Verbundwerkstoffe spielen in vielen Anwenderbranchen eine zunehmende Rolle. Der Composites United e. V. (CU) – das führende Netzwerk für faserbasierten hybriden Leichtbau – möchte den Austausch mit Anwenderbranchen intensivieren und hierfür Mitglieder und Gäste aus den Branchen ins Gespräch bringen, um Ideen für neue Anwendungen und neue Technologien zu diskutieren. Die Referentinnen und Referenten stellen ihre Projekte und Einschätzung vor und stellen sich der Diskussion mit den Teilnehmenden. Im Rahmen der Online-Veranstaltung „Verbundwerkstoff trifft Schienenfahrzeug“ im Dezember 2024 trafen sich etwa 70 Mitglieder und Gäste des CU.
„Schienenfahrzeuge Made in Germany spielen vor dem Hintergrund ihrer Energieeffizienz und der weltweit zunehmenden Urbanisierung eine zentrale Rolle beim Ausbau einer nachhaltigen Mobilität. Dabei leisten Verbundwerkstoffe wichtige Innovationsbeiträge für Leichtbau und Funktionsintegration“, so Dr. Heinz Kolz (Clustergeschäftsführer CU West) in seiner Begrüßung.
Faserverbundleichtbau für mechanisch hochbelastete Schienenfahrzeugstrukturen – Chancen und Herausforderungen
CG Rail ist ein chinesisch-deutsches Forschungs- und Entwicklungszentrum für Bahn- und Verkehrstechnik in Dresden. Innovative Leichtbaulösungen und Multimaterialbauweise mit integrierten Funktionalitäten sollen eine nachhaltige energie- und kosteneffiziente Mobilität der Zukunft möglich machen – z. B. in U-Bahnen mit vielen Starts und Stopps, aber auch in Nutzfahrzeugen oder Batteriestrukturen. Marktscreenings nach neuesten Entwicklungen und Kooperationen helfen dabei innovative Ideen weiterzuentwickeln. Mit einem 20-köpfigen Team wurden neue Leichtbaulösungen für Strukturbauteile wie Drehgestell und Wagenkasten innerhalb des metallischen Referenzrahmens entwickelt. Das Pilotprojekt „Next Generation Metro Train“ mit CFK-Lösungen stellte ein Innovations-Highlight auf der Fachmesse für Schienenfahrzeuge InnoTrans dar. Das Folgefahrzeug mit deutlichen Gewichtseinsparungen und Korrosionsbeständigkeit wird aktuell in China getestet. Das Drehgestell, welches im Flecht- und Harzinfusionsverfahren gefertigt wurde, soll in eine Kleinserienfertigung überführt werden. CFK-Profile von mehr als 20 m Länge für den Wagen werden im Pultrusionsverfahren hergestellt, welches sich für hochbelastete Strukturen bewährt hat.
Während deutliche Gewichtseinsparungen im Interieur kurzfristig zu erzielen sind, bilden Normen und Zulassungen deutliche Hürden für Strukturbauteile, da die Regelwerke auf Metallbauteile ausgerichtet sind. Die tolerierten Mehrkosten pro Kilogramm Materialeinsparung liegen deutlich unter denen in der Luftfahrt. Das erfordert hohe Anstrengungen an Kosteneinsparungen beim Material. Weitere Herausforderungen sind Brandschutz, Recyclinggerechtigkeit und die Ausrichtung der Instandhaltung auf das neue Material.
Referent: Prof. Andreas Ulbricht, Geschäftsführer, CG Rail GmbH
Funktionalisierung von faserbasiertem hybriden Leichtbau am Beispiel von GFK-Fußböden für Schienenfahrzeuge
Die Forster System-Montage-Technik GmbH aus Forst (Lausitz) ist ein etablierter Zulieferer von leichten, robusten und feuerfesten Faserverbundlösungen. Das Portfolio deckt die gesamte Prozesskette von Konzeption über Produktion und Montage ab. Die Expertise der Aufarbeitung von Systemkomponenten ermöglicht kosteneffiziente Lösungen für den Transportsektor. Während in Asien Hochgeschwindigkeits- und Regionalbahnnetze aktuell ausgebaut werden, besitzt die europäische Bahnindustrie langjährige Erfahrungen. Drehgestell und tragende Strukturen bedeuten komplett neue Fahrzeugkonzepte, wohingegen bei Interieur- und Bodenelementen niederschwellige Gewichtsvorteile durch Faserverbundkomponenten erzielt werden können. Innovationen kommen aus Erfahrungen in der Instandhaltung. Fußböden aus GFK-Sandwichstrukturen bieten Gewichtseinsparung, leichte Lagerung, Funktionsintegration wie Fußbodenheizung und Vorteile beim Thema Feuchtigkeitsempfindlichkeit. Neben Leichtbau ist die Funktionsintegration ein großer Trend in der Branche. Sensoren und Aktoren können integriert werden, das wäre bei Metallstrukturen nicht möglich. Leichtbautechnologien kommen zunächst bei Schnellzügen zum Einsatz und finden erst später ihre Anwendung in Regionalzügen, obwohl eine verminderte Masseträgheit insbesondere aufgrund des häufigen Beschleunigen und Bremsen im Regionalzug- und Straßenbahnbetrieb einen wirksamen Energiesparhebel darstellt. Das Unternehmen ist an weiteren Kooperationspartnern für Sandwichstrukturen, additive Fertigung und Klebetechnik interessiert.
Referent: Martin Plettig, Leiter F&E, Forster System-Montage-Technik GmbH SMT
Thermoplastische Schmelzpultrusion – Ideen nehmen Profil an
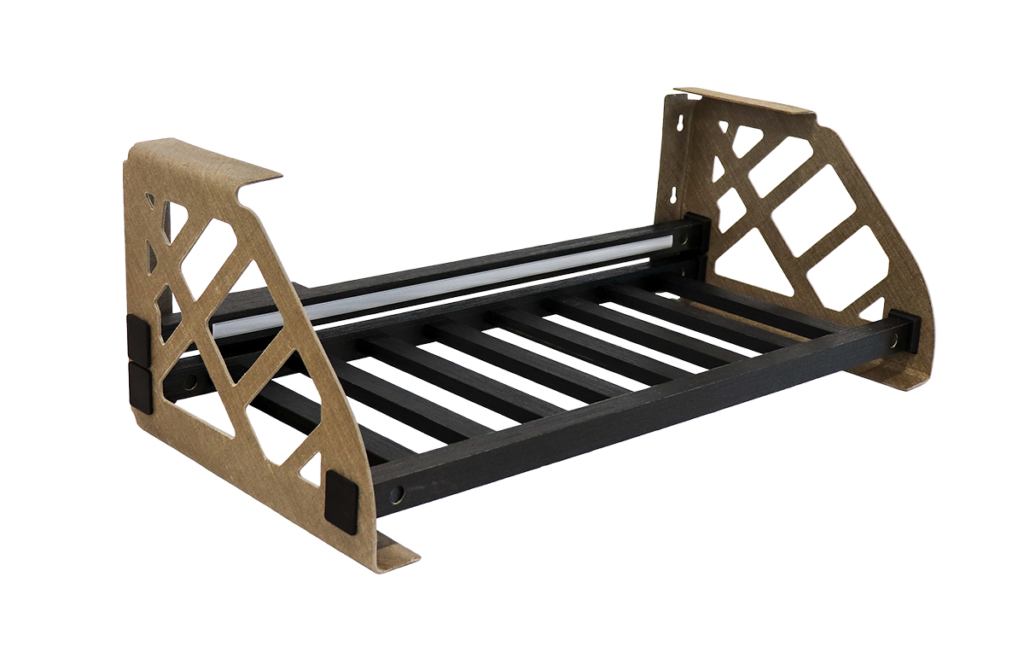
Bild: BWF Group
Die BWF Group ist ein internationaler Technologieführer für Industriefilter, Wollfilz, technischen Nadelfilz und Kunststoffprofile mit Hauptsitz in Offingen/Bayern. Wer in Europa, China oder Indien in einem Bus gesessen hat, ist garantiert mit den Produkten der BWF Group in Berührung gekommen. BWF-Fireblocker-Materialien sind in Sitzen, Kunststoff-Verkleidungsteilen, Wänden und Türen von Bus und Bahn zu finden. Imprägnierte Fließstoffe erfreuten sich eines sehr positiven Marktfeedbacks.
Angepasste Pultrusions- und Extrusionsanlagen ermöglichen die Herstellung endlosfaserverstärkter Thermoplastprofile. Es wurden Faser-Matrix-Kombinationen mit diversen Additiven – teils aus eigenem Hause – für hohe Anforderungen an Brandschutz und Oberflächengüte entwickelt. Ein Pilotpartner wird die junge Technik auf die Schiene bringen. In dem neuen Verfahren wurden die Herstellungsgeschwindigkeiten ohne Verlust bei den Kennwerten deutlich erhöht. Konkrete Anwendungsbeispiele – wie z. B. Gepäckablagen – wurden bereits auf der InnoTrans präsentiert.
Referent: Christoph Tippel, Head of Innotec by BWF Group
Verbundwerkstoffe in elektrischen Antriebssystemen von Schienenfahrzeugen
Das Leibniz-Institut für Verbundwerkstoffe in Kaiserlautern forscht, als große Wissenschaftseinrichtung, entlang der gesamten Prozesskette von Verbundwerkstoffen von der Materialentwicklung über die Konstruktion bis hin zu Produktionstechnologien.
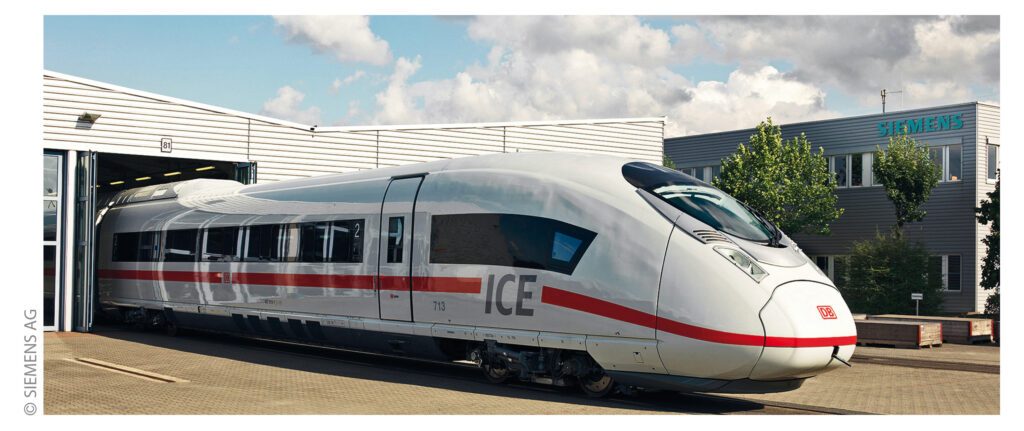
Das vorgestellte Projekt hatte das Ziel, Composite-Strukturen zur Leistungssteigung von E-Motoren zu nutzen. Ein Projektkonsortium hat verschiedene Motorteile (wie Gehäusedeckel aus Radialgewebe und Spaltrohr) entwickelt. SMC-Materialen, für einen Bereich bis 100 °C einsatzbar, mussten eigens für Temperaturen von 120-130 °C weiterentwickelt werden. Ein gänzlich neues SMC-Material ist bis 160 °C einsetzbar. Da für die Kühlung kein Wasser genutzt werden konnte, wurde ein neues Kühlungsdesign zur Wärmeabführung entwickelt. Die leichte und steife Pilotentwicklung bietet eine Steigerung der Leistungsdichte und wird aktuell vom Konsortialführer getestet.
Referent: Dr. Florian Gortner, Leibniz-Institut für Verbundwerkstoffe
Diskussion
Bessere Dämpfungseigenschaften und Korrosionsschutz bieten Anwendungsmöglichkeiten bei der Infrastruktur wie Bahnschwellen. Das End of Life muss beim Start of Life gleich mitgedacht werden. Monomaterialien bieten beim Recycling Vorteile und es stehen bereits industrielle Verfahren zur Verfügung. Neuausrichtung der auf Metallbauteile ausgerichtete Normung läuft schleppend. In zwei bis drei Jahren können Ergebnisse erwartet werden. Bei der Zulassung von Fußböden geht es mit einem halben Jahr schneller, um Schallschutz, Brandschutz und weitere Anforderungen abzuprüfen, weil Prüfinstitute mit einer guten Ausstattung zur Verfügung stehen.
Die Aufzeichnung der Veranstaltung können Sie auf dem YouTube-Kanal des CU anschauen.
Der nächste Termin unserer Reihe:
7. April 2025 „Verbundwerkstoff trifft Batterietechnik“ (14:00 Uhr, online)
Programm und Einladung finden Sie frühzeitig auf der CU-Internetseite.
Weitere Informationen erhalten Sie von:
Dr. Heinz Kolz (CU West): heinz.kolz@composites-united.com