Schweißen des ersten Thermoplast-Flugzeugrumpfs der Welt
Im Rahmen des Clean Sky 2-Programms demonstriert Fraunhofer in Stade die Montage des weltweit größten Thermoplast-Flugzeugrumpfs. In dem anspruchsvollen Forschungsvorhaben kommen verschiedene Schweißverfahren, Automatisierungstechnologien und neuartige Materialien zur Anwendung, wodurch die Effizienz in der Hochratenproduktion sowie die Treibstoffeffizienz durch die Gewichtsreduktion gesteigert werden.
Im Rahmen des Clean Sky 2-Projekts Large Passenger Aircraft (LPA) arbeitet die Fraunhofer-Gesellschaft in Stade mit internationalen Projektpartnern am Multi Functional Fuselage Demonstrator (MFFD), dem weltweit ersten thermoplastischen CFK-Flugzeugrumpfsegment. Durch das Verschweißen von 8 m langen thermoplastischen CFK-Halbschalen entlang der zwei Längsnähte entsteht ein Rumpfsegment mit einem Durchmesser von etwa 4 m.
Vorintegration und Schweißtechnik
Der im Projekt von Fraunhofer entwickelte CO2-Laserschweißprozess für die Längsnaht ermöglicht im Vergleich zum Nieten Gewichtsreduktion und staubfreies Fügen. Der Bedarf hierfür ergibt sich aus der erstmalig durchgeführten Vorintegration beider Schalen mit zahlreichen ebenfalls schweißtechnisch gefügten Struktur- und Systemkomponenten, die ein nachträgliches Entfernen von Staub und Spänen nicht zulassen würden. Die innovative Bauweise des MFFD braucht dadurch deutlich weniger Niete. Dies führt zu einer hohen Effizienzsteigerung in der Hochratenproduktion und verbessert die Treibstoffeffizienz.

MFFD-Montage-Forschungsplattform mit integrierten thermoplastischen Rumpfschalen bei Fraunhofer, Stade
Automatisierte hochpräzise Montage
Für die automatisierte Montage wurde eine Forschungsplattform im CFK NORD in Stade entwickelt und errichtet. Die Plattform umfasst eine zentrale Anlagen- und Prozesssteuerung, in die Technologiebausteine weiterer Projektpartner integriert sind. Das hochpräzise Positionieren der beiden Schalen zueinander übernehmen zehn Hexapod-Roboter, die mittels Laser-Sensoren die optimale Form und Lage der Schalen einstellen und bei Bedarf nachjustieren.
Beim CO2-Laserschweißen werden bis zu 4,5 m lange CFK-Streifen (Straps) mit einem Strap-Handling-Werkzeug exakt auf der Naht geführt, positioniert und dem nachfolgenden Schweißkopf zugeführt. Der Schweißkopf fährt entlang der Naht und schmilzt deren Oberfläche auf. Das Strap-Handling-Werkzeug presst den Strap dann per Andrückeinheit mit Fügekräften von bis zu einer Tonne gegen die oberen und unteren Schalenfügestellen. Um Schäden an der Rumpfstruktur durch die hohen Fügekräfte zu vermeiden, stützt innerhalb der entstehenden Rumpfsektion eine spezielle Vorrichtung zur Kraftaufnahme und -ableitung die Schalenschweißregionen ab.
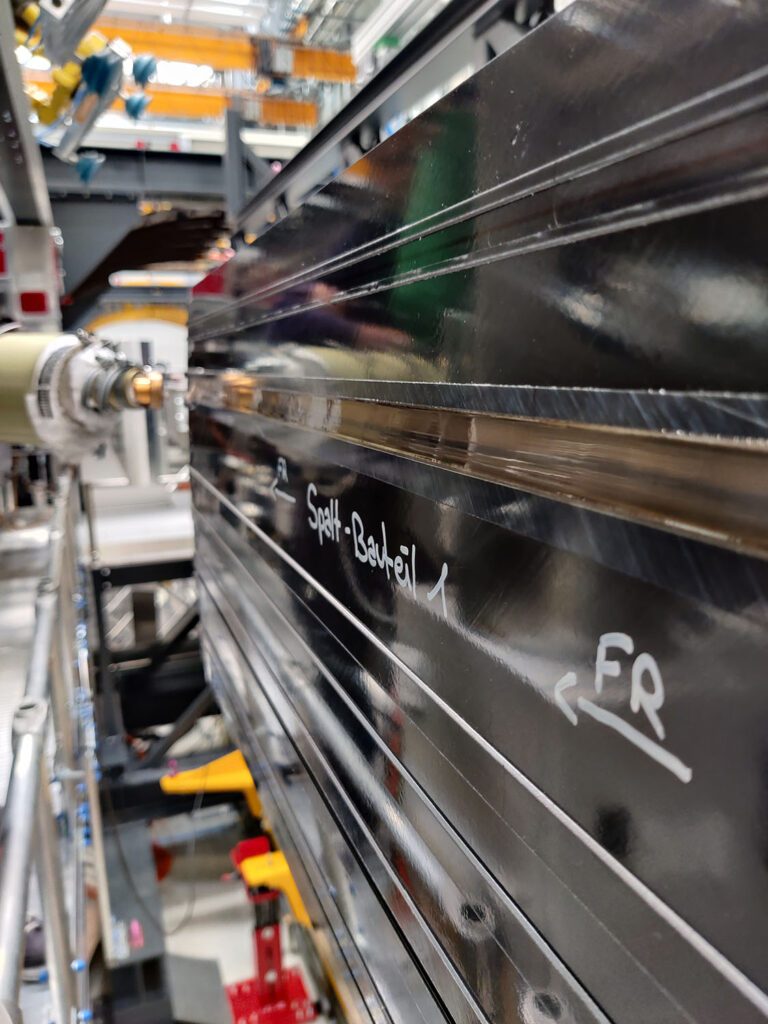
Spaltfüllprozess – mit Extruderwerkzeug gefüllter Spalt an thermoplastischem CFK-Rumpfschalensegment
Das automatisierte Füllen der ober- und unterhalb der Straps entstandenen Spalte übernimmt ein Extruder. Dieser wird nach jedem geschweißten Strap entlang der zuvor erzeugten Verbindungsnähte geführt, erhitzt das Ausgangsgranulat und fördert es über eine Schnecke zum Spalt. Eine spezielle Düse sorgt dafür, dass das Material den Spalt füllt, bevor es an der Luft aushärtet. Ein im gleichen Endeffektor integrierter 2D-Sensor misst vorab das lokale Spaltvolumen und überträgt diese Information an das Extrudersystem. Die Austragleistung wird also während des Prozesses dynamisch berechnet, sodass unregelmäßige Spalten von 3 – 11 mm Breite an jeder Stelle mit genau der erforderlichen Menge geschmolzenen Thermoplast-Matrixmaterials gefüllt werden.
Gefördert durch Clean Aviation Joint Undertaking (JU), mitfinanziert durch die Europäische Union.
Kontakt:
Fraunhofer-Institut für Fertigungstechnik und Angewandte Materialforschung
IFAM, Automatisierung und Produktionstechnik , Stade
Dipl.-Ing. Leander Brieskorn
leander.brieskorn@ifam.fraunhofer.de
Dipl.-Ing. oec. Benjamin Diehl
benjamin.diehl@ifam.fraunhofer.de
+49 4141 787 07-0
www.ifam.fraunhofer.de/stade