Nach dem Wachstumskern thermoPre® ist nun auch das Folgeprojekt, der Wachstumskern thermoPre® plus, mit der Diversifizierung und Erweiterung der Technologieplattform der einstufigen Direktverarbeitung, erfolgreich abgeschlossen worden.
Am 08. und 09. November 2022 fand die 8. thermoPre®-Fachtagung in Chemnitz statt. Unter dem Motto „Faserverstärkte Thermoplaste: nach wie vor im Trend!“ referierten an zwei Tagen Vertreter aus Industrie und Forschung zu Trends, Innovationen und Einsatzmöglichkeiten faserverstärkter Thermoplaste. Die Tagung bildete gleichzeitig die Abschlussveranstaltung des Wachstumskerns thermoPre® plus. Die über 100 Teilnehmer erhielten umfangreiche Einblicke in die mehrjährige Forschungsarbeit, in ausgewählte Ergebnisse und konnten neue Anlagen und Bauteile besichtigen.
Bereits Ende 2018 ist das große Forschungsprojekt, welches wie sein Vorläufer, vom Bundesministerium für Bildung und Forschung im Rahmen der Initiative „Unternehmen Region“ gefördert wurde, mit dem Ziel gestartet, grundlegend neue Ansätze zur ressourcen- und kosteneffizienteren Herstellung von funktionsintegrierten thermoplastischen Hochleistungsbauteilen mit Endlosfaserverstärkung zu erforschen und bis zu einem Technologiereifegrad (TRL) der Stufe 4 zu führen. 24 Unternehmen, drei Forschungseinrichtungen und drei assoziierte Partner entwickelten in sieben großen Verbundprojekten u. a. neue Module und Anlagen sowie die Technologiebasis für die Herstellung von endkonturierten Textilhalbzeugen mit belastungsgerechter Faserausrichtung in einem vollautomatisierten, kontinuierlichen „Rolle-zu-Rolle“-Prozess (effiLOAD-Technologie).
Durch die wachsende Forderung einer nachhaltigen Energie- und Ressourceneffizienz nimmt die Bedeutung neuer Produktionstechniken stetig zu. Die Herstellung und Verarbeitung innovativer Materialien, die Integration von Funktionen sowie eine last- und werkstoffgerechtere Konstruktion führen zu neuen Produkten und Anwendungen. Genau an diesem Punkt setzten die Partner des Wachstumskerns an. So wurde die Technologieplattform der einstufigen Direktverarbeitung, einer im Wachstumskern thermoPre® entwickelten Großserientechnologie für die Herstellung endlosfaserverstärkter, thermoplastischer Halbzeuge, um die Verarbeitung von Hochleistungs- und Hochtemperaturpolymeren erweitert. Im Ergebnis können in einer neuen Anlage endlosfaserverstärkte Tapes bis 600 mm Breite, mit unterschiedlichen Verstärkungsfasern und den Matrices PP, PA6, PA6.6, PPS und PET hergestellt werden (Abb. 1).
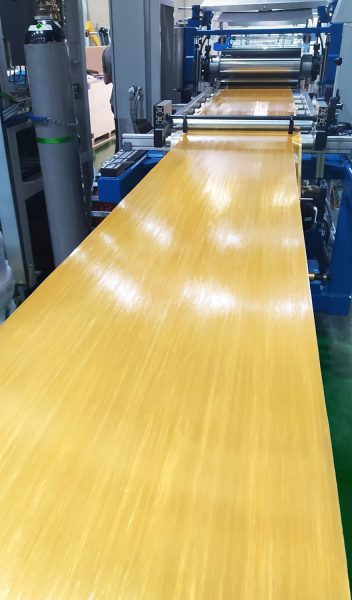
An einer Erweiterung des Polymerportfolios wird seitens der beteiligten Partner bereits jetzt weitergearbeitet. Anwendungen für die neuen Hochtemperaturhalbzeuge werden in allen Industriebereichen gesehen, vor allem aber im Transportwesen, im Automobilbau und in der Luftfahrt. Die Potentiale der neuen Hochtemperaturtapes wurden im Forschungsprojekt am Beispiel des Demonstrators „Frontendadapter“ als Strukturleichtbaukomponente aufgezeigt, wo die Bauteileigenschaften möglichst konsistent im Temperaturspektrum von -25 bis +80° C verbleiben müssen. Eine gute mechanische Performance wird durch einen deutlich verbesserten Verbundaufbau auf der Basis aufeinander abgestimmter Matrixwerkstoffe erreicht und durch einen lastpfadgerechten Profileinleger, welcher mittels Thermoplast-Wickeln und Thermoformen in Kombination mit Innenhochdruckumformen (IHU) hergestellt wird. Die Abb. 2 zeigt das Muster eines Frontendapapters.
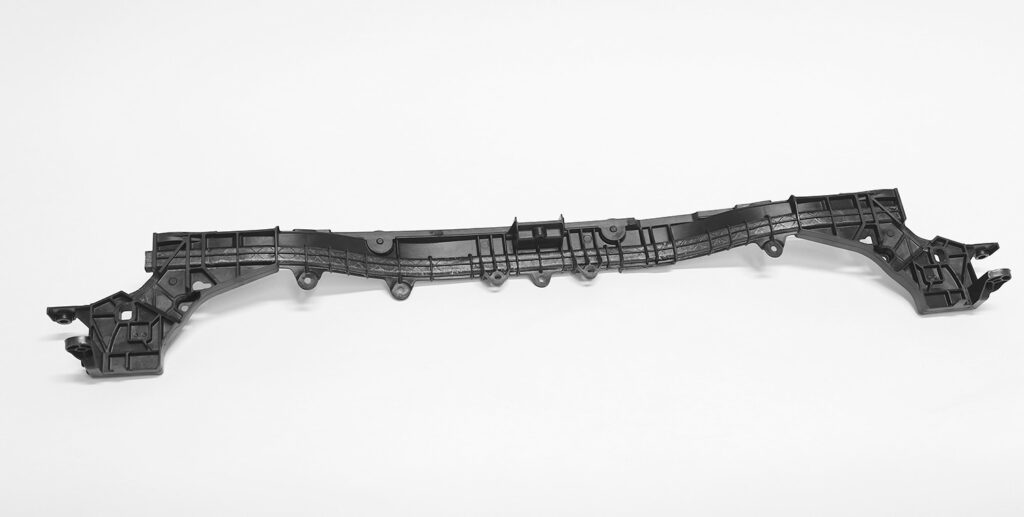
Die mechanischen, wirtschaftlichen und ökologischen Anforderungen an moderne Leichtbaustrukturen sind häufig disparat und erfordern zunehmend die gezielte Kombination von neuartigen Materialien, intelligenten Bauweisen und effizienten Fertigungstechnologien. Ein Konzept, welches diesem Gedanken folgt, ist z. B. die Entwicklung der effiLOAD-Technologie zur kontinuierlichen Herstellung endkonturnaher, lastpfadgerechter und verschnittreduzierter Preformen für Hochleistungsbauteile.
Im effiLOAD-Verfahren werden die Endlosfasern als konsolidierte thermoplastische Tapes in definierter Breite endkonturnah und belastungsgerecht in Lagen übereinander auf einem sich fortlaufend bewegenden Trägermaterial abgelegt und thermisch fixiert. Zusätzlich zur flächigen endkonturnahen Halbzeugstruktur erfolgt die Verlegung von Endlos-Verstärkungsfasern als Hybrid-Rovings in der Form, dass deren Verlauf in Richtung zur Längsachse der Warenbahn lastpfadgerechte partielle Verstärkungen der Preform ermöglicht. In Abhängigkeit der Anzahl der Multi-Tape-Legeköpfe können größere Bauteilabmessungen in einem Arbeitsgang hergestellt werden. Ausgehend von einer ortsfesten 0°-Ablage können mit einer verfahrbaren Legeeinrichtung quasi isotrope Strukturen in Winkeln von 90° und +/- α (z.B. α=45°) endkonturnah abgelegt werden. Nach Ablage der flächigen Struktur erfolgt das lastpfadgerechte Aufbringen von Hybrid-Rovings in einem kontinuierlichen Prozess. Die so gebildete Preform wird anschließend aus der Trägerbahn herausgeschnitten und über ein Handling-System wird ein Preformstack, d.h. ein bauteilgerechter Stapel, aus effiLOAD-Zuschnitten gebildet. Die Abb. 3 veranschaulicht das Gesamtlayout der komplexen Anlage.
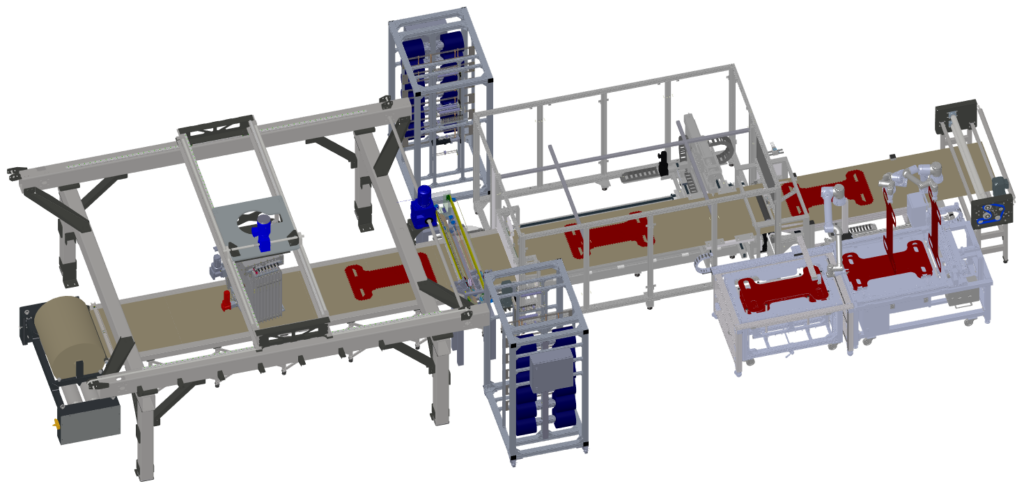
Mit der effiLOAD-Technologie wurde ein völlig neues Verfahren entwickelt, welches innerhalb des gesamten Wachstumskerns eine zentrale Stellung eingenommen hat und welches mit dem Patent Nr. EP3 257 663 B1 geschützt ist.
Die neue Technologie zeichnet sich durch eine deutlich verbesserte Ressourceneffizienz und Energieeinsparung insbesondere für Carbonfaseranwendungen aus, da bauteilabhängig Verschnittreduktionen bis 70 % erreicht werden können. Die in der Herstellung energieintensiven Carbonfasern kommen ausschließlich partiell entlang der Lastpfade zum Einsatz. Damit liefert das effiLOAD-Verfahren einen Beitrag auf dem Weg zum Umbau auf CO2-arme und langfristig klimaneutrale Produktionstechnologien. Aufgrund der deutlichen Steigerung der Wirtschaftlichkeit, Ressourceneffizienz und Produktivität, kann eine signifikante Erweiterung und Diversifizierung der Einsatzfelder von endlosfaserverstärkten thermoplastischen Faserverbundmaterialien erzielt werden. Dadurch werden intelligente und klimafreundliche Leichtbaulösungen in die breite industrielle Anwendung getragen.
Am Beispiel einer Sitzschale für Schienenfahrzeuge, wird das technische, wirtschaftliche und ökologische Potenzial der effiLOAD-Preformen praktisch aufgezeigt. Strukturbauteile aus dem Interieur-Bereich weisen Designelemente mit komplexen Formen auf und sind gleichzeitig hohen Anforderungen in Bezug auf die optischen und haptischen Oberflächeneigenschaften ausgesetzt. Darüber hinaus unterliegen derartige Bauteile verschiedensten statischen und dynamischen Lastfällen sowie hohen Anforderungen an die Temperatur- und Flammbeständigkeit. Im Schienenfahrzeugbereich sind bei Strukturbauteilen für Interieur-Anwendungen Flammschutzeigenschaften und Temperaturbeständigkeiten von über 150° C gefordert.
Die Abb. 4 zeigt das Muster eines Schienenfahrzeugsitzes, welches sich u. a. durch folgende Vorteile gegenüber dem Referenzsitz (Masse 7,2 kg) auszeichnet:
- Masseeinsparung von 29 %
- Einteilige Sitzschale mit optionalen Anbauteilen, d. h. wesentliche Reduzierung der Herstell- und Montagekosten
- Erfüllung der Brandschutzanforderungen nach DIN EN 45545
- Erfüllung der Prüfanforderungen nach VDV 152 u. DB
Da sich Schadstoffemissionen mit der Etablierung von umweltfreundlichen Antriebstechnologien zunehmend in Richtung der Produktionsphase verschieben, kann mit CO2-armen Produktionsprozessen ein wichtiger Beitrag zur Erreichung von Nachhaltigkeits- und Klimazielen erreicht werden. Eine Massereduzierung bewirkt für alle Anwendungen nachhaltige Lösungsansätze, welche die Energie- und Ressourceneffizient im Focus haben. Die Ergebnisse des Wachstumskerns thermoPre plus zeigen in beeindruckender Weise, dass Leichtbaulösungen mit ganzheitlichen Ansätzen vom Rohstoff bis zum einsatzfähigen Bauteil die Anforderungen an eine CO2-neutrale Industrieproduktion nachhaltig erfüllen.
thermoPre ENGINEERING GmbH, Chemnitz
www.thermopre-gmbh.de
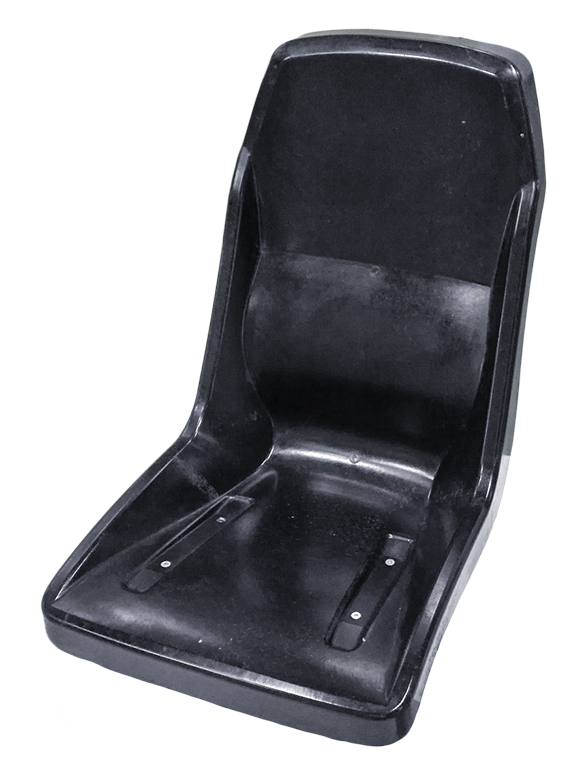