Interdisciplinary research was carried out in order to transfer knowledge on fibre placement from aircraft construction to architecture for lightweight structural construction. IFB, ITKE and IGVP combined their expertise to make the Tailored Fibre Placement process usable for architecture. A special focus was placed on the use of bio-based materials.
The aim was to transfer the TFP textile preforming process to architectural applications and to adapt design methodologies accordingly. TFP is classically used in aerospace applications or in special solutions for structural components subject to high loads. It is an extremely low-energy
process for near-net-shape and load-pathadapted fibre placement, and is used for quantities ranging from 1 to large-scale production. Flax fibres were used as reinforcement fibres, as they are available in sufficient quantities and in technically high quality, as well as having similar
mechanical properties to glass fibers.
Biodegradable materials
Partially bio-based epoxy resins were used as a matrix. They meet mechanical requirements and are partially CO2 neutral, but are not biodegradable. Thanks to the IGVP, it was possible for the first time to use the new matrix system chitosan in a water-based process. This polymer is based on chitin, the world‘s second most common biopolymer, which is found mainly in fungi and shellfish, and is biodegradable.
Design and manufacturing
Modern, individual building geometries were considered through parametric designs. Parallel mouldless curing methods and/or adaptive tooling moulds were developed, as each individual component of an overall structure can have a different geometry.
Design is layed-out to using the least amount of material, as well as shaping without complex tools, and considering the manufacturing boundary conditions of TFP. Bionic structures and physical principles served as the basis for the algorithms used to calculate the fibre paths
and geometries.
Particularly noteworthy is the successful application of the principle of curved folding, as it allows the production of flat preforms that can be transformed into multi-curved structures without high degrees of forming.
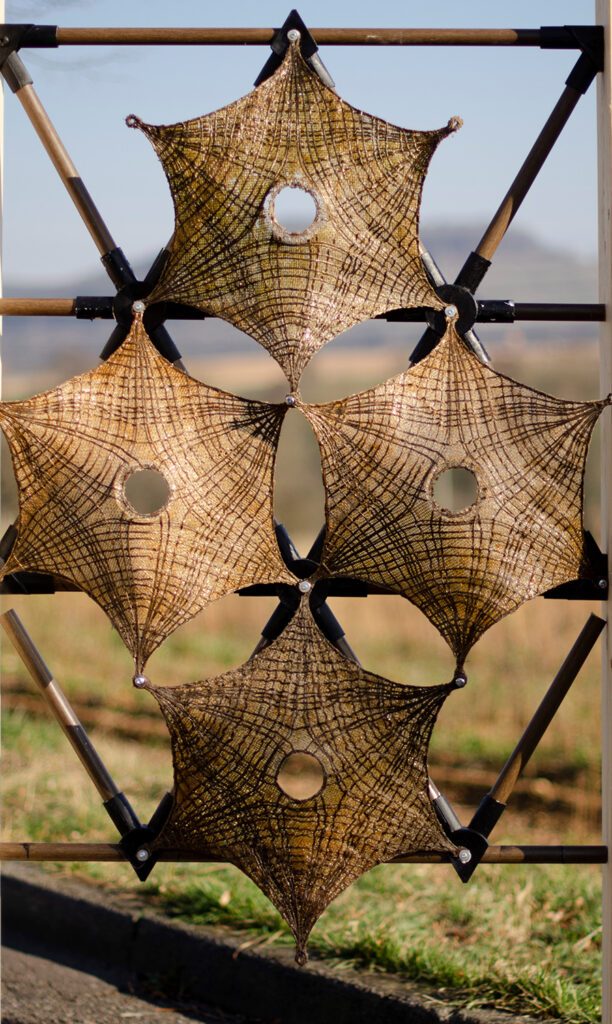
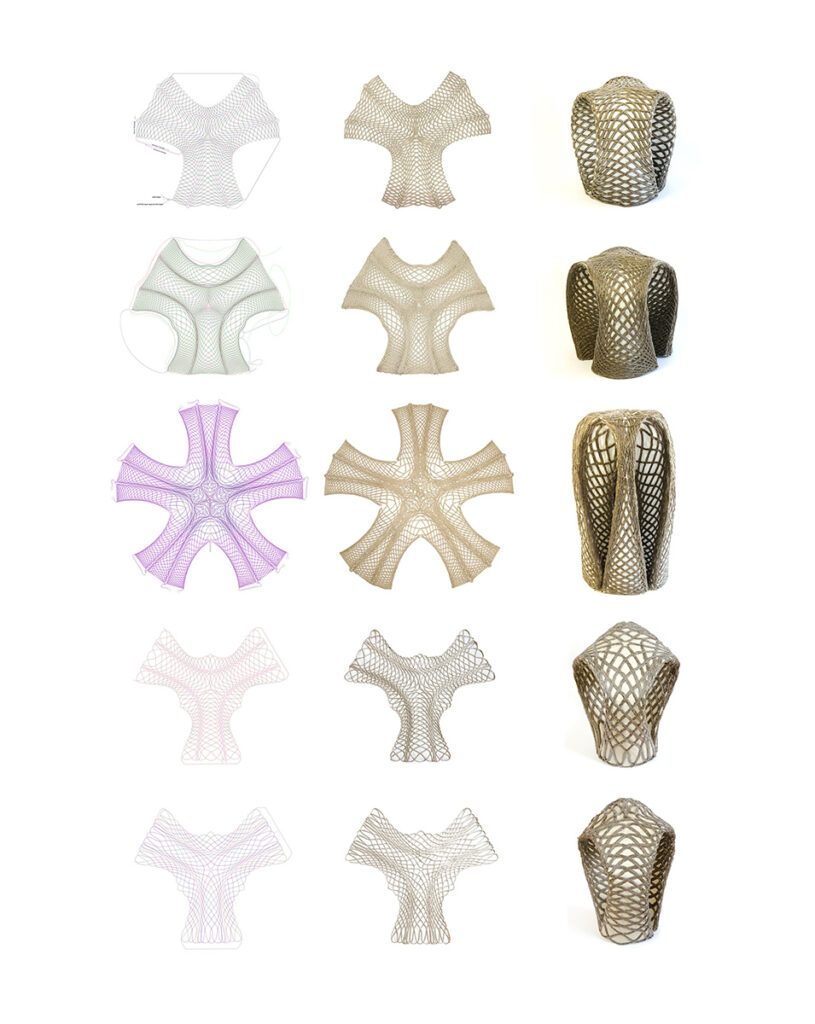
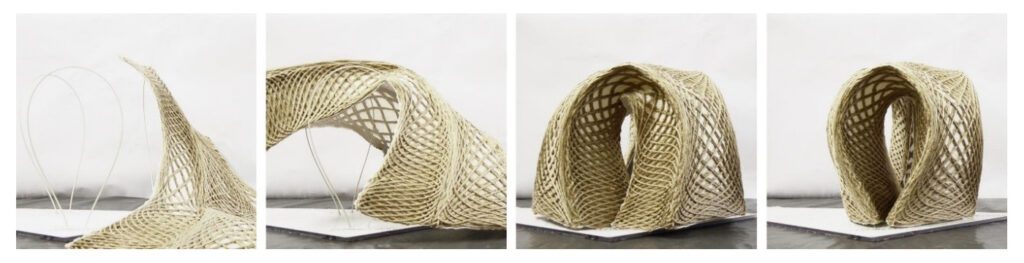
Within the framework of close co-operation, over the past five years researchers and students from three Stuttgart University institutes have been working together on new concepts, processes and materials for the production of sustainable lightweight architectural elements.
Partners were: 1) Institute of Aircraft Design (IFB), 2) Institute of Structures and Structural Design, Deparment of Bio-based Materials and Material Cycles in Architecture (BioMat at ITKE), and 3) Institute of Interfacial Process Engineering and Plasma Technology (IGVP).
Contact:
University of Stuttgart | www.uni-stuttgart.de
Institute of Aircraft Design (IFB)
Institute of Structures and Structural Design (ITKE-BioMat)
Institute of Interfacial Process Engineering + Plasma Technology (IGVP)