Composites United e.V. (CU) as a network for fiber-based multi-material lightweight design supports and promotes its members in the industrial use of hybrid composites. For the technical exchange within the network, the CU currently has over 40 specialist working groups (WG) and circles on all relevant topics in the composites industry. CU North has now expanded this service and, at the request of its members, has founded two new working groups dealing with the topics of fire protection and pultrusion.
Fire protection with composites
Fire protection is of essential importance for all areas of human life and work, because in the event of an emergency, a fire not only causes considerable damage to property, but also threatens human life. In addition to constructional and technical protective systems, such as extinguishing systems, fire and smoke alarm systems, fire doors or escape and rescue routes, the flammability or fire behavior of materials and building components as well as their fire resistance are essential criteria in the design of, for example, vehicles, aircraft or buildings.
These requirements for materials and components are strictly regulated by a large number of legal regulations. In order to bundle answers to the question: “How can composites meet the existing fire protection requirements?” across industries and to present the current state of the art to interested members, the CU has established the working group “Fire Protection”.
At the digital kick-off event “Fire protection with composites across industries – sustainable solutions and trends” on April 28, 2021, about 70 national and international participants from different industries were attending and discussed current research activities and developments.
For example, Tassilo Witte (CTC GmbH) presented in the opening lecture the possibilities for designing the materials used in an aircraft in accordance with fire protection specifications. Dr. Tina Schlingmann reported on how Deutsche Bahn AG is using 3D printing to manufacture flame-retardant plastic components for the interior of a train compartment. There were several presentations on current developments in maritime applications: Franz Evegren (RISE Research Institute of Sweden), Dr. Lars Molter (Hyconnect GmbH) and Jörg Bünker (Saertex GmbH) spoke about their experiences with the use of composites in an area that is conventionally dominated by steel applications.
The presentations by the industry users were complemented by contributions from materials research and development, such as those by Prof. Markus Milwich and Dr. Mark Steinmann from the German Institutes of Textile and Fiber Research (DITF). Both scientists highlighted the advantages and disadvantages of currently available flame retardants and pointed to a great need for research into the toxicity and ecological impact of these substances.
Head of the new working group Dr.-Ing. Hauke Lengsfeld (General Manager Reactive Polymers and Flame Retardants at Schill + Seilacher “Struktol” GmbH) is pleased about the great interest and the successful kick-off event: “Our aim is to bundle future activities in the field of fire protection with composites across industries and to stimulate the exchange of knowledge and experience among the players. In this way, we can jointly drive forward the development of high-performance composites that meet all relevant safety requirements and thus create a broader field of application for these materials. At the same time, however, the CU members are going one step further – today’s event showed that all companies and institutions are also addressing the issues of sustainability. In their research and development activities, they also focus on reusability, recyclability, and the environmental compatibility and health effects of the materials used.”

The pultrusion market is growing
Pultrusion is a highly efficient, automated process for producing profiles or rods from continuous fiber-reinforced plastics. The market for pultruded applications is growing – the lightweight, corrosion-resistant profiles, which can be produced cost-effectively, are in demand above all from the wind energy, automotive and construction sectors.
This is another topic for which CU members have called for stronger networking and an exchange of knowledge within the framework of a working group. Jens Boelke, Head of Composites & New Technologies at Thomas GmbH + Co. Technik + Innovation KG and head of the new “Pultrusion” working group, explains: “Although pultrusion is now an established process, the networking of the players active in this field is still inadequate. We want to bring together these players along the entire value chain for a pre-competitive exchange of experience on the tools as well as the fibers and resin systems used. This is the only way we can drive innovation around the pultrusion process while ensuring the quality and stability of the process.”
The high level of interest among CU members in joint collaboration was reflected in the registrations for the virtual opening event “CU Pultrusion Innovation Forum” on May 04, 2021: More than 100 international guests from Brazil to Australia had dialed into the online conference.
As an example of a possible collaboration between a resin producer, a fiber manufacturer and a developer of a compact pultrusion system, Lars Friedrich (Olin), Bryan Minges (Owens Corning Composites) and Jens Boelke (pullCUBE) presented a holistic, mobile pultrusion system with coordinated fiber and resin materials (see Fig.).
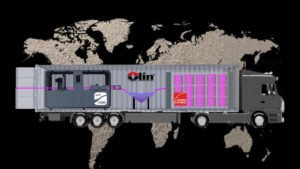