At the CU Innovation Day on May 4, 2023 in Herzogenrath, everything revolved around Automated Fiber Placement (AFP). In this fully automated manufacturing process for composite parts, fiber-reinforced plastic tapes are robotically placed on the surface of the mold using pressure and temperature along a predefined path. There are now a number of technologies for automated robot-assisted placement of composites that can be considered not always in competition but also complementary, as they develop their potential differently in different applications. Together with the speakers and guests of the event, the special features, advantages, boundary conditions as well as challenges of the different technologies were discussed.
The working groups “Manufacturing Processes”, “Automation”, “Artificial Intelligence” and “Additive Manufacturing” of Composites United (CU) had invited to this theme day. The host was the company Conbility GmbH, a startup of the technology location Aachen. Dr. Michael Emonts, one of the Conbility founders, and the two organizers of the Innovation Day, Dr. Thomas Heber (Managing Director CU Ost) and Dr. Heinz Kolz (Managing Director CU West), opened the event, which was fully booked with 40 international guests, and welcomed participants from six European countries.
Under the title “Conbility Turn-Key Machines for Laser-assisted Tape Placement & Winding”, Dr. Emonts presented his company’s system technologies. Conbility GmbH from Herzogenrath offers machine systems for automated FRP production technologies. The product portfolio includes multifunctional tape laying and winding heads that can process laser-assisted thermoplastic tapes as well as thermoset pregregs and dry fiber rovings. In addition to individual applicators, Conbility offers turnkey and laser-safe manufacturing cells for tube and pressure vessel winding as well as 2D and 3D tape placement. Customer applications for Conbility machines include the production of consolidated thermoplastic laminates for further processing by thermoforming and back injection, the production of cost-effective lightweight components with local UD fiber reinforcements, and the production of thermoset or thermoplastic composite pressure vessels. A second business area comprises technology consulting and cost as well as life cycle analyses including CO2 footprint analyses with the intuitive “OPLYSIS” software developed specifically for this purpose.
Other topics and presenters included:
- The XCell, a compact and accessible AFP solution by Chiemi Avila Mori, Carbon Axis, France
- 3D robot tape layup by Wilhelm Rupertsberger, FILL, Austria
- F2-Compositor® – Scalable Platform for Printing Thermoplastic-Tape-Preforms by Dr. Markus Steeg, Automation Steeg & Hoffmeyer
- Flexible Fiber Placement Systems – the STAXX-Family by Raphael Reinhold, Broetje-Automation
- VRA – the tape laying machine for large-scale production of automotive CFRP-parts by Mario Krupka, Voith Composites
- Latest trend in MTorres AFPs. From serial production Gantries to robotics R&D by Manu Motilva, MTorres, Spain
- CATFiber V2 DFM: bringing AFP into design stages to optimise composite parts for automated manu-facturing by Thierry Couvin, Coriolis Composites, France
In the course of the day, the guests were repeatedly surprised at how differently solutions for automatic fiber placement can be designed depending on the application. Requirements for systems result, among other things, from the respective specifications with regard to the investment budget, the space limitations for the system, the laying speed, the component size, the precision requirements, and the degree of automation. The applications presented ranged from small high-precision components and vehicle parts to complete aircraft wings.
Breaks for individual exchange and networking as well as a live technology presentation at the host Conbility followed by a guided tour through the AZL Aachen rounded off the Innovation Day.
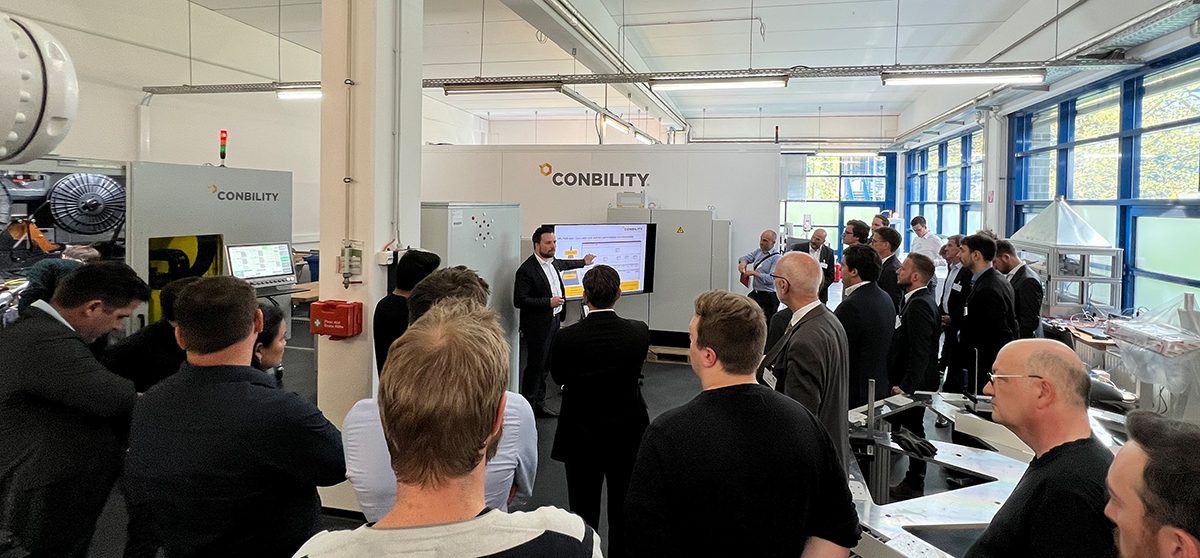
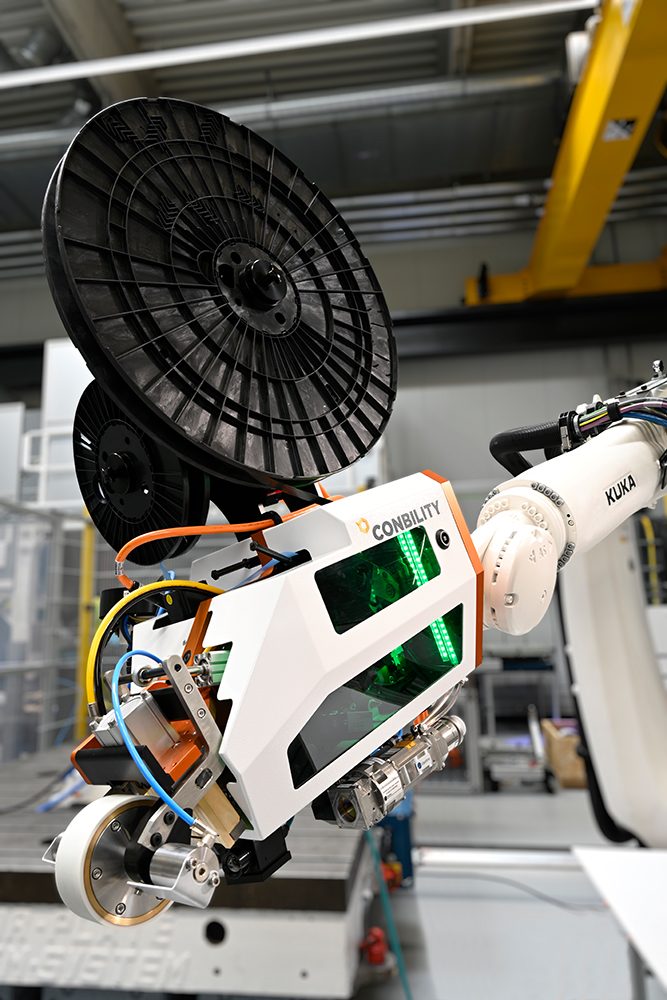
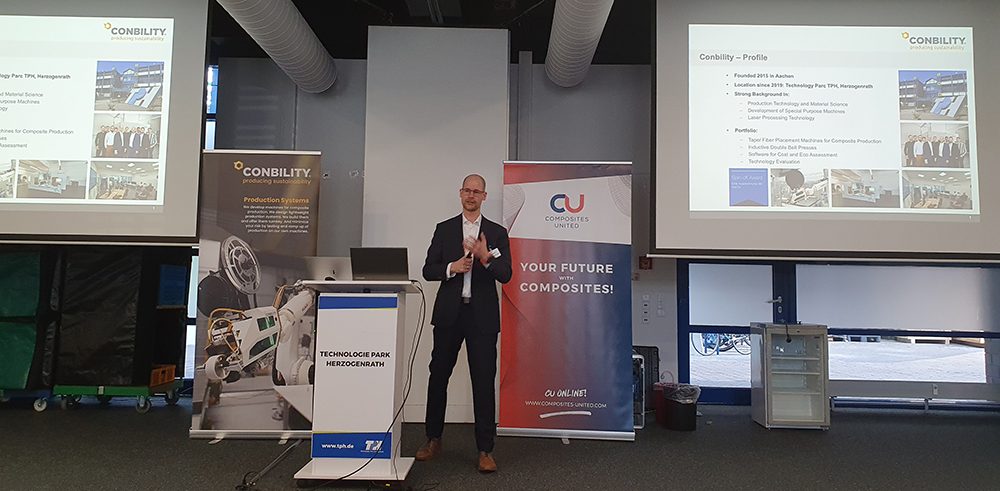
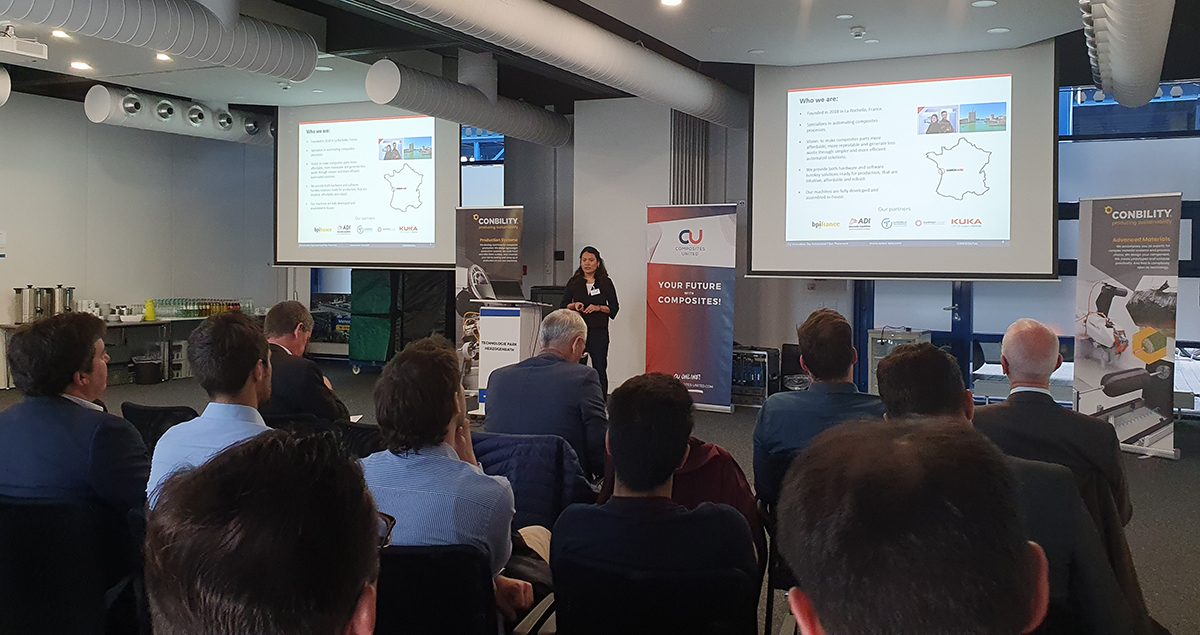
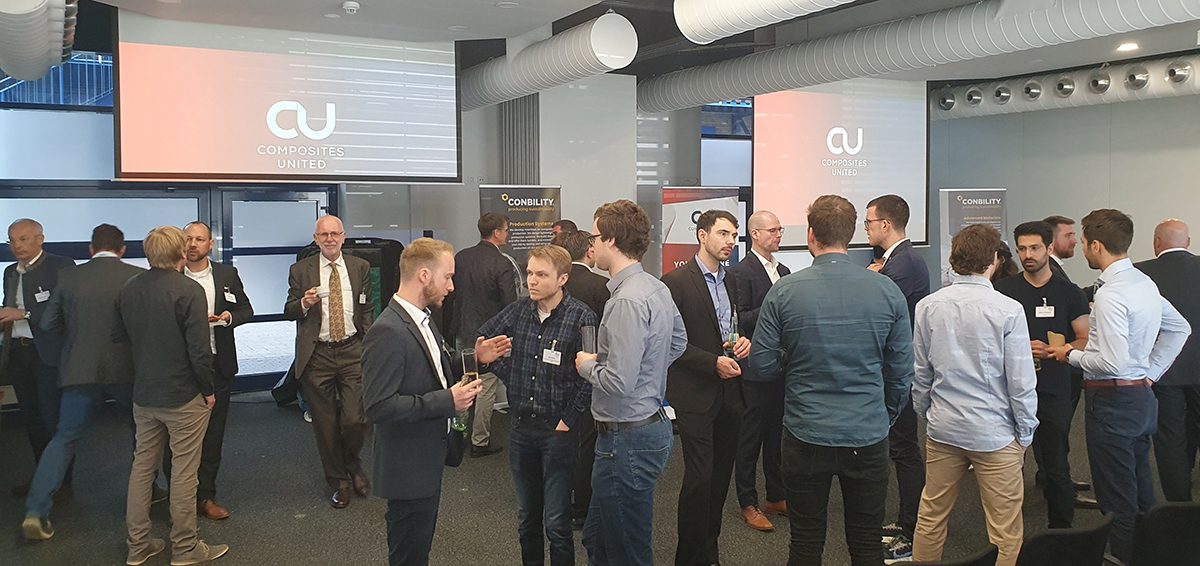
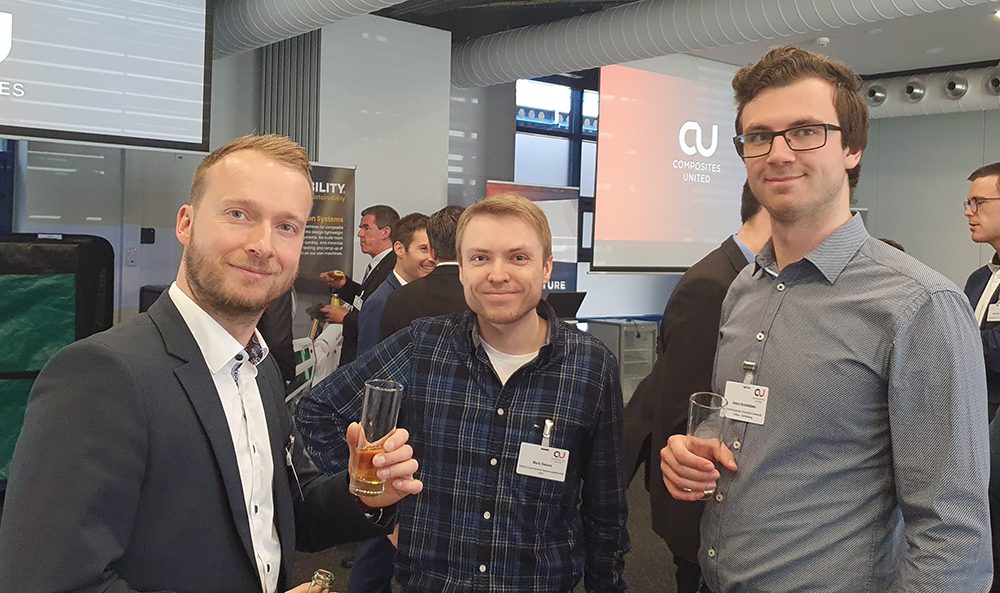
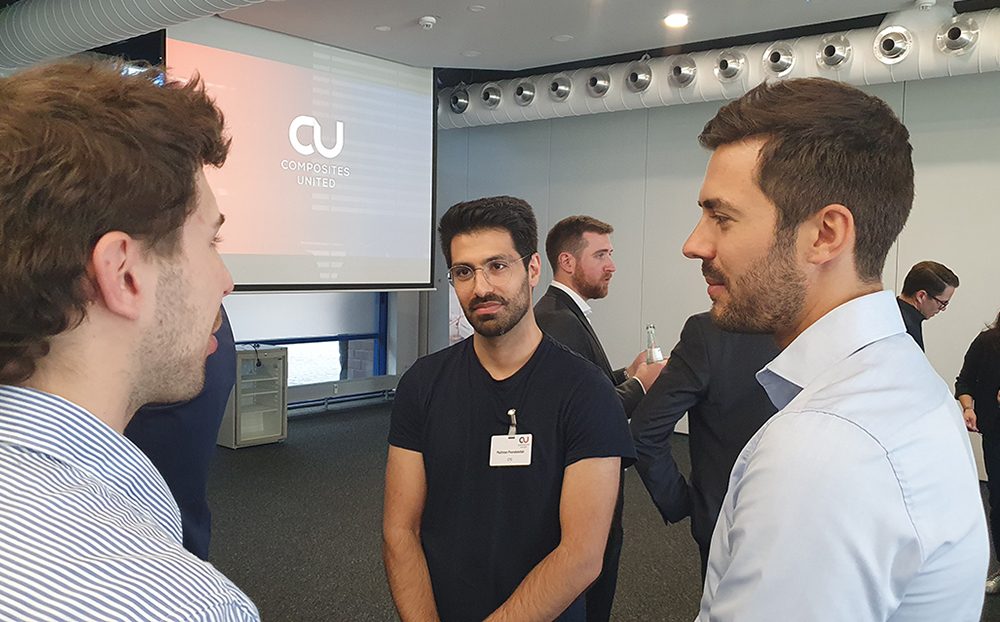
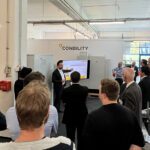
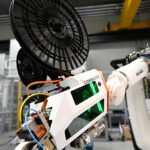
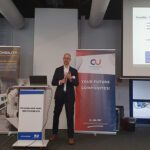
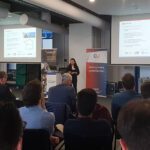
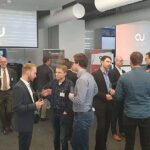
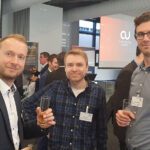
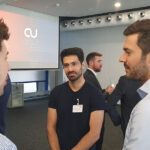