We congratulate all the winners of this year’s AVK Innovation Award and are really pleased that so many members of our network are among the winners!
The winners of the prestigious Innovation Award for Fiber Reinforced Plastics from the AVK Industrievereinigung Verstärkte Kunststoffe were presented in Stuttgart this year. The award goes to companies, institutes and their partners in each of the three categories “Products and Applications”, “Processes and Procedures” and “Research and Science” for outstanding composites innovations. An expert jury of engineers, scientists and trade journalists evaluates the submissions in the three categories based on criteria such as level of innovation, degree of realization and sustainability.
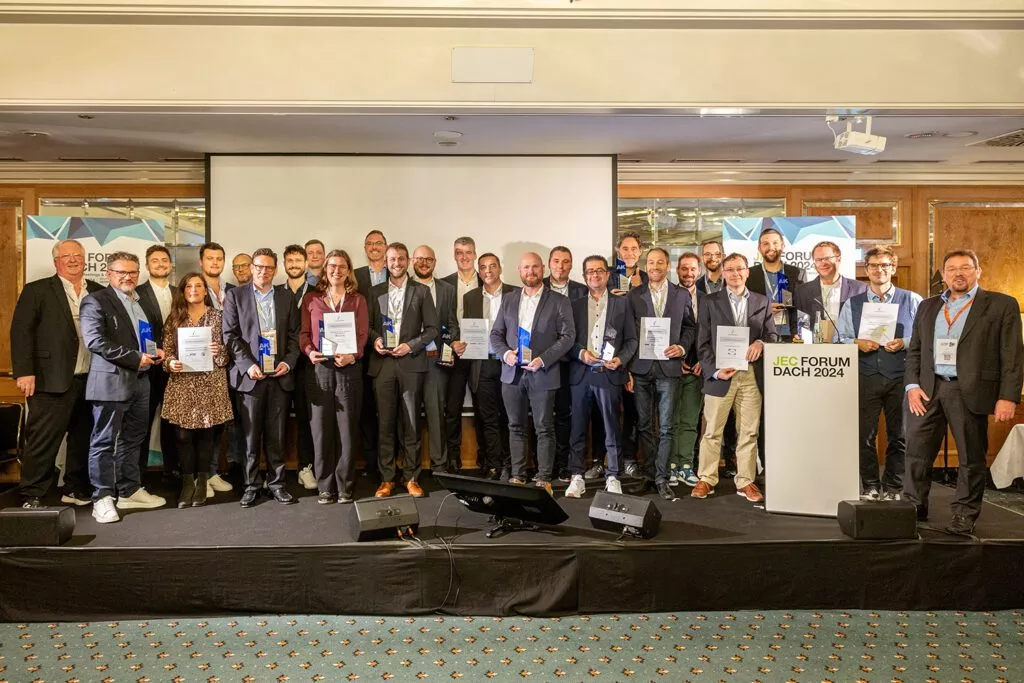
Category “Innovative products and applications”
First place in the “Innovative products and applications” category went to thoenes® Dichtungstechnik GmbH, RAUCH Landmaschinenfabrik GmbH and the Institute for Lightweight Construction and Plastics Technology at TU Dresden with their innovation “Sustainable fertilizer spreader frame: lightweight construction with thermoplastic carbon-PA6 hollow profiles”.

As part of the Le²Gro project, an innovative lightweight fertilizer spreader frame with a span of more than 36 meters was developed. The construction consists of thermoplastic, continuous fiber-reinforced hollow profiles, which are manufactured using an advanced tube blowing process. This design reduces the weight of the frame by 43% from 2000 kg to 1140 kg, which reduces both fuel consumption and the ground pressure load and increases the payload capacity. In addition, the improved manufacturing technology enables greater efficiency in production and allows the integration of functions such as material conveying directly through the boom in the end section.
The frame is connected by innovative metallic node structures which, in combination with thermoplastic load introduction elements, create a rigid and durable truss structure. The overall prototype was tested in 2024 and the aim is to launch it on the market in the coming years. The technology not only offers potential for agricultural engineering, but also for other industries such as tent construction or special machine construction.
The focus is also on sustainability: in addition to reducing CO₂ emissions through lower fuel consumption, the material is more impact-resistant, easier to repair and recyclable, which further increases the service life and environmental friendliness of the product.
Funded by the Federal Ministry for Economic Affairs and Climate Protection on the basis of a decision by the German Bundestag as part of the TTP LB.
The “GREEN GUARD bicycle box – modular, versatile and sustainable for the mobility of tomorrow” from Mitras-Composites Systems GmbH and project partner Leichtbau-Zentrum Sachsen GmbH took second place.
A unique bike box due to its properties:
- Modularity – convertibility (modular extension or dismantling) enables lifelong use
- Sustainability – lower CO₂ balance than comparable metal products
- Durability – robust and weatherproof fiber composite material without maintenance and care requirements
- Attractive design – natural shape and color scheme creates a suitable fit in urban rural cityscapes
The following two videos provide further insights:
Image film bicycle box GREENGUARD: https://www.youtube.com/watch?v=UwJRTIKM0Jc
Product film bicycle box GREENGUARD: https://www.youtube.com/watch?v=ly2lpZm1nKU
3rd place went to SPIN Siebert&Schörner GbR, together with the project partners University of Applied Sciences Northwestern Switzerland (FHNW), V-Carbon, CG TEC and Schmolke Carbon and the submission “Recycled carbon fibers (rCF) for load-bearing components – high-end racing bike frames for a genuine circular economy”.
As part of the German-Swiss project “RecyWind – Recyled carbon fibers in structural applications” funded by Innosuisse-Innobooster “Plastics for Zero Emission”, the partners FHNW University of Applied Sciences and Arts Northwestern Switzerland (CH), V-Carbon (CH), SPIN (D), CG-TEC (D) and Schmolke-Carbon (D) developed and manufactured the world’s first high-end racing bike frame made from recycled carbon fibers.
The aim of the project was to investigate the suitability and performance of recycled and oriented carbon fibers (rCF) with regard to structural applications.
As an example of a dynamically highly stressed structure, a racing bike frame was selected as a demonstrator. The suitability of recycled carbon fibers was impressively confirmed, the frame produced has comparable mechanical properties and, with a total mass of only 1050g, has a low and absolutely tolerable additional weight compared to new fiber frames.
The developed racing bike frame can be certified as having race-ready properties and the total weight just under the limit (6.8 kg) of the UCI cycling world federation underlines the quality of the project result. Sustainability and performance therefore do not have to be a contradiction in terms.
Basically, however, it is not just about bicycle frames, but about the use of recycled carbon fibers (rCF) for structurally stressed components and structures for a wide variety of applications in different branches of industry.
The component “high-end racing bike frame” was only selected as a demonstrator to demonstrate the applicability of “2nd life material” as a real primary structure in a tangible way.
Category “Innovative processes/procedures”
The company REHAU Industries SE + Co KG together with the project partners ANYBRID GmbH and CQFD Composites came first in the category “Innovative processes and procedures” with their submission “Processing method of thermoplastic composites in a process chain for the production of components”.
The process chain, consisting of the production of thermoplastic pultruded and co-extruded profiles in combination with automated frame production using assembly injection molding, offers groundbreaking potential for various applications.
At this year’s international window construction trade fair FENSTERBAU FRONTALE 24, the first functional prototype of a window element manufactured using this process was exhibited. The thermoplastic pultrudate with up to 85 percent glass fiber reinforcement by weight enables outstanding properties in key aspects and without any steel reinforcements. For windows in particular, dispensing with steel brings considerable advantages in terms of logistics, production and thermal insulation. Due to the thermoplastic nature of the profile, there are further advantages, both in terms of sustainability and for functional integration options. For example, offcuts left over from the mitre cuts required in window construction can be regranulated and reused for window applications. The recycled material is processed into corner connectors by injection molding, which are inserted into the profiles before automated assembly. However, the production of short glass fiber reinforced extruded profiles is also possible. The window frames are assembled in a highly automated process using mobile injection molding, in which the corners are joined simultaneously by up to four robots, depending on the required productivity.
Each process step has been developed and extensively tested over many years in collaboration with various partners to ensure maximum reproducibility with maximum material utilization. This innovation represents a significant advance in the production of composite profiles and has the potential to redefine the standards of the industry, not only in the window sector.
“Patented process optimization of UV channel rehabilitation thanks to sensor-supported and data-driven real-time monitoring in the liner” is the title of the 2nd place innovation, submitted by NETZSCH Process Intelligence GmbH, in collaboration with the project partners Rausch Rehab GmbH, ProKASRO Mechatronik GmbH and RelineEurope GmbH.
The NO-DIG movement is widespread, and trenchless sewer rehabilitation is the means to success. The promising new method renews damaged sewer pipes with the aim of restoring tightness and stability. For this purpose, a plastic layer, the so-called liner, is installed as a new pipe wall. The call for on-site testing is getting louder and louder. Climatic influences from location to location, different material behavior due to a diverse landscape of liner manufacturers and other dominant factors, such as sewer wetness, influence the curing behavior of plastics. NETZSCH Process Intelligence GmbH and its partners have patented a process that monitors the curing progress along the entire sewer rehabilitation channel and transmits the information to an evaluation unit in real time. The technology also enables the active and dynamic control of the core feed speed based on the curing progress of the material in order to utilize the highest possible feed speed and avoid overheating the liner. At the same time, the data of the cured liner measured in the channel enables correlation with quality assurance data such as the degree of curing, the modulus of elasticity and the residual styrene content. The sensor and evaluation unit of the solution, called sensXPERT Pipe, is mounted directly on the UV cores, while the data is transferred to the “third man”. The expansion of the “third man” as a system component that actively controls the core significantly reduces sudden jumps and makes the system accessible for retrofits and new UV irradiation systems from ProKASRO and its competitors.
Fibron Pipe GmbH and its project partners Ceyeborg GmbH and Kloos Systems GmbH took 3rd place with the “Development and use of an AI-based ATP system for the production of TCP”.
The use of delivery lines in the energy industry is a critical application. Against this background, the use of inline quality assurance systems is increasingly demanded and expected, in addition to the existing product-related quality standards that have been in place for years. Intelligent inline quality assurance is therefore essential for the production of composite pipes. Our existing QA systems have been supplemented by the use of a completely new inline quality control system, the ATP (Automatic Tape Placement). Failure of a composite pipe can be attributed to the use of inadequate materials and/or sub-optimal machine/process settings during the pipe manufacturing process. In the case of using UD fiber tapes as a pressure-resistant reinforcement material, the primary concern is the precise positioning of the tapes and the control of the tape tension at all times during production. In addition to classic computer vision techniques, FibronPipe® relies on state-of-the-art AI models. These models were trained in a months-long process with a mixture of synthetic and on-site data to understand exactly what the different regions in a camera image mean and how the control system has to deal with them. For example, if a gap dimension between the fiber tape layers is measured that deviates from the target value by more than 0.2 mm, the system reacts automatically and controls the axial adjustment of the drive motor, which regulates the respective fiber tape spool position. Of course, the system also serves to ensure the basic quality of the fiber tape itself at all times – in other words, the surface of the fiber tape is constantly checked visually. The entire system then communicates fully and independently with the higher-level system control of the entire production process.
Category “Research and Science”
The Fraunhofer Institute for Chemical Technology (ICT) took first place in this category with the “Processing of recyclable mono-material sandwich structures in large-scale production processes”.
Conventional FRPs demonstrate their advantageous mechanical properties in lightweight construction primarily during the use phase, but reuse in the same application is only possible to a limited extent or not at all due to the structure-related fiber shortening or the matrix material used. The award-winning research approach addresses this problem and paves the way for recycling in the same application. To this end, the multi-material design approach widely used in lightweight construction was rethought and adapted into a multi-morphology approach using just one material. This involved optimizing commercially available, self-reinforced materials and foams and developing new joining, forming and functionalization processes suitable for large-scale production. A deep understanding of the mechanisms of action in the material, such as crystallization kinetics, cell morphology and melt viscosity, forms the basis of this approach. The developed process chain from semi-finished product to complex components was then validated using an automotive seat structure. Self-reinforced organic sheets have been on the market for several years, but have limited areas of application due to stiffness deficits. The adhesive-free combination with thermoplastic foams, which are based on an identical base polymer, allows weight-specific bending stiffnesses to be achieved as with conventional FRPs. Temperature control along the process chain is crucial in order to avoid relaxation of the reinforcing fibers and thus maintain mechanical performance. The components produced using the multi-morphology approach consist of just one thermoplastic material – this enables complete recycling. The approach was implemented for recyclate-based PET and bio-based PLA, so that the need for new production of petro-based plastics can be reduced. The development was transferred from the technical center to industry through close cooperation with partners along the value chain, with potential applications in the sports and leisure sectors as well as semi-structural components in the mobility industry. In addition to the reuse of existing materials, the maximum lightweight construction made possible by the innovation also contributes to climate protection by reducing greenhouse gases in the mobility industry and avoiding further plastic waste.
Second place went to the Faserinstitut Bremen e.V. with the “Development of fine-denier PEEK yarns with product-specific mechanical and thermomechanical behavior”.
The Faserinstitut Bremen has succeeded in developing fine-denier yarns made from the high-performance thermoplastic PEEK with product-specific mechanical and thermomechanical behavior. Blends of various PEEK materials with different molecular weights were developed by means of compounding. These blends were further processed by melt spinning into yarns with gauges of 50 dtex (50f18 or 50f36) and technical strengths of more than 70 cN/tex. The yarns developed were successfully processed into twisted yarns on an industrial scale and used in the textile processes of embroidery, warp knitting and sewing. With the fine-denier PEEK yarns developed, a foundation stone has been laid for the optimal utilization of high-performance fiber composite structures – above all CFRP. Damage and defects in the subsequent fibre composite component can be minimized and resources conserved through the use of fine-denier yarns.
The Institute of Textile Machinery and Textiles at TU Dresden came third with its submission “Final contour-compatible multiaxial fabrics with variably adjustable reinforcement thread density”.
As part of two research projects, a unique retrofit module for multiaxial warp knitting machines was developed that significantly increases the material and cost efficiency and sustainability of fiber-reinforced plastic composite (FRP) production. For the first time, this technology enables the production of fabrics with locally adapted reinforcing warp yarn densities and weft yarn lengths, resulting in material cost savings of up to 35% – especially when using cost-intensive high-performance fibers such as carbon fibers.
The innovation allows precise control of the thread placement so that warp threads can be specifically removed or reintegrated where they are needed. This enables near-net-shape production; waste is minimized by up to 90 %.
The new modules have been specially developed so that they can be easily integrated into existing production environments. This makes them particularly attractive for small and medium-sized enterprises (SMEs). Experimental tests have confirmed the reliability and potential of this technology, which not only contributes to cost savings but also to a significant reduction in the CO₂- footprint of FRP production, particularly CFRP.
Overview of all award winners in the three categories:
Category „Innovative products and applications“ | |
---|---|
1st place: “Sustainable fertilizer spreader frame: lightweight construction with thermoplastic carbon-PA6 hollow profiles” - thoenes® Dichtungstechnik GmbH, RAUCH Landmaschinenfabrik GmbH, Institute for Lightweight Construction and Plastics Technology (TU Dresden) | |
2nd place: “GREEN GUARD bicycle box - modular, versatile and sustainable for the mobility of tomorrow” - Mitras-Composites Systems GmbH, partner: Leichtbau-Zentrum Sachsen GmbH | |
3rd place: “Recycled carbon fibers (rCF) for load-bearing components - high-end racing bike frames for a true circular economy” - SPIN Siebert&Schörner GbR, partners: University of Applied Sciences Northwestern Switzerland (FHNW), V-Carbon, CG TEC, Schmolke Carbon | |
Category “Innovative processes/procedures” | |
1st place: “Processing method of thermoplastic composites in a process chain for the production of components” - REHAU Industries SE + Co KG, partner: ANYBRID GmbH, CQFD Composites | |
2nd place: “Patented process optimization of UV channel rehabilitation thanks to sensor-supported and data-driven real-time monitoring in the liner” - NETZSCH Process Intelligence GmbH, partners: Rausch Rehab GmbH, ProKASRO Mechatronik GmbH, RelineEurope GmbH | |
3rd place: “Development and use of an AI-based ATP system for the production of TCP” - Fibron Pipe GmbH, partners: Ceyeborg GmbH, Kloos Systems GmbH | |
Category “Research and Science” | |
1st place: “Processing of recyclable monomaterial sandwich structures in large-scale production processes” - Fraunhofer Institute for Chemical Technology (ICT) | |
2nd place: “Development of fine-denier PEEK yarns with product-specific mechanical and thermomechanical behavior” - Faserinstitut Bremen e. V. | |
3rd place: “Final contour-compliant multiaxial fabrics with variably adjustable reinforcement yarn density” - Institute for Textile Machinery and Textiles (TU Dresden) |
The award ceremony took place on October 22, 2024 during the JEC Forum DACH in Stuttgart.
Contact:
AVK – Industrievereinigung Verstärkte Kunststoffe e. V.
Katharina Wagner
Tel. +49 69 271077-13
Katharina.wagner@avk-tv.de