CU member Institute for Lightweight Enginieering and Polymer Technology (ILK) of the TU Dresden puts automated process chain for the production of composite metal hybrid components into operation – important milestone reached in the hypro project.
Hybrid parts made of fibre-reinforced composites, plastics and metals are particularly suitable for highly loadable and geometrically complex lightweight structures. By using thermoplastics with short and continuous fibre reinforcement, cycle times of well under one minute can be achieved, which predestines such solutions for high-volume production. However, in order to ensure a highly resilient bonding of the monolithic substructures, a careful pretreatment of the structures – especially of the metallic elements – is necessary. Therefore, the production technology for this type thermoplastic composite (TPC) metal hybrid components (TPC metal hybrid components) is currently barely competitive.
The BMBF-funded project “hypro – Holistic implementation of hybrid design methods in series production” addresses precisely this gap and thus helps to further deepen the understanding of the production of thermoplastic FKM hybrid structures suitable for series production. To this end, the project consortium, coordinated by Brose Fahrzeugteile SE & Co. KG, Bamberg, designed a fully automated process chain for the series production of FKM hybrid components. With the successful ramp-up of this complex process chain, an important milestone has now been reached in the project on the way to the series-ready and competitive production of hybrid components. In more than nine months of intensive work, a fully automated system was created in the process development centre of the Institute for Lightweight Enginieering and Polymer Technology (ILK) of the TU Dresden, which for the first time enables the production of TPC metal hybrid components in cycle times of one minute.
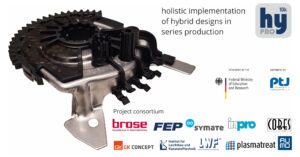
The set-up system is based on an injection moulding combination process in which preformed metal inserts are combined with preconsolidated TPC patches and then overmoulded with short-fibre-reinforced plastic. To ensure an optimal bond between the polymer components and the metal insert, the latter is cleaned and coated inline using plasma. To activate the adhesion-promoting plasma coating, the metal insert is heated by induction within a few seconds during transfer into the injection mould. Once correctly tempered, it is pressed with the TPC patch and then overmoulded. The individual process steps are coordinated via a central control unit. This monitors the status of the components and moulds, actively readjusts the process parameters and thus reacts to process fluctuations, such as changes in heating rates. This ensures that both the TPC patch and the metal insert are joined in clearly defined states and thus repeatedly with high quality. At the same time, the higher-level process control system continuously records more than 350 sensor channels for all relevant process, quality and environmental data, which are then stored individually for each component in a database. The resulting extensive database (approx. 10,000 parts will be produced in the coming weeks) enables comprehensive process studies and the elaboration of relevant parameters for the economic production of highly resilient hybrid components. In this way, the goal of the project consortium is within reach: the transfer of the thermoplastic TPC metal hybrid construction method into large-scale production processes with cycle times of less than one minute.
The joint project hypro, funding code 03XP0284A-J, is funded by the Federal Ministry of Education and Research on the basis of a resolution of the German Bundestag under the supervision of the Project Management Organisation Jülich PTJ.
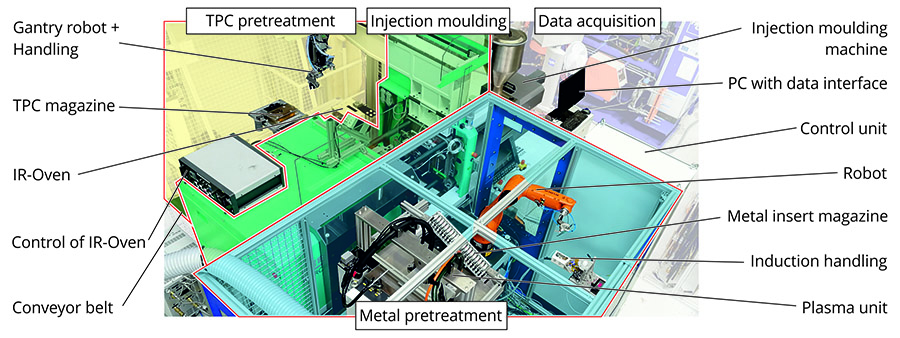