Infiltrated TowPregs in production processes and applications
The interest in the Infiltrated Towpreg System from M+A Dieterle is already growing shortly after the presentation of the technology at the beginning of this year. The first applications in winding techniques are being developed. These TowPregs have the advantage that they can be infiltrated directly before processing, so the added value remains with the user.
For individual applications, it is possible to work independently of large suppliers and to react flexibly to customer wishes.
Winding in architecture
The Towpregs have been successfully tested by FibR in their manufacturing process. FibR is a construction company that specialises in the implementation of architectural fibre composite structures for load-bearing structures, facades, and interiors.
Based on a digital design and manufacturing process, robot-controlled production facilities are operated, which spatially deposit impregnated fibres to create the corresponding structures. The products are customised and often have a wide variety of requirements for the material combinations.
FibR Production and Development Manager, Dr.-Ing. Julian Fial, points to the potential: “We have already successfully tested the material in various versions. Our goal is to integrate the material into our production process and also have the value creation of impregnation in-house.”
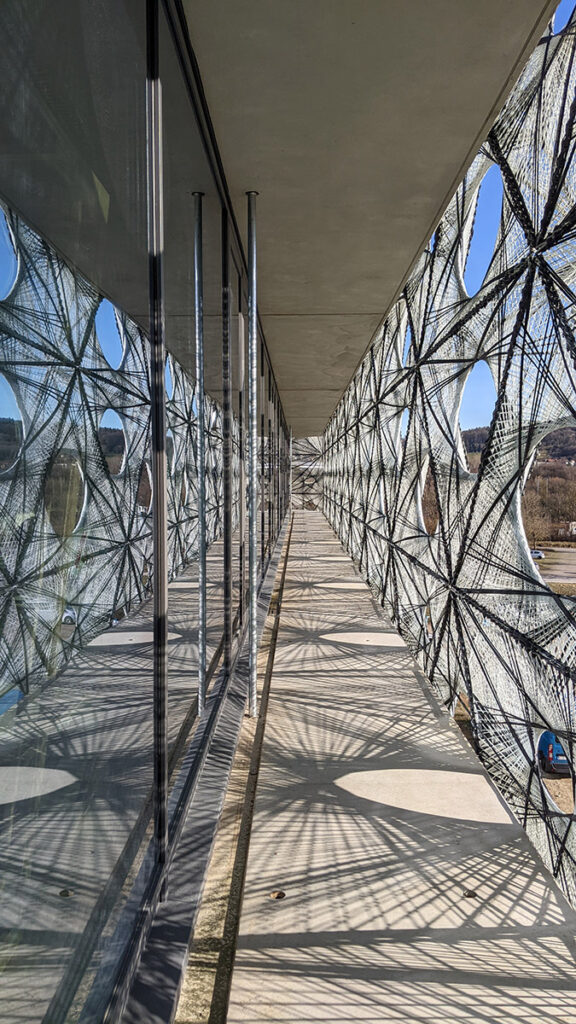
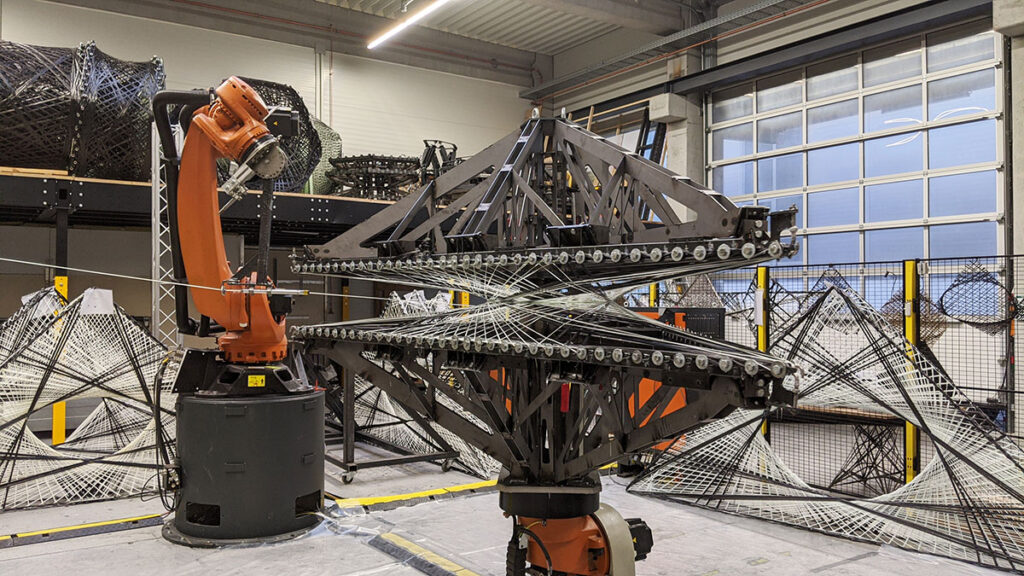
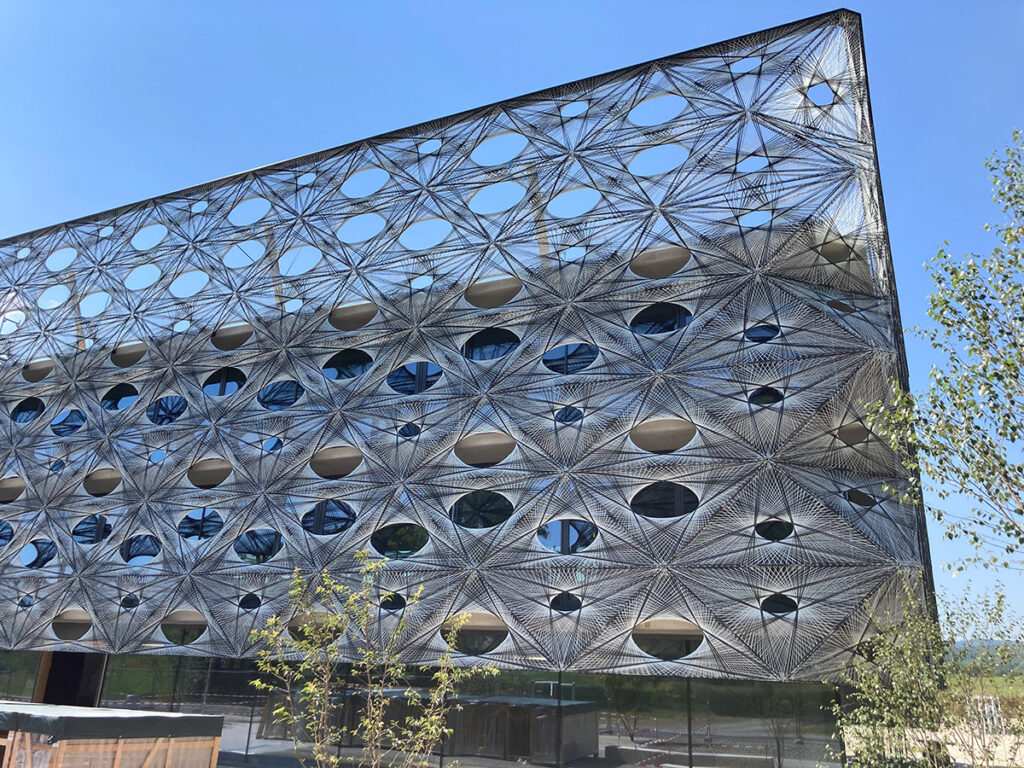
Winding of tubes
Another application concerns the winding of tubes and profiles. For this purpose, a winding machine and an associated laying head were developed and implemented at M+A Dieterle; working length 6.5 m and diameter up to 400 mm. The system is characterised by the fact that the TowPreg is processed as a tape and can thus produce very thin layers. In contrast to classic cross winding, the system can actively cut and reattach the roving. This means that any layer can be produced in any orientation,
closed and without crossing points. As well one can lay down unidirectional layers. The first series production of CFRP pipes using this technology will be implemented inhouse at M&A Dieterle by the end of the year 2023.
Contact:
M&A Dieterle GmbH, Ottenbach
Dipl.-Ing. Benjamin Grisin, Head of Development – Open Fibre Systems
+49 151 64 05 27 48
benjamin.grisin@ma-dieterle.de
www.ma-dieterle.de
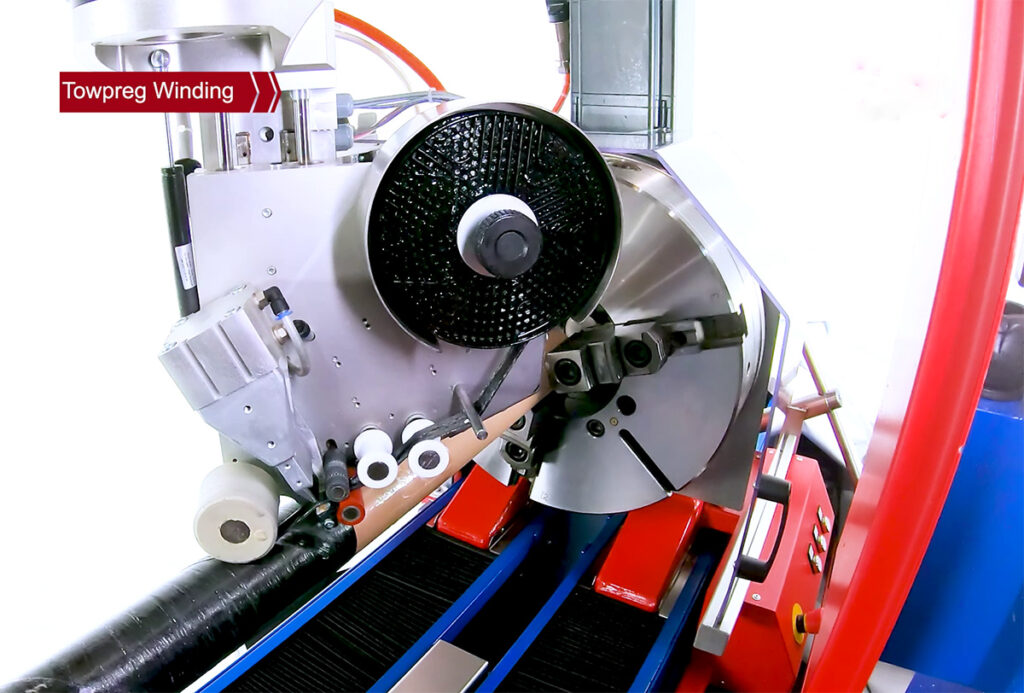