Textile-reinforced CFRP pultrusion profiles for ultra-light frame structures in vehicles
CFRP profiles produced by pultrusion, for example, allow a substantial mass reduction for frame structures in rail or commercial vehicles at low costs. CG Rail GmbH has consistent
know-how from the pultrusion process up to the design of frame structures.
The holistic approach ranges from mould design and process simulation for individually designed pultrusion profiles, including subsequent process testing on a company-owned machine (fig. 1), up to the design and simulation of frame structures made of such profiles. The functional requirements
as well as the multi-dimensional stress conditions of frame structures in vehicles often require the realisation of complex profile cross-sections with textile reinforcement.
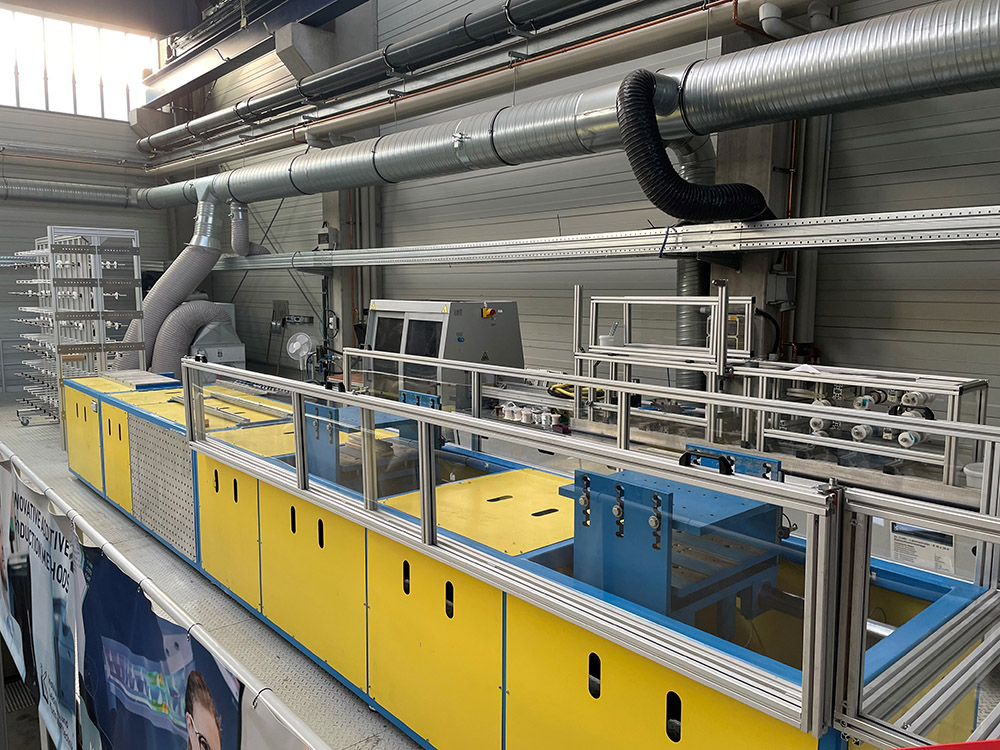
Process development pultrusion
The process development for such profiles is largely based on numerical simulations as well as on tests to determine suitable geometries (e. g. feeding devices and moulds) and process parameters that enable wrinkle-free guidance of the impregnated textiles in the process.
Fig. 2 shows an examplary comparison of numerically and experimentally obtained results for the feeding of CF multiaxial fabrics. The high non-linearity regarding material behaviour, geometry and boundary conditions requires special know-how for FE simulation. Furthermore, special tests for the mechanical material characterisation of the (impregnated) textiles are usually required. The range of already realised profile cross-sections with textile reinforcement extends from closed hat profiles to complex multi-chamber profiles with wall thicknesses of more than 20 mm (fig. 3).
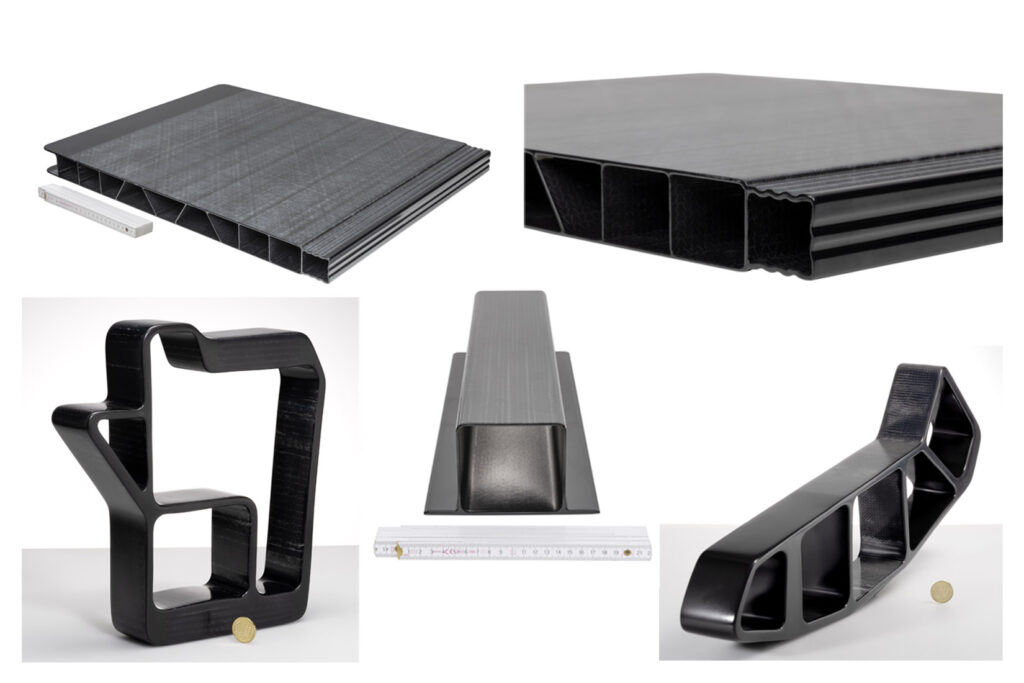
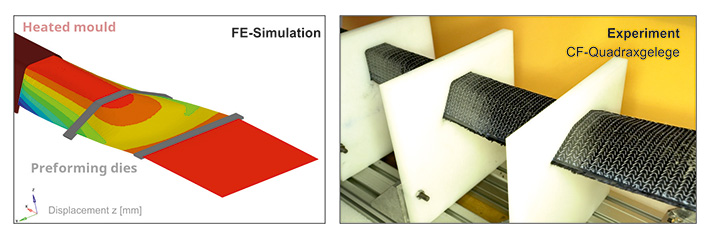

Lightweight frame structures
Within the scope of industrial projects, CG Rail GmbH has already successfully realised several highly stressed lightweight frame structures made of CFRP pultrusion profiles. An impressive example is the car body of the world‘s first metro in carbon-intensive lightweight design, Cetrovo.
Its structural backbone is formed by more than 20 m long CFRP pultrusion profiles, which are positioned longitudinally in the corners of the car body and serve primarily to carry the
longitudinal forces and bending loads (fig. 4). These profiles are connected to each other in the side wall via the door pillars and CFRP sandwich structures in between. The mass saving compared to the metal car body is about 30 percent.
Contact:
CG Rail GmbH, Dresden
Prof. Dr.-Ing. Andreas Ulbricht | Managing Director
+49 351 41 67 30 03
andreas.ulbricht@cgrail.de
www.cgrail.de