch automatisiertes Fräsen auf die erforderliche exakte Endkontur zu bringen. Dieser Bearbeitungsprozess stellt heute einen Engpass in der Produktion dar. Zudem ist er äußerst risikobehaftet, da Fehler auf hoher Wertschöpfungsstufe zu hohen Kosten durch Ausschuss oder Korrektur des Bauteils führen können.
Flow-Line-Production
»Um den Prozess – bei gleichzeitiger Risikominimierung – deutlich zu beschleunigen, haben wir uns im Projekt »UniFix« dazu entschieden, die mechanische Bearbeitung bei der Herstellung von Seitenleitwerken bzw. Landeklappen eines Passagierflugzeugs als Flow-Line-Production zu realisieren«, erklärt Projektleiter Christoph Brillinger vom Fraunhofer IFAM in Stade. »Dies ermöglicht uns, zeitintensive Nebentätigkeiten in der Bearbeitungsanlage zu vermeiden und sie somit signifikant zu entlasten. Zugleich werden wir den höchsten Präzisionsanforderungen im Flugzeugbau an allen Stationen gerecht, was insbesondere im Hinblick auf die Größe und die herstellungsbedingten Unikat-Eigenschaften der CFK-Bauteile eine ganz besondere Herausforderung darstellt«, betont Brillinger und ergänzt: »Wir haben in Stade einen übergreifenden Referenzierungsprozess entwickelt, der es ermöglicht, Vermessungsvorgänge bezüglich des optimal im Spannfeld positionierten Bauteils unabhängig von der Bearbeitungsstation durchzuführen. An der Bearbeitungsstation selbst ist dann nur noch eine aus wenigen Messpunkten bestehende Schnellreferenzierung nötig.«
Auf dem entlastenden Weg zur Bearbeitungsanlage – Die Stationen der Flow-Line
Bevor die neu entwickelte, vielseitig konfigurierbare, mobile Aufspannvorrichtung schlussendlich die CFK-Großbauteile zur Bearbeitungsanlage transportiert, passiert sie noch zwei Prozessstationen: In der ersten Station wird das vom Projektpartner FFT Produktionssysteme GmbH & Co. KG (Fulda) eigens entwickelte Spannfeld, das zehn verschiedene Landeklappen- bzw. Seitenleitwerk-Schalenelemente mit Längen von bis zu acht Metern aufnehmen kann, in einer automatisierten Routine für die Aufnahme des betreffenden Bauteils konfiguriert. Danach überprüft ein neuartiges Multikamerasystem (»Kamera-Arena«) des Projektpartners Hexagon AICON ETALON GmbH (Braunschweig) die Formhaltigkeit. So wird sichergestellt, dass das konfigurierte Spannfeld das CFK-Bauteil optimal in die nötige Sollform für die folgende präzise Bearbeitung positioniert. Schließlich folgt das Einlegen, die Positionierung und Aufspannung
sowie die Sicherung des Bauteils.
Für den Transport zur zweiten Station ist das Spannfeld samt Bauteil mit zwei fahrerlosen Transportsystemen (Automated Guided Vehicle; AGV) verbunden. Diese neu entwickelten
AGV-Systeme des Projektpartners Stäubli WFT GmbH (Sulzbach-Rosenberg) sind in der Lage, sich virtuell zu koppeln – d.h., sie tauschen Daten aus, um sich synchron bewegen zu können, ohne dabei mechanisch miteinander verbunden zu sein. So können sie im Synchronbetrieb große Lasten durch mehrere Fahrzeuge koordiniert transportieren. Das Fraunhofer IFAM in Stade entwickelte die zweite Station, an der das eingespannte CFK-Bauteil hochgenau und automatisiert mittels Laser-Linien-Scanner vermessen wird. Diese Vermessung ist unumgänglich, da das Bauteil herstellungsbedingt eine hohe Formvarianz – und damit einen Unikat-Charakter – aufweist. Anhand der Messdaten lassen sich die Soll-Bearbeitungsbahnen und die Soll-Lage der Bohrungspositionen für das Bauteil ermitteln. Das Bauteil ist nun für die Bearbeitung vorbereitet und kann von dem mobilen Spannfeld in die Bearbeitungsanlage gefahren werden. Die dritte Station ist die Bearbeitungsanlage. Da die herkömmlichen Nebentätigkeiten der Bearbeitungsanlage bereits an den ersten beiden Stationen erfolgt sind, ist hier nur noch eine Schnell-Referenzierung – bestehend aus der Messung weniger Referenzpunkte – nötig, bevor umgehend die eigentliche Bearbeitungsaufgabe ausgeführt werden kann.
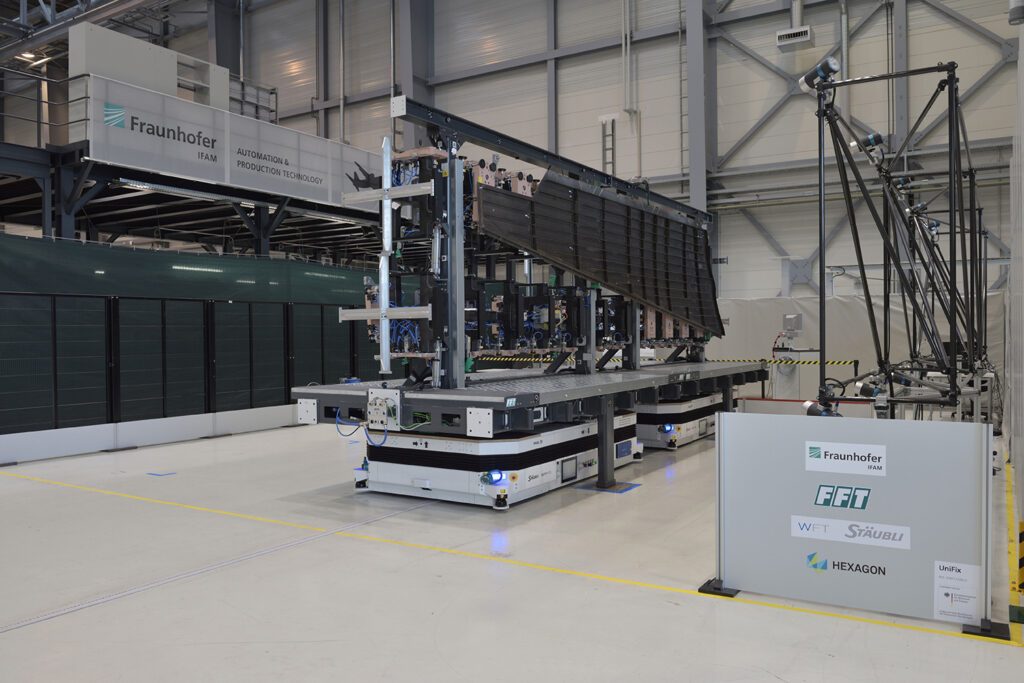
Ausblick
Die im Forschungsprojekt »UniFix« gewonnen Erkenntnisse und entwickelten Technologien lassen sich nicht nur für die Flugzeugproduktion weiter vorantreiben und implementieren, sondern ebenso effizienzsteigernd in die Produktionsprozesse anderer Branchen – wie Windenergieanlagen-, Schienenfahrzeug-, Nutzfahrzeug-, Automobil- oder Schiffbau – übertragen. In dem vom Land Niedersachsen geförderten Projekt »InProNi« (»Innovative Produktionssysteme aus Niedersachsen«), das am 1.1.2022 startete, werden die im Forschungsprojekt »UniFix« erarbeiteten Konzepte weiterverfolgt. Im Fokus stehen Fräsprozesse am Spannfeld in der Bearbeitungsanlage sowie weiterführende Referenzierungsstrategien.
Willy Messerschmitt-Studienpreis 2021
Die Masterarbeit »Automated Scanning Process of a Large Scale CFRP Component« von Satheesh Kumar Kallipalayam Murugesan, die in Kooperation mit dem Institut für Produktionsmanagement und -technik (IPMT) der Technischen Universität Hamburg entstanden ist, befasst sich mit der Umsetzung der automatisierten Bauteilvermessung der zweiten Station.
Sie wurde 2021 mit dem Willy Messerschmitt-Studienpreis durch die Deutsche Gesellschaft für Luft- und Raumfahrt (DGLR) ausgezeichnet. Auftraggeber Nach einer Laufzeit von etwa drei Jahren endete Ende 2021 das vom Bundesministerium für Wirtschaft und Klimaschutz (BMWK) geförderte Forschungsprojekt »UniFix« (»Universelle mobile Bauteilspann- und Fixiervorrichtung für die Bearbeitung von Faserverbundstrukturen«); Förderkennzeichen: 20W1722A-D.