Holz ist ein natürlicher Faserverbundwerkstoff aus Cellulosefasern und der biologischen Matrix Lignin. Durch den großen Porenvolumenanteil und wachstumsbedingte Strukturveränderungen im Holz kann das mechanische Materialpotenzial jedoch nicht voll ausgeschöpft werden. Das Forschungsprojekt „Woodtrusion“ kann das ändern.
Unter Einwirkung von Wärme und Druck ist Holz komprimierbar, wodurch sich verbesserte Materialeigenschaften wie höhere Festigkeit und Witterungsbeständigkeit erzielen lassen. Zudem ermöglicht die thermo-mechanische Verdichtung neue, spanlose Herstellungsverfahren für technische Profile aus Holz.
Löst man vorab Lignin und Hemicellulose durch chemisch-thermische Prozesse aus dem Holz heraus, sind Volumenreduzierungen bis um den Faktor 5 bei analoger Zunahme der Dichte möglich. Nach Vorbehandlung und Komprimierung konnte eine Steigerung der Festigkeit um das Zwölffache nachgewiesen werden.
Technischer Ansatz
Ziel des Woodtrusion-Projekts war es, einheimische Dünnhölzer zu hochwertigem Konstruktionsholz in Form von Rohren zu verarbeiten. Anhand von Fichtenhölzern wurden in umfangreichen Materialuntersuchungen optimale Prozessparameter für Verdichtungsgrad, Temperatur und Feuchtigkeit ermittelt. Insgesamt entwickelten
die Projektpartner eine komplexe Anlage (Abb. 1), die alle Prozessstufen umfasst:
- Vereinzelungs- und Zuführstrecke (Steinbeis Innovationszentrum Chemnitz)
- Plastifizierungs- und Verdichtungsstrecke (Niemeier Fahrzeugwerke Lunzenau)
- Wicklungs- und Fixierungsstrecke (STFI e. V. Chemnitz)
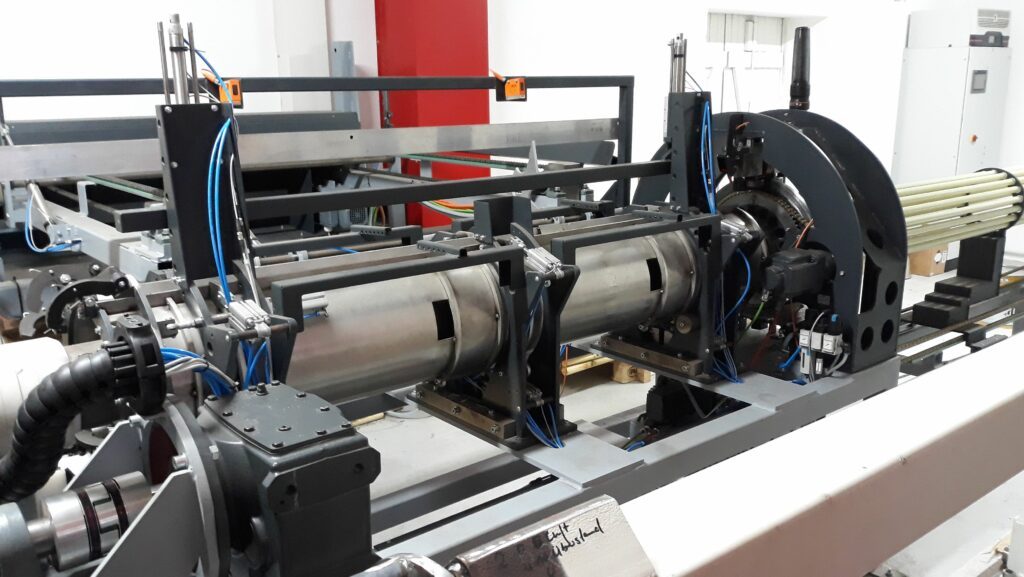
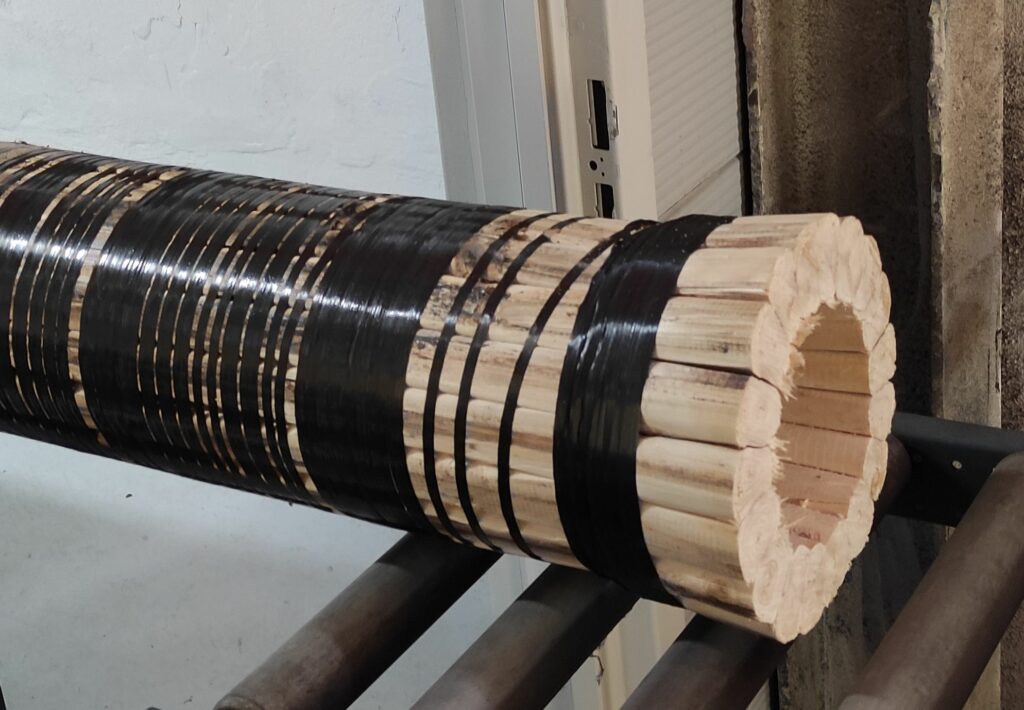
Prozessablauf
Einem Revolvermagazin werden Rundprofile aus Dünnholz zugeführt, mit Längenversatz, um Schwachstellen in den Rohren zu vermeiden. Die Anlage kann durch alternierend genutzte Magazine quasikontinuierlich arbeiten.
In einem neu entwickelten Pressform-Werkzeug werden die Rundhölzer dann auf 120 – 140 °C erhitzt und komprimiert. Um die Rückstellkräfte des Holzes am Pressformausgang zu kompensieren, wurde eine Umwindeeinheit in das Verfahren integriert. Die Umwindeeinheit arbeitet im Orbitalwickelverfahren und kann zwei um 180° versetzte Spulen aufnehmen.
Zum Wickeln wurden 50K-Carbonfaser-Towpregs (SIGRAFIL® C T50-4.0240E100) verwendet, deren Harzsystem beim Kontakt mit dem aufgeheizten Holz aushärtet. Über die Drehzahl der Umwindeeinheit kann die Dicke der Armierung auf die zuvor berechneten Rückstellkräfte angepasst werden. Im konkreten Fall wurde eine zweilagige Armierung mit ca. 1 mm Wandstärke aufgebracht. Ohne Armierung weitet sich das Rohr beim Verlassen der Anlage wieder auf (Abb. 2).
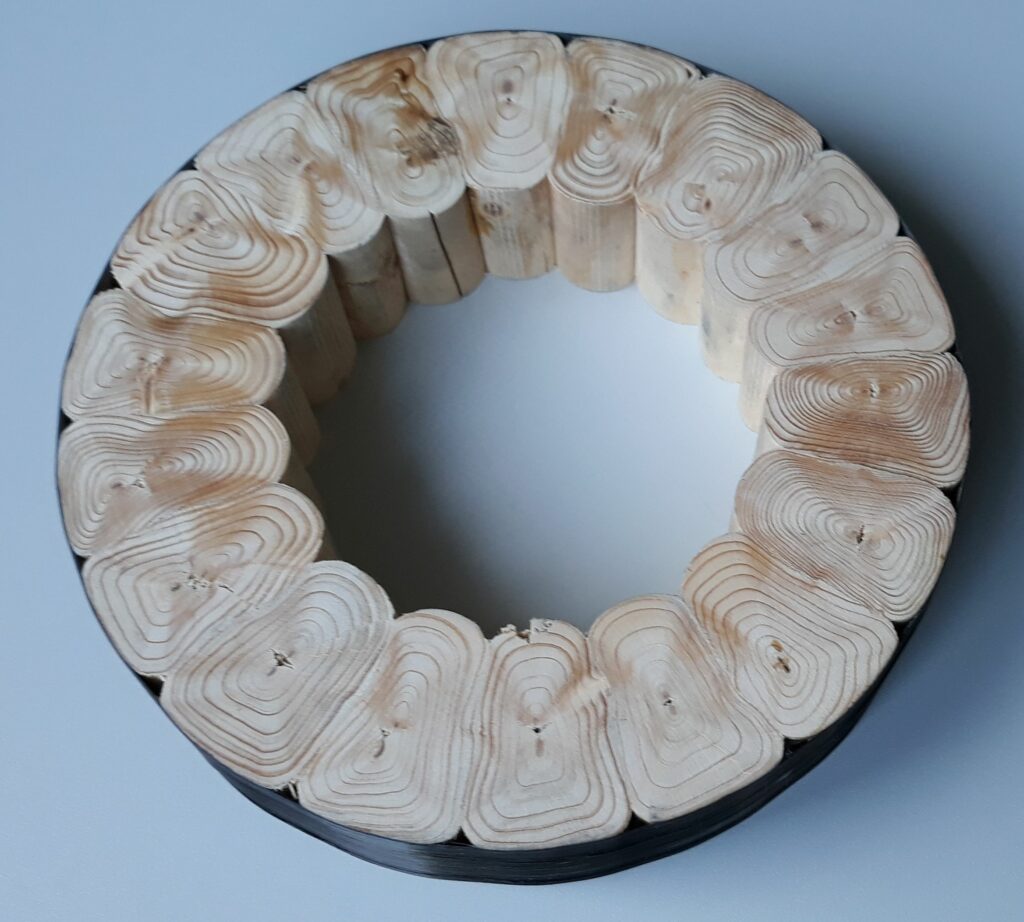
Mögliche Anwendungsbereiche
Mit der Anlage können faserarmierte Holzrohre (Abb. 3) in beliebiger Länge gefertigt werden. Mögliche Anwendungen sind etwa als alternatives Material für Säulen aus Stahl im Hochbau. Für die Anpassung an den jeweiligen Einsatzfall und die entsprechende Belastungsart ist ein abschließender Laminataufbau im Wickelverfahren
möglich (Abb. 4).
Kontakt:
Sächsisches Textilforschungsinstitut STFI e. V., Chemnitz
Dipl.-Ing. Günther Thielemann
+49 371 52 74-239
guenther.thielemann@stfi.de
www.stfi.de
Niemeier Fahrzeugwerke GmbH (ehem. STM Montage GmbH), Lunzenau
Dipl.-Ing. Tom-Egmont Werner
+49 37383 74 98 24
wernert@niemeier-fahrzeugwerke.de
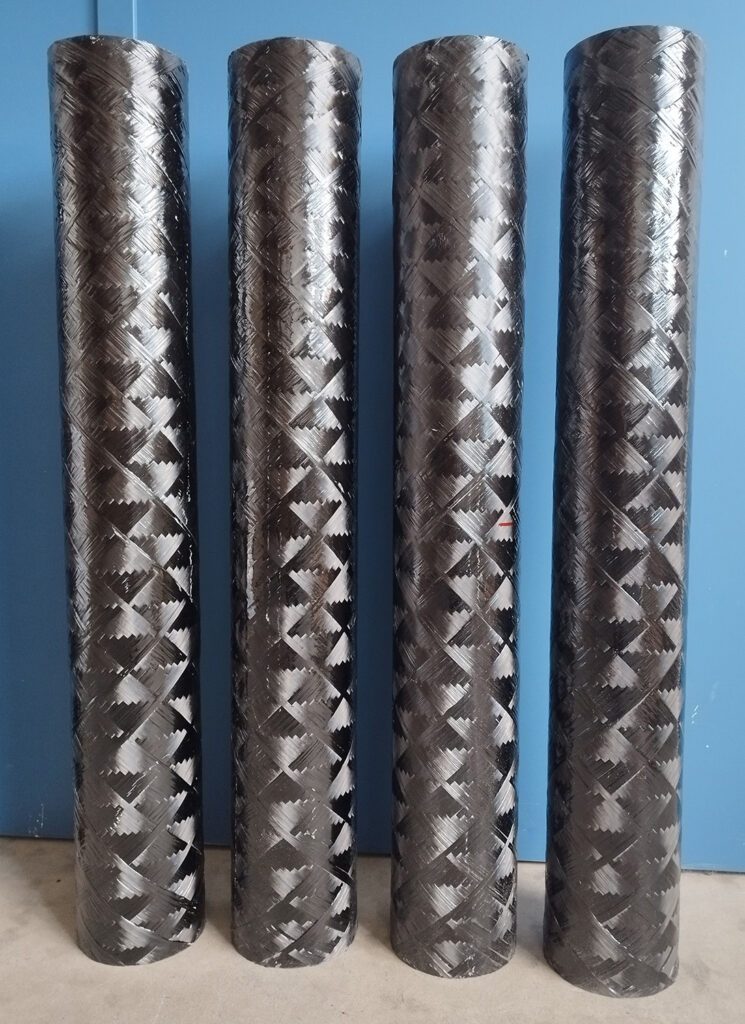
Wir danken dem Bundesministerium für Ernährung und Landwirtschaft für die Förderung des Förderprojektes (FKZ 22009217) sowie dem Projektträger, der Fachagentur für Nachwachsende Rohstoffe e. V.