Die Skelettbauweise am Beispiel eines Dachspriegels
Im Förderprojekt MAI Skelett wurden am Beispiel eines Dachspriegels das strategische Ziel des Spitzenclusters der deutlichen Kostenreduzierung von CFK-Bauteilen mit einem neuen konstruktiven und fertigungstechnischen Ansatz entwickelt und bestätigt. Konstruktiv wird für den Dachspriegel die lastpfadgerechte Auslegung durch wenige unidi-rektionale, aber starke Stränge aus endlosfaser-verstärkten Carbonfasern längs des Spriegels und somit in Fahrzeugquerrichtung umgesetzt, welche durch eine Rippenstruktur im Sinne eines Fachwer-kes (Skelettbauweise) verbunden sind. Fertigungs-technisch wird die Herstellung auf drei bekannte, industriell genutzte, robuste Prozesse zur Bau-teilherstellung beschränkt. Das Pultrudieren endlosfaserstärkter Carbonfasern zu unidirektionalen Strängen mit einer thermoplastischen Matrix, das Umformen der Stäbe zu einer produktspezifischen Faserverstärkung, wobei auch starke Querschnittsänderungen möglich sind, und das Überspritzen dieser Profile im Sinne von Einlegeteilen. Als Spritzgussmaterial kommen recycelte Carbonfasern zum Einsatz.
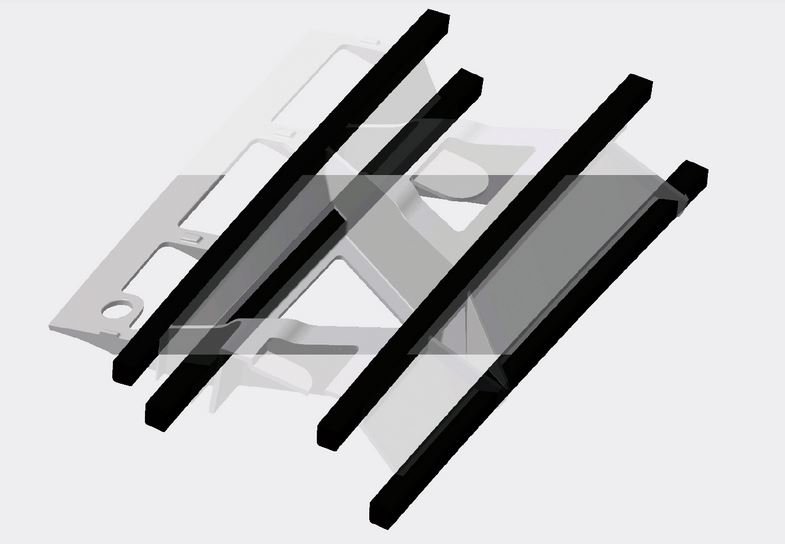
© BMW Group
Das Potential eines langfaserverstärkten Carbon-Spritzgusscompounds wurde durch parallel durchgeführte Versuche grundsätzlich untersucht.
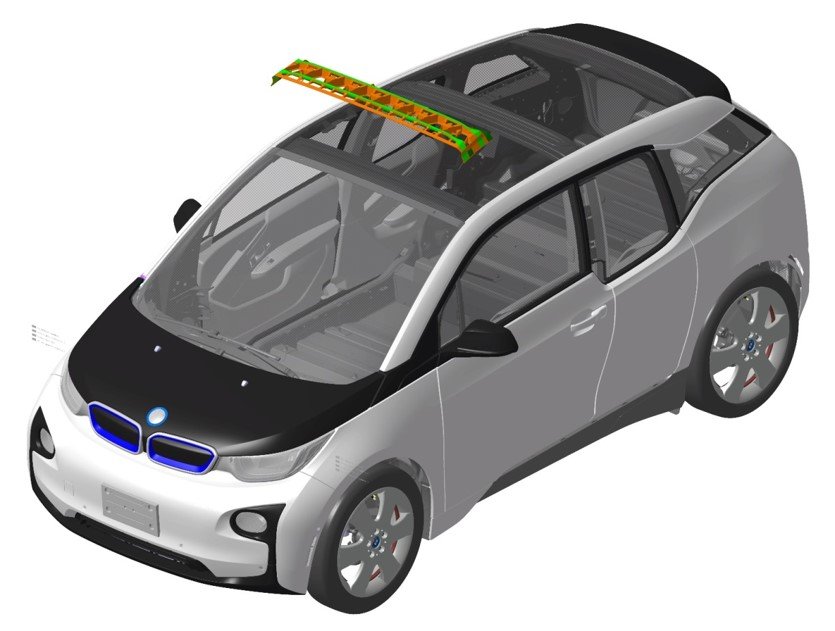
© BMW Group
Neben der Materialvarianz für das Spritzgussmaterial wurde die Geometriefreiheit des Spritzgießprozesses zur optimalen Auslegung des Bauteiles als auch die Funktionsintegration, z. B. von Anschraubelementen genutzt. Durch die engagierte Zusammenarbeit der Partner, die ihre Schwerpunkte längs der Prozesskette hatten, konnte ausgehend von dem Konzept in kurzer Projektlaufzeit die Erprobung durchgeführt werden. Verbundpartner waren: BMW AG (Konzept, Konstruktion, Stabumformung, Erprobung); SGL Automotive Carbon Fibers GmbH & Co. KG (carbonfaserverstärkte Spritzgussmaterialien); CirComp GmbH (Pultrusion der Stäbe); P+Z Engineering GmbH (Auslegung) und Eckerle GmbH (Spritzgießen).