Welding the world’s first thermoplastic aircraft fuselage
As part of the Clean Sky 2 program, Fraunhofer in Stade, Germany, is demonstrating the assembly of the world’s largest thermoplastic aircraft fuselage. The challenging research project uses various welding processes, automation technologies and new materials to increase efficiency in high-rate production and fuel efficiency by reducing weight.
As part of the Clean Sky 2 project Large Passenger Aircraft (LPA), the Fraunhofer-Gesellschaft in Stade is working with international partners on the Multi Functional Fuselage Demonstrator (MFFD), the world’s first thermoplastic CFRP aircraft fuselage segment. By welding 8-m-long thermoplastic CFRP half-shells along the two longitudinal seams, a fuselage segment with a diameter of around 4 m is created.
Pre-integration and welding technology
Compared to the riveting process the CO2 laser welding process developed by Fraunhofer for the longitudinal seam enables weight reduction and dust-free joining. The need for this arises from the first-time pre-integration of both shells with many structural and system components that are also joined by welding, which would not allow subsequent removal of dust and chips. The innovative design of the MFFD needs significantly less rivets. In future, this will lead to a high increase in efficiency in high-rate production and improve fuel efficiency.

MFFD assembly research platform with integrated thermoplastic fuselage shells at Fraunhofer in Stade, Germany
Automated high-precision assembly
A research platform for automated assembly was developed and set up at the CFK NORD in Stade. The platform comprises a central plant and process control system into which technology modules from other project partners are integrated. The high-precision positioning of the two shells in relation to each other is carried out by ten hexapod robots, which use laser sensors to set the optimum shape and position of the shells and readjust them if necessary.
For CO2 laser welding, CFRP straps up to 4.5 m long are guided and positioned precisely on the seam using a strap handling tool and fed to the attached welding head. The welding head moves along the seam and melts its surface. The strap handling tool then presses the strap against the upper and lower shell joints using a pressing unit with joining forces of up to one ton. To prevent damage to the fuselage structure due to the high joining forces, a special device for force absorption and dissipation supports the shell welding regions within the resulting fuselage sections.
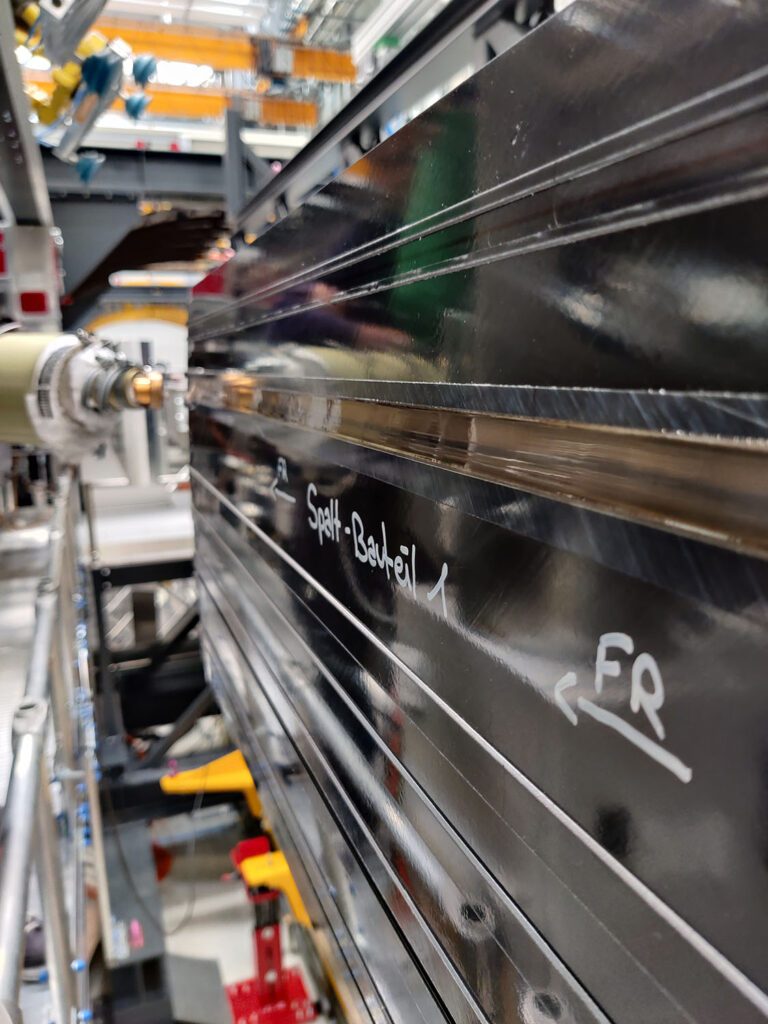
Gap filling process – filled gap by extruder on a segment of the thermoplastic CFRP fuselage shell
An extruder automatically fills the gaps resulting above and below the straps. After each welded strap, it is guided along the previously created connecting seams, heats the initial granulate and conveys it to the gap via a screw. A special nozzle ensures that the material fills the gap before it hardens in the air. In advance, a 2D sensor integrated in the same end effector measures the local gap volume and transmits this information to the extruder system. Thus, the discharge rate is calculated dynamically during the process so that irregular gaps of 3 – 11 mm in width are filled with the exact amount of molten thermoplastic matrix material required at each position.
Funded by Clean Aviation Joint Undertaking (JU), co-funded by the European Union.
Contact:
Fraunhofer Institute for Manufacturing Technology and Advanced Materials IFAM, Automation and Production Technology, Stade
Dipl.-Ing. Leander Brieskorn
leander.brieskorn@ifam.fraunhofer.de
Dipl.-Ing. oec. Benjamin Diehl
benjamin.diehl@ifam.fraunhofer.de
+49 4141 787 07-0
www.ifam.fraunhofer.de/stade