We congratulate all the winners of this year’s AVK Innovation Award and are especially pleased that so many members of our network are among the winners!
The winners of the prestigious Innovation Award for Fibre-Reinforced Plastics of the AVK, the German Federation of Reinforced Plastics, were presented in Salzburg this year. This award always goes to businesses, institutions and their partners for outstanding innovations in composites the three categories Products & Applications, Processes & Methods and Research & Science. Projects are submitted in all three categories and are evaluated by a jury of experts in engineering and science as well as trade journalists, who look at each project in terms of their levels of innovation, implementation and sustainability.
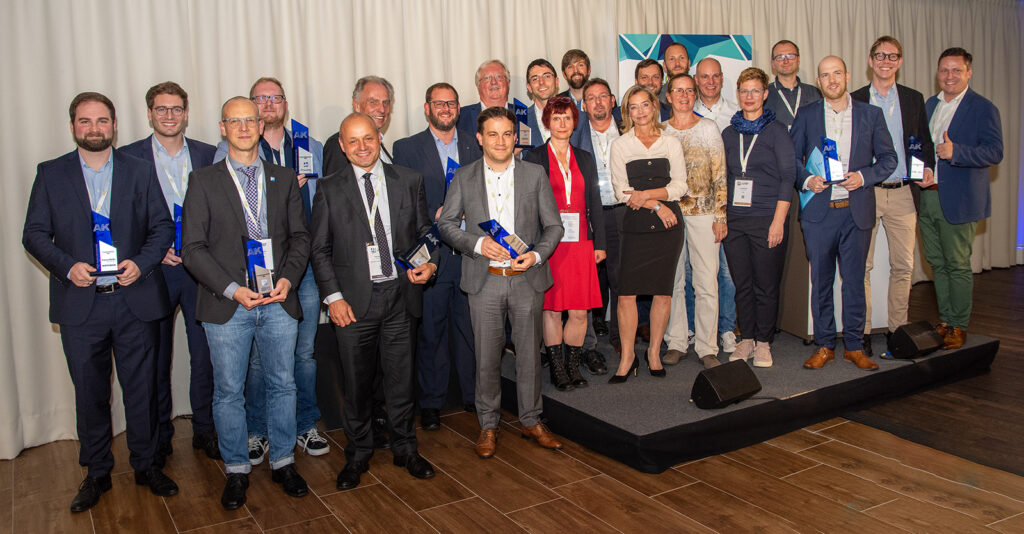
Products & Applications category
First place in innovative Products & Applications went to Leichtbau-Zentrum Sachsen GmbH (LZS) and its partner KWD Kupplungswerk Dresden GmbH for their “Insulating Coupling Shaft For Rail Vehicles”.
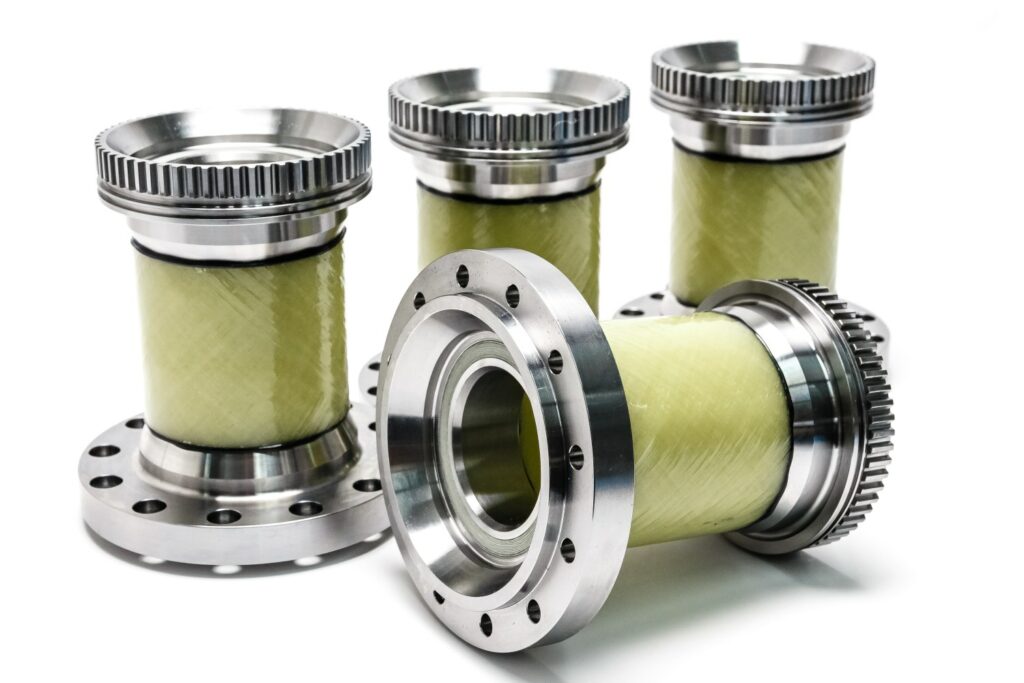
Toothed couplings are classic components in mechanical engineering and may have been invented immediately after the gear wheel. They are resistant to torsion and compensate for any angular misalignment within a small installation space. As this technology is already very mature, one might not expect any general further developments in this segment. Occasionally, however, special requirements arise, such as an application needing electrical insulation between shafts, so that there is indeed still room for innovative development. The two companies therefore developed traditional gear coupling into an electrically insulating intermediate shaft where the functional core element is a tube made of glass-fibre reinforced resin. In this newly developed version, the shaft transfers torques up to 300 Nm at up to 13,000 min-1. At the same time, the high level of material damping that characterises fibre-reinforced plastic also improves the vibration behaviour of the coupling. Special attention was paid, in particular, to the development of the joining principle between the glass fibre tube and the metallic end pieces. This involved using a supported clamp connector which had been specially developed by LZS – a connector that is robust, overload-proof and inexpensive and which can also be attached quickly. The insulating intermediate shaft enables users (e.g. manufacturers of railway and machinery drives) to develop innovative, lightweight and, above all, compact drive units. Since then, the shaft has proved its worth in serial operation and can also be adapted for different specifications.
Second place went to SGL Carbon for its “Electric Car Battery Housing Components Based on Innovative Continuous Fibre-Reinforced Phenolic Resin Composites”.
Lightweight, crash-proof and fire-resistant composites are the materials of choice for battery housings in electric vehicles. They are able to safely contain even thermal runaways, i.e. the uncontrolled overheating of a battery cells. Until recently, such components have usually consisted of glass-fibre reinforced epoxy resin with fire-retardant additives. Now, however, SGL Carbon has for the first time started series production of a component that uses phenolic resins in an innovative process chain, combining them with continuous glass fibres. This solution reduces the wall thickness of the housing components by up to 25% compared with solutions based on an epoxy resin matrix, while also achieving better performance. After all, every gram counts when it comes to optimising the range of an electric vehicle. Also, improved process control saves material during production and therefore valuable resources.
Third place went to Composites Technology Center GmbH (CTC GmbH) and its partners, Faserinstitut Bremen e. V., Sächsisches Textilforschungsinstitut e.V., C.A.R. FiberTec GmbH; partners Japan: CFRI Carbon Fiber Recycle Industry Co., Ltd., IHI Logistics and Machinery Corporation, ICC Kanazawa Institute of Technology for their “High Performance Recycled (HiPeR) Carbon Fibre Materials“.
The aerospace industry is increasingly turning to carbon fibre-reinforced plastics (CRP). These valuable fibres, which are made from production waste or end-of-life components, can be recovered through pyrolysis on a major scale. However, due to their inadequate price-performance ratio, recycled materials of this kind are still not used very widely. A considerable amount of time and money is required to recover such carbon fibres, so that the resulting price is no longer attractive. Compared with continuous virgin carbon fibres, short fibres perform rather poorly, i.e. within a range that lacks attractiveness for high-performance applications.
The aim of this joint German-Japanese project, led by CTC GmbH, was to improve the price-performance ratio of semi-finished recycled carbon fibre products through a high degree of fibre alignment. The manufacturers convincingly demonstrated general feasibility by presenting the extremely promising mechanical characteristics of the material together with a range of full-size mock-up aircraft components.
Procedures & Processes category
First place in Processes & Methods went to KraussMaffei Technologies GmbH and its partner Wirthwein SE for their “Chopped Fibre Direct Process (CFP)”.
This innovative direct fibre-processing method, CFP, will transform the fibre processing into injection-moulding machines. Being efficient and simple, it saves up to 46% in material costs and 0.8 kWh/kg in energy, as it eliminates the need for pre-compounded materials. By using a standard injection moulding machine and a patented screw, CFP significantly reduces production costs. All that needs doing is some adjustments to the material feed and the screw. CFP has reached TRL 8 and has also been successfully tested in automotive injection-moulding applications. The new screw design allows cost-effective retrofitting of existing machinery, replacing expensive continuous-fibre processes. The patented screw geometry also permits direct processing of waste materials from other production processes, such as PA-CF waste from the aerospace industry, without the need to separate fibres and polymers. The new process, CFP, promises quality, efficiency and sustainability.
Second place went to the Fraunhofer Institute for Manufacturing Engineering and Automation and its industrial partners Schindler Handhabetechnik GmbH and Vision & Control GmbH for their “CIRC (Complete In-House Recycling of Thermoplastic Compounds)” process.
Together, they developed an innovative process for the efficient use of offcuts from the processing of thermoplastic organic sheets. Current recycling processes have so far led to the loss of fibre-composite structures and thus also of the high mechanical strength associated with them. The new process captures the geometry and material data of offcuts, combines them efficiently and consolidates them into a new organic sheet via a thermoforming process. Besides a high recycling rate, this also ensures that the relevant mechanical properties are largely retained. The process thus promises a more sustainable and cost-efficient use of organic sheets by minimising waste, while also being scalable to suit different types of applications and materials.
Third place went to CarboScreen GmbH together with the Institute of Textile Technology at RWTH Aachen University for “CarboScreen – Sensor-Based Monitoring of Carbon-Fibre Production”.
Carbon fibres are among the most important lightweight construction materials. They are made through the thermal conversion of a PAN fibre. The manufacturing process is highly complex and sophisticated. At present, it is only monitored visually in the industry, by semi-skilled staff. However, inadequate process control can lead to fibre damage and, in extreme cases, to production line fires that are often not detected early enough. To ensure satisfactory product quality, the maximum production speed is limited to 15 metres per minute, which considerably reduces the production capacity of a plant. To improve and accelerate the manufacturing process, CarboScreen GmbH, a company founded under an EXIST grant, now offers a sensor-based monitoring system for carbon fibre production. The underlying technology allows the continuous monitoring of fibres during production and automatically identifies any deviations.
Research & Science category
First place in Research & Science went to Faserinstitut Bremen e. V. for its “Development of a Stereocomplex PLA Blend on a Pilot Plant Scale”.
Working on a pilot plant scale and using an innovative type of process control, the AIF research project PLA2 was the first to produce a blend that is based on the biopolymer called polylactide (PLA) and which has a stereocomplex crystalline structure and a melting temperature of 235°C. Scale-up to industrial dimensions allows for sample material availability, thus creating the potential to develop self-reinforced PLA fibre composites, which will significantly expand the range of applications. This will make it possible to replace conventional plastics such as polypropylene (PP) and thus to save resources and protect the environment.
Second place went to the Chair of Carbon Composites at the Technical University of Munich and its partners Apppex GmbH and Haas Metallguss GmbH for their “Fibre-Reinforced Salt as a Robust Lost Core Material”.
The innovation is a new lost core material and a range of manufacturing process designed to produce it. Lost cores give the designer a completely new scope for creativity that would be impossible to achieve with conventional tools. Depending on the component geometry and process conditions, the material has to meet stringent requirements. While it needs to be robust enough to survive the filling process, it must also highly soluble. The combination of materials is based on the principle of fibre-reinforced ceramics. A water-soluble salt (e.g. NaCl) is combined with either short or continuous fibre reinforcement, transforming the originally brittle fracture behaviour into a pseudo-ductile one. Fibre-reinforced salt is a lost core material that has high levels of mechanical strength and impermeability and which can be dissolved in water and recycled. It is suitable for materials that make major thermomechanical demands on a water-soluble core material, e.g. under injection moulding, RTM and light-metal die casting.
Third place went to Sächsisches Textilforschungsinstitut e.V. (STFI) and its partner Fraunhofer Institute for Chemical Technology (ICT) for “VliesSMC – recycled Carbon Fibres with a Second Life in the SMC Process”.
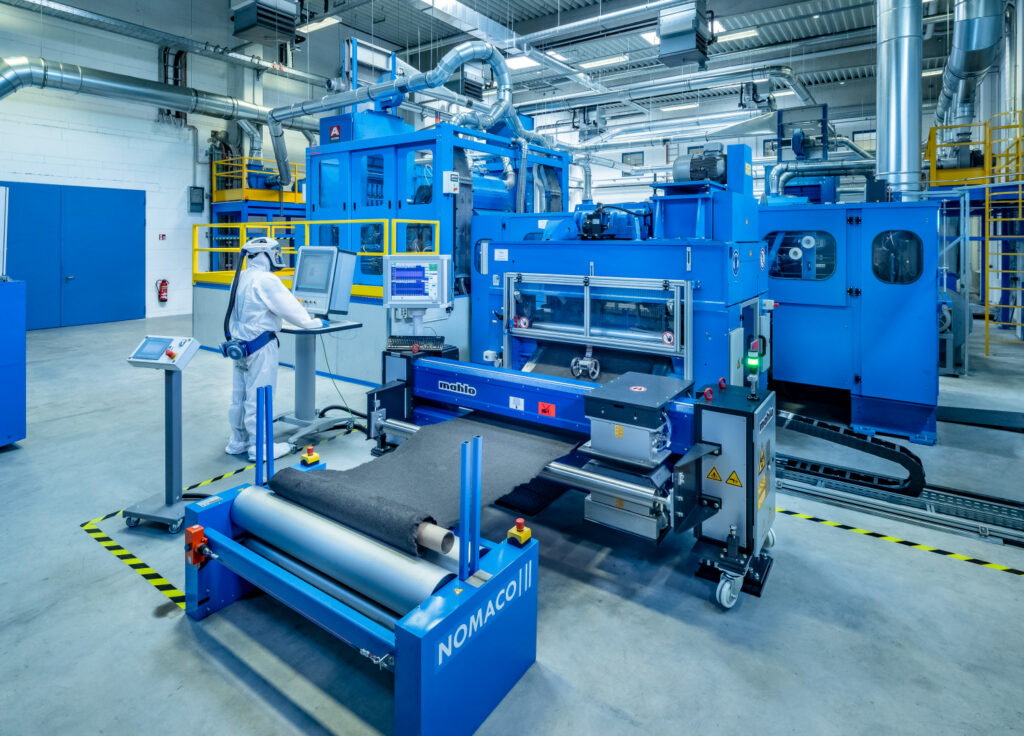
Third place in the “Research and Science” category went to the STFI – Sächsisches Textilforschungsinstitut e. V. (Saxon Textile Research Institute) and its partner, the Fraunhofer Institute for Chemical Technology (ICT), with “VliesSMC – Recycled Carbon Fibers with a Second Life in the SMC Process”.
The researchers succeeded in integrating recycled carbon fibres in the form of nonwovens or unbonded nonwoven layers into an SMC and then processing this product not through compression moulding, as is normally the case, but through extrusion. © STFI
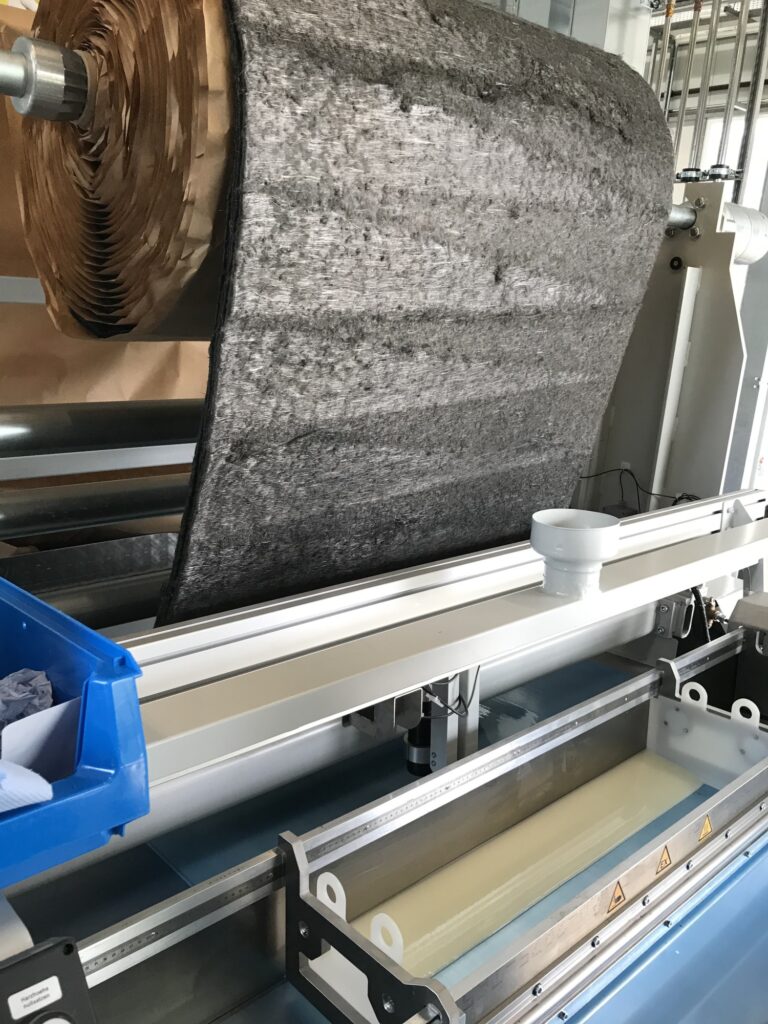
The researchers succeeded in integrating recycled carbon fibres in the form of nonwovens or unbonded nonwoven layers into an SMC and then processing this product not through compression moulding, as is normally the case, but through extrusion. Thus, nonwoven-based SMC can be used for the production of complex components with high levels of deformation and reinforcing elements (e.g. ribs). Together with a project committee of 25 industry representatives, the research partners demonstrated that these SMC have two benefits: first, they can be manufactured more cost-effectively than commercially available products made from primary materials, and secondly, their performance is as good as or even better than that of others. Moreover, the results were not obtained on a laboratory scale, but have already been validated on a pilot plant scale, so that a big step has been taken towards feasibility.
List of award winners in the three categories:
Products & Applications category | |
---|---|
First place: “Insulating Coupling Shaft for Rail Vehicles” – Leichtbauzentrum Sachsen GmbH, partner: KWD Kupplungswerk Dresden GmbH | |
Second place: “Electric Car Battery Housing Components Based on Innovative Continuous Fibre-Reinforced Phenolic Resin Composites” – SGL Carbon | |
Third place: “High Performance Recycled Carbon Fibre Materials (HiPeR)” – Composites Technology Center GmbH (CTC GmbH), partners: Faserinstitut Bremen e. V, Sächsisches Textilforschungsinstitut e.V., C.A.R. FiberTec GmbH; partners Japan: Faserinstitut Bremen e.V., Sächsisches Textilforschungsinstitut e.V., C.A.R. FiberTec GmbH; Partner Japan: CFRI Carbon Fiber Recycle Industry Co., Ltd., IHI Logistics and Machinery Corporation, ICC Kanazawa Institute of Technology | |
Innovative Processes & Methods category | |
First place: “Chopped Fibre Direct Processing (CFP)” – KraussMaffei Technologies GmbH, partner: Wirthwein SE | |
Second place: “CIRC - Complete Inhouse Recycling of Thermoplastic Compounds” – Fraunhofer Institute for Production Engineering and Automation (IPA), partners: Schindler Handhabetechnik GmbH, Vision & Control GmbH | |
Third place: “CarboScreen – Sensor-Based Monitoring of Carbon-Fibre Production” – CarboScreen GmbH, partner: Institute of Textile Technology at RWTH Aachen University | |
Research & Science category | |
First place: “Development of a Stereocomplex PLA Blend on a Pilot Plant Scale” – Faserinstitut Bremen e. V. | |
Second place: “Fibre-Reinforced Salt as a Robust Lost Core Material” – Technical University of Munich, Chair of Carbon Composites, partners: Apppex GmbH, Haas Metallguss GmbH | |
Third place: “VliesSMC – Recycled Carbon Fibres with a Second Life in the SMC Process” – Sächsisches Textilforschungsinstitut e.V. (STFI), partner: Fraunhofer Institute for Chemical Technology (ICT) |
The award ceremony was held in Salzburg, at the JEC Forum of Germany, Austria and Switzerland – the third of its kind in the three German-speaking countries. “Whether it’s innovative products, cutting-edge processes or indeed research, the opportunities offered by composites are highly promising, offering plenty of scope for the future. As before, the AVK Innovation Award is demonstrating this very clearly. Special congratulations are therefore due to everyone who has been actively involved in production, development and research for their outstanding work. By presenting the innovations in this way, we have taken a further step towards showcasing the potential of composites and their many benefits. Again, it was a pleasure for the jury to play its part,” summed up chairman of the jury Gerhard Lettl, from C.F. Maier GmbH, at the award ceremony.
Entries for the next Innovation Award 2024 can be submitted from January 2024 onwards.
Contact:
AVK – Industrievereinigung Verstärkte Kunststoffe e. V.
Birgit Förster
Tel. +49 69 271077-13
birgit.foerster@avk-tv.de