Bionic design principles for an efficient and sustainable lightweight construction
In the field of nature-based sports, the idea of sustainability has been deeply anchored in the DNA for ages. Based on this approach, the Institut für Konstruktion und Verbundbauweisen (KVB) and the High Tech Sportgoods Production GmbH (HTSG) took on the challenge of developing a kiteboard from recycled materials as part of a ZIM research project.
In the project the focus was on a recycled carbon fiber fleece (rCF) in particular, which is made from production residues and other recycled carbon fibers in order to contribute to the development of a circular economy in the composite sector.
To ensure a highest possible degree of recyclability after the end of product life, a classic wooden or plastic core inside the sports equipment was deliberately avoided. However, a board made entirely of recycled fibers would theoretically weight 3,5 times as much as classic fabricated boards with the same property profile. On the other hand, a minimum of weight is aimed for dynamic handling and higher jumps.
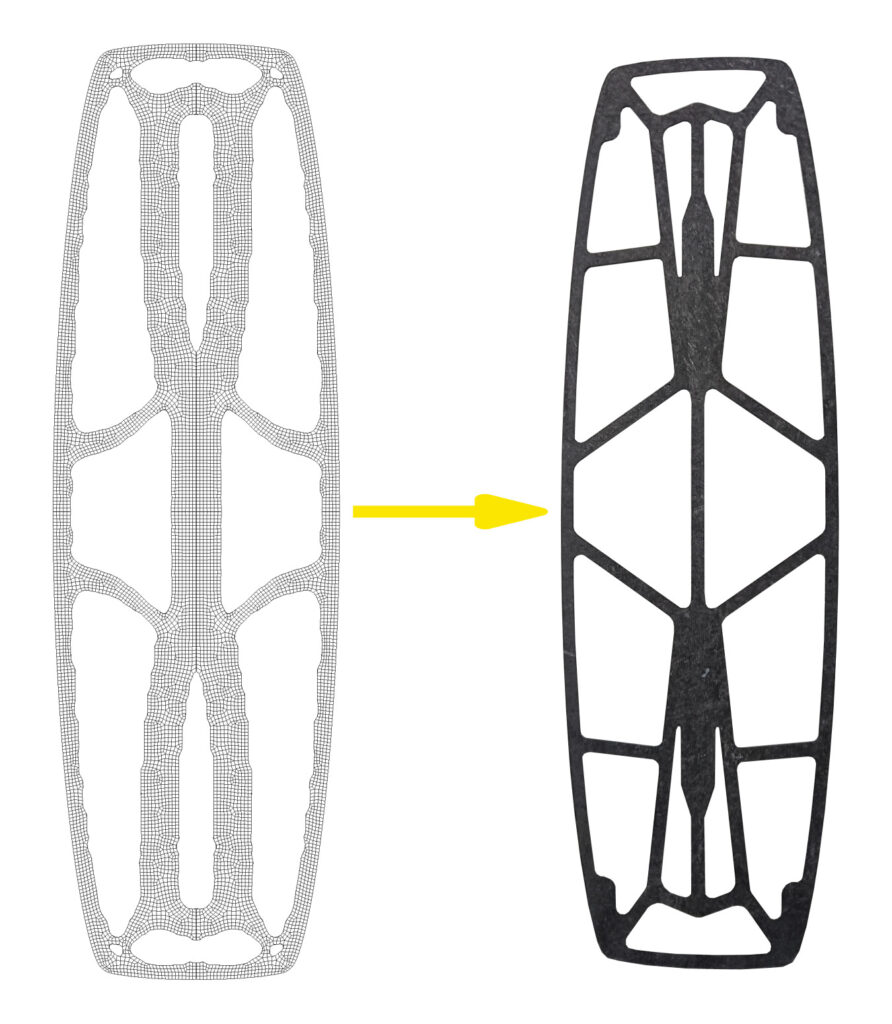
Bionic approaches to save weight
The solution in this case was to develop of a skeletal core that ensures the necessary distance between the outer layers. A topology optimization was carried out according to the principles of bionic design. Depending on the set load assumptions, boundary conditions and target function, different characteristics of the skeleton geometry were formed. The finally optimized basic design was then taken up and converted into a production-ready geometry, taking into account the necessary interfaces for fins, bindings and carrying handles.
No loss of properties due to mono-material construction
A significant advantage of rCF textiles is the qusi-isotropic the profile of mechanical properties. In this way, for example, threads for all add-on parts can be integrated directly into the material. Various concepts for the integration of the threads during the manufacturing process were developed and validated in a subsequent pull-out test. It was observed that the pull-out forces with the same thread length are on a similar level to those of conventionally installed metallic load application elements. Additional long-term tests on the water impressively confirmed the results.
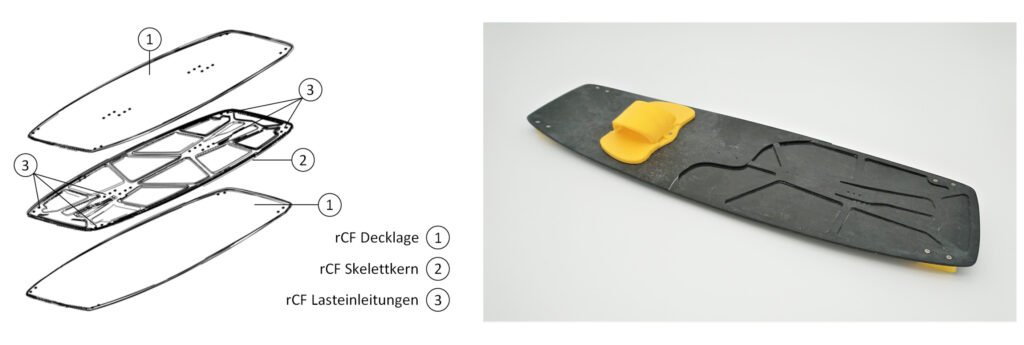
Same or better in all areas
Moreover, laboratory tests of the skeleton core board demonstrator showed the same mechanical properties as conventionally manufactured boards with the same weight and an improved CO2 balance. Based on the knowledge gained during the research project, fleece materials are already being used in serial production boards of the sports equipment manufacturer.
Basically, the potential of recycled materials in structural applications could be demonstrated with the project. For a holistic, all-encompassing circular economy, further innovative solutions will be necessary in a wide variety of application areas in order to breathe new life into all components made of fiber composite materials after the end of their life cycle.
Contact:
KVB Institut für Konstruktion und Verbundbauweisen gGmbH, Großweitzschen
M.Sc. Martin Zießler
Wissenschaftlicher Projektleiter | Scientific Project Manager
+49 3431 734 25 95
martin.ziessler@kvb-forschung.de
www.kvb-forschung.de