Wood is a natural fiber composite material made from cellulose fibers and the biological matrix lignin. Due to the large proportion of pores and growth-related structural changes in the wood, however, the mechanical potential cannot be fully exploited. This might change thanks to the „Woodtrusion“ research project.
Under heat and pressure wood can be compressed, thus improving material properties, such as strength and weather resistance. In addition, the thermo-mechanical compaction enables new, non-cutting manufacturing processes for technical profiles made of wood.
If lignin and hemicellulose are first removed from the wood by chemical-thermal processes, volume reductions by a factor of 5 are possible with an analogous increase in density. After pre-treatment and compression, a twelfe-fold increase in strength could be demonstrated.
Technical solution
The aim of the Woodtrusion project was to process local thin wood into high-quality construction wood in the form of tubes. In extensive material tests, optimal process parameters for compaction degree, temperature and moisture were determined using spruce wood. The partners developed a complex system (fig. 1) that includes all process stages:
- Separation and feed line (Steinbeis Innovation Center)
- Plasticizing and compression line (Niemeier Fahrzeugwerke)
- Winding and fixing section (STFI e. V.)
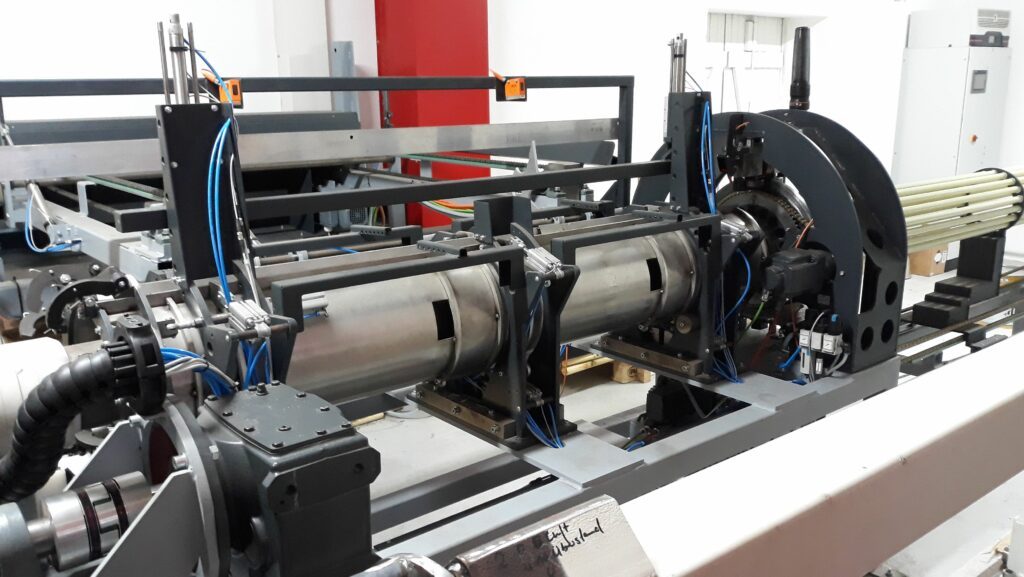
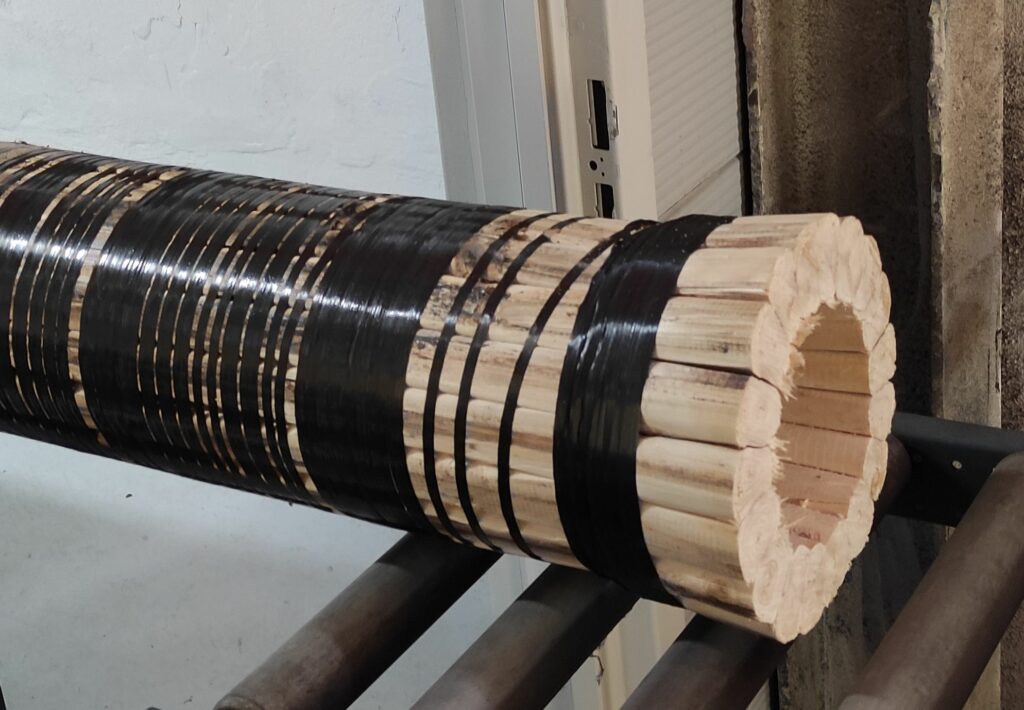
Process sequence
Round profiles made of thin wood are fed into a revolver magazine with a length offset in order to avoid weak points in the tubes. The system can work quasi-continuously due to the alternately used magazines.
The logs are heated up to 120 – 140 °C and compressed in a newly developed compression molding tool. To compensate for the restoring forces of the wood at the press mold outlet, a orbital winding unit was integrated, that can hold two coils offset by 180°.
50K carbon fiber towpregs (SIGRAFIL® C T50-4.0240E100) were used for wrapping, the resin system. The thickness of the reinforcement can be adjusted by altering the speed of the winding unit. In this specific case, a two-layer reinforcement with a wall thickness of app. 1mm was applied. Without reinforcement, the pipe expands when leaving the plant (fig. 2).
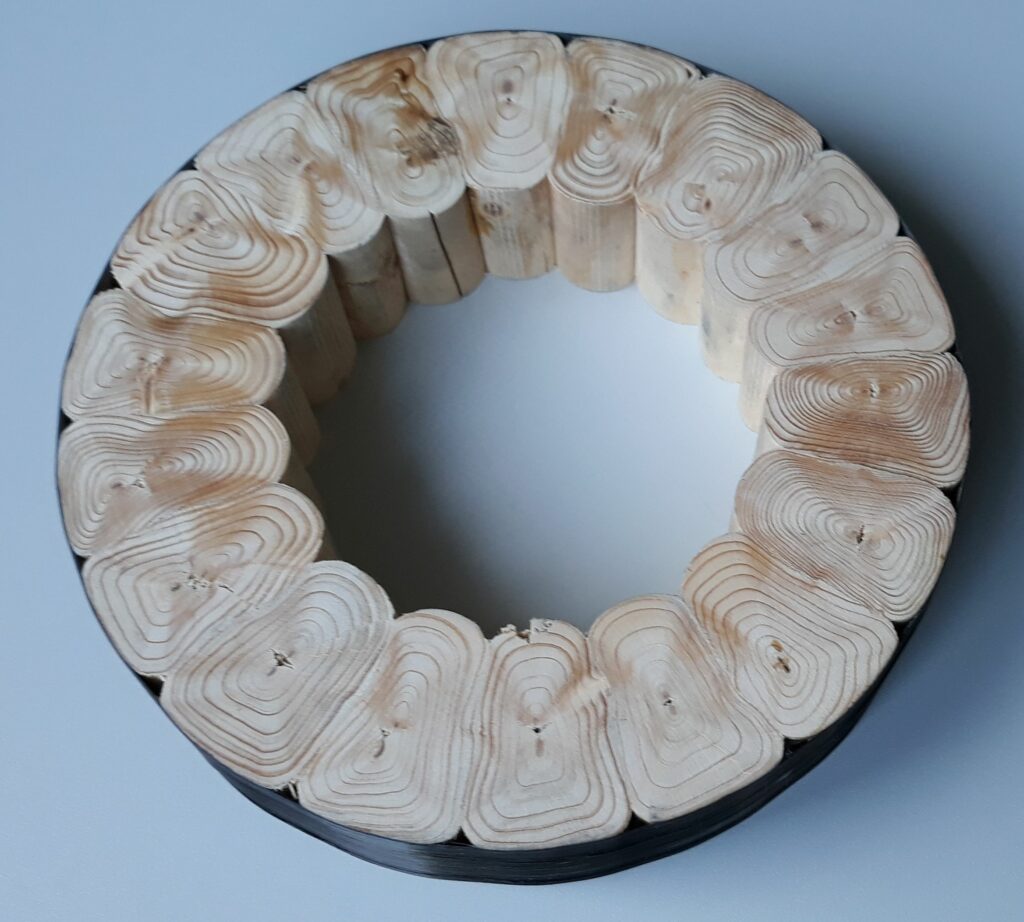
Application options
With the system, fiber-reinforced wooden tubes (fig. 3) can be manufactured in any length. Possible applications are e.g. in construction as an alternative material for columns made of steel. A final laminate structure using the winding process is possible for adaptation to the respective application and the corresponding type of load (fig. 4).
Contact:
Sächsisches Textilforschungsinstitut STFI e. V., Chemnitz
Dipl.-Ing. Günther Thielemann
+49 371 52 74-239
guenther.thielemann@stfi.de
www.stfi.de
Niemeier Fahrzeugwerke GmbH (ehem. STM Montage GmbH), Lunzenau
Dipl.-Ing. Tom-Egmont Werner
+49 37383 74 98 24
wernert@niemeier-fahrzeugwerke.de
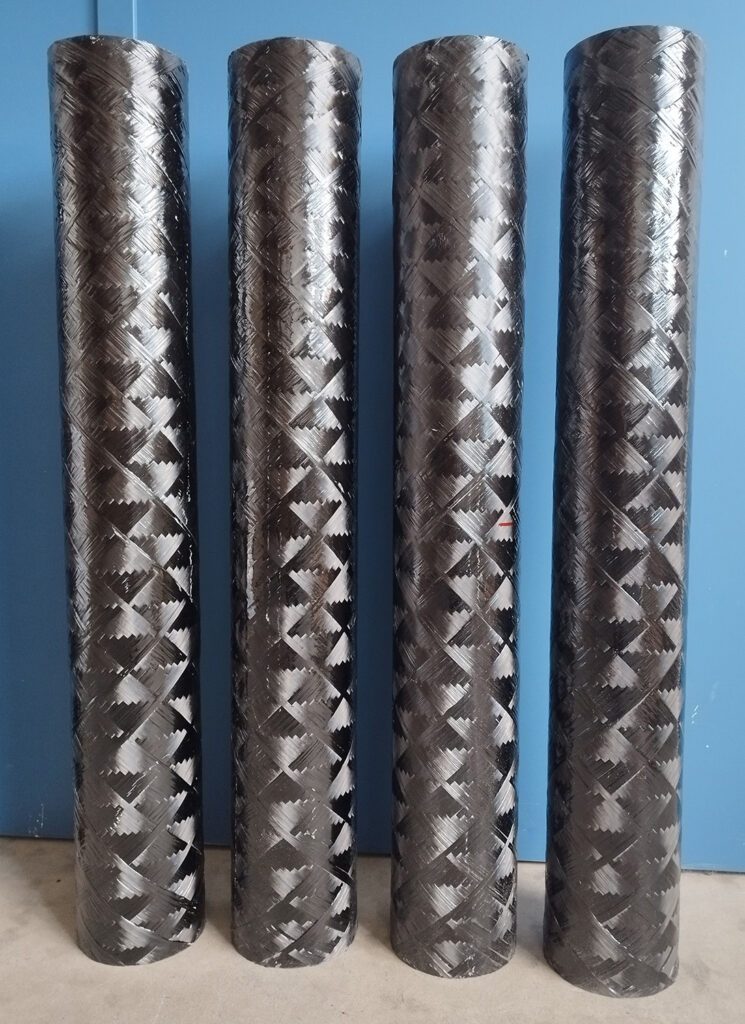
We would like to thank the Federal Ministry of Food
and Agriculture for funding the funding project (FKZ 22009217) and the project sponsor, the Agency for Renewable Resources.