Durch den Einsatz hochwertiger Leichtbaumaterialien wie Carbon können die bewegten Massen für Bahnanwendungen erheblich reduziert und so auch die CO2-Emmissionen drastisch minimiert werden. Durch intelligente Laminataufbauten lassen sich zudem zusätzliche Funktionen wie Impactschutz, Feder- oder Dämpfungselemente oder ein Structural-Health-Monitoring-System in derartige Komponenten integrieren.
Die hohen Anforderungen in der Bahnindustrie stellten bislang signifikante Hürden zum Einsatz von Leichtbaumaterialien in diesem Segment dar. In einem von der Sächsischen Aufbaubank (SAB) geförderten Forschungsvorhaben haben sich Wissenschaftler des KVB gemeinsam mit den Projektpartnern Hörmann VE, Fraunhofer IWU und IMA mit der Entwicklung und Fertigung eines Leichtbau-Drehgestellrahmens befasst. Um signifikant Masse einzusparen, wurde dabei die im Stand der Technik übliche Stahl-Schweißkonstruktion durch eine Carbonbauweise substituiert.
Herausgekommen ist ein um bis zu 80 % leichterer Drehgestellrahmen, der zudem mit zusätzlichen Funktionen wie einer integrierten Federung im Bereich der Längsträger aufwartet. Daneben zeigten Untersuchungen an Couponproben, wie eine derartige impactgefährdete Struktur durch geeignete Maßnahmen gegenüber Steinschlägen aus dem Gleisbett geschützt werden kann.

Integriertes Sensorsystem liefert permanenten Strukturzustand
Um derartige Belastungen auf die Struktur auch im laufenden Betrieb richtig bewerten zu können, bestand ein weiteres Ziel des Forschungsvorhabens in der Integration eines Structural-Health-Monitoring-Systems (SHM), das dauerhaft und zuverlässig auch unter realen (wechselnden) Umgebungsbedingungen den Strukturzustand überwacht.
Hierzu wurden bereits während der Herstellung der Carbon-Komponenten des Drehgestellrahmens über 130 Dehnungs-Sensoren im Laminat integriert. Das schützt gleichzeitig das empfindliche Sensorsystem vor äußeren Einflüssen. Über insgesamt zwölf ebenfalls im Laminat integrierte Kontaktierungsstellen wird die Vielzahl der Sensordaten ausgewertet. Dafür wurde eigens eine miniaturisierte und zugleich hochleistungsfähige Auswerteeinheit entwickelt.
Zugleich können mit dem System nicht nur Aussagen zum Strukturzustand, sondern auch zu fertigungsinduzierten Dehnungen getroffen werden, da die Sensoren bereits während der Aushärtung der Carbonbauteile im Autoklav ausgelesen werden können. Mit den damit gewonnenen Erkenntnissen konnte der Einfluss der Härtung auf die Struktureigenschaften abgeleitet werden. Auf der diesjährigen Messe InnoTrans wurden einzelne Komponenten des Drehgestellrahmens auf dem Messestand der Hörmann VE der Öffentlichkeit präsentiert.
Potenziale des Sensorsystems auch für weitere Bahnanwendungen
Das eingesetzte Sensorsystem kommt auch in anderen Bahnanwendungen bereits zum Einsatz. So konnten in der Vergangenheit schon Torsionsfedern aus CFK mit der Sensorik ausgestattet werden. Zudem werden im KVB derzeit GFK-Druckluftbehälter mit integrierter Sensorik für den Einsatz in Güterwaggons im Faserwickelverfahren gefertigt.
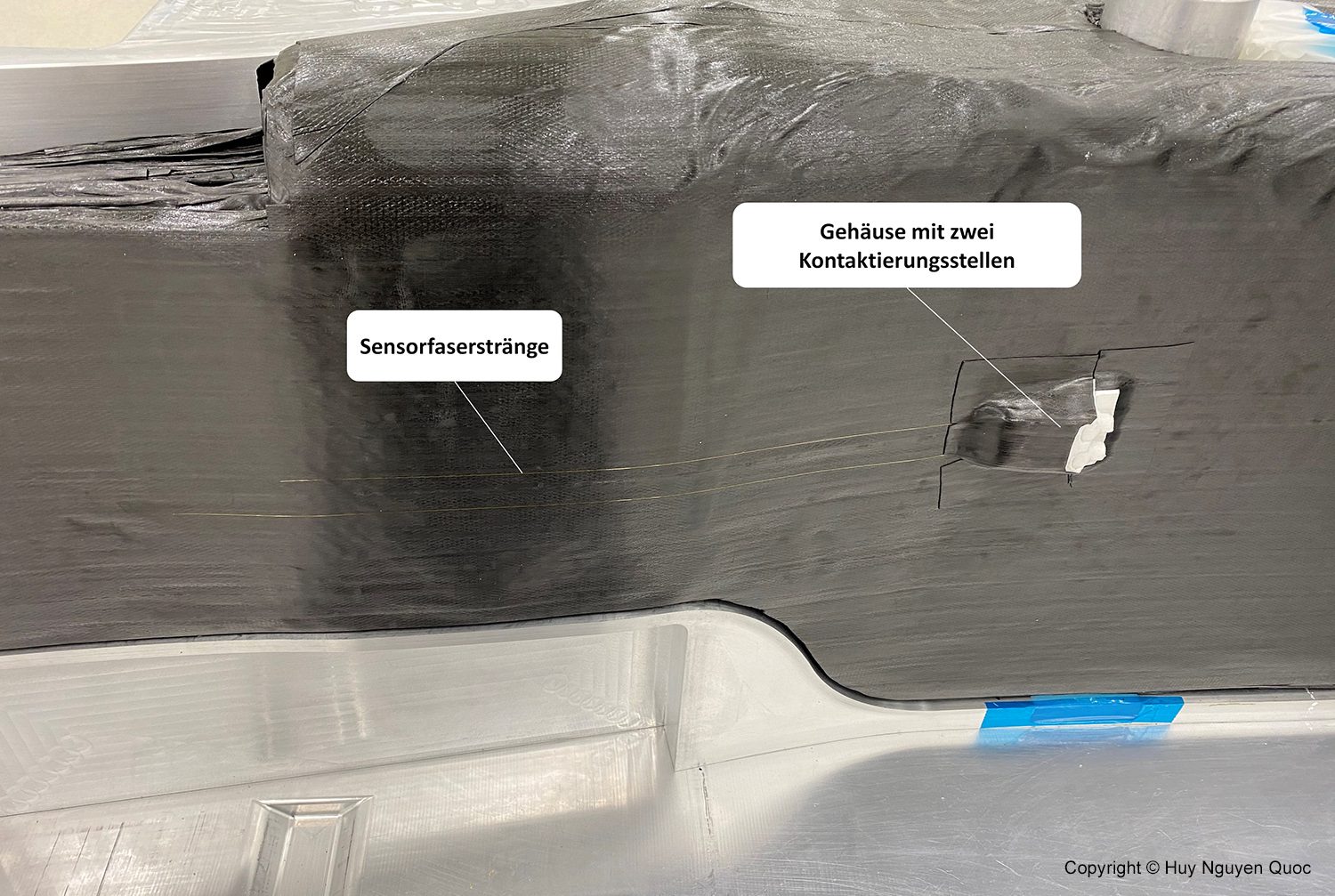
Kontakt:
KVB Institut für Konstruktion und Verbundbauweisen gGmbH, Großweitzschen
www.kvb-forschung.de