The path to recyclable fiber materials might well be short – and a win-win for everyone
The combination of sustainable fiber materials with efficient manufacturing processes for semi-finished textile products enables the production of cost-effective reinforcement materials for lightweight design applications – all the more so when there are no long transport routes to contend with.
All of today’s lightweight products strive to use as few resources as possible. However, materials with little or no recyclability are often used. Though it might sound a little presumptuous to claim that Hans Carl von Carlowitz had modern fiber composite lightweight design in mind when he coined the term sustainability in 1713 – but with his work he identified renewable raw materials as an indispensable component of a circular economy even back then.
Regional value creation
Hemp and flax fibers have already become classic reinforcing fibers. They are recyclable, sustainable and have a property profile comparable to typical semi-finished glass fiber products. A regional value chain, in which the fibers are grown and processed close to the processing location – in the case of Hightex Verstärkungsstrukturen GmbH: in Saxony – further improves the ecological footprint of these natural fibers.
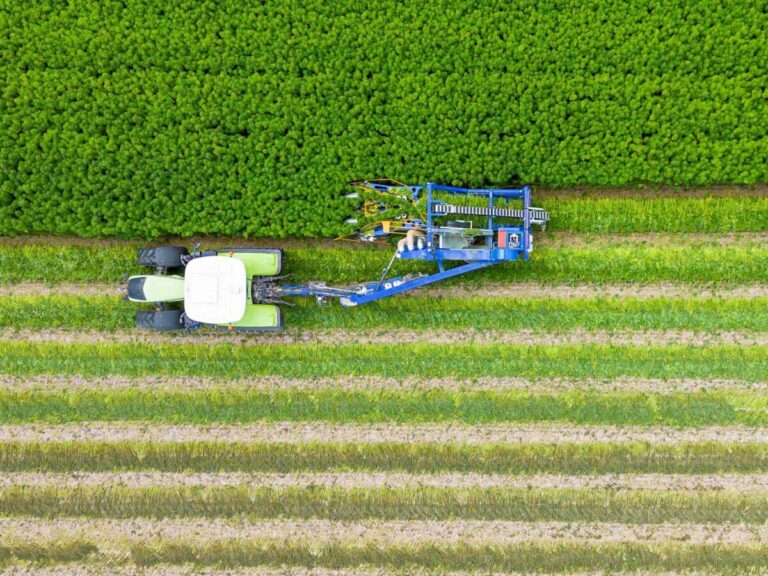
Regional cultivation of raw materials – flax harvest in Saxony / © Cretes
Innovative textile processes
To date, the Tailored Fiber Placement (TFP) process has mainly been used for the precise placement of fibers, especially high-performance fibers, that are oriented according to their load-bearing capacity.
Hightex has further developed this process into Tailored Fiber Placement high Volume TFP(hV). The new process generation enables processors to replace existing reinforcement systems made of woven or non-crimp fabrics with TFP(hV) preforms – even in large quantities. And with a lower specific weight and a significantly improved price-performance ratio.
Novel applications
The combination of cost-effective preforms with recyclable fiber materials is suitable for existing and new applications. Users, designers and processors of textile fiber reinforcements can develop sustainable products with natural fiber-reinforced preforms without having to change their processes or component designs.
The preforms manufactured using TFP(hV) not only offer the option of choosing the technical parameters as freely as possible, but also completely new approaches to visual design through textures and patterns. This opens up unique and completely new possibilities of component design for customers from the automotive sector, the sports and leisure industry and architecture, for example.
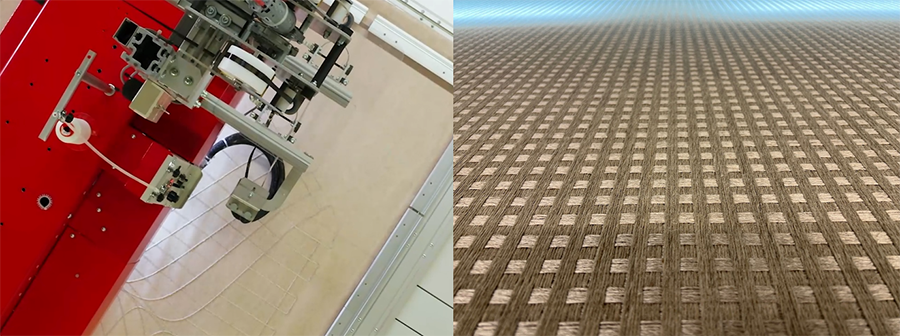
Processing on embroidery machine (l.), flax-based TFP(hv) semi-finished product (r.)
Contact:
Hightex Verstärkungsstrukturen GmbH, Klipphausen
Kai Steinbach
Sales Manager
+49 35204 39 30-189
steinbach@hightex-dresden.de
www.hightex-dresden.de