Hybridly reaching the finish line: Multidisciplinary project team develops innovative resource-saving solutions
Currently, the industrial use of lightweight solutions still often fails due to high material and manufacturing costs. There are also open questions regarding the ecological aspects of recycling and the reuse of high-performance fibres. In this area of conflict, in the VliesComp joint project expert teams from science and industry developed innovative approaches.

VliesComp project consortium with final demonstrators
The aim of the three industrial partners Tenowo GmbH (Hof), Siemens AG (Erlangen) and Invent GmbH (Braunschweig) involved in this VliesComp project is to bring recycled materials back into the market in various lightweight applications. They received scientific support for this project from the Sächsisches Textilforschungsinstitut e. V. (Chemnitz), STFI.
However, the focus of VliesComp was not the search for the highest mechanical structural potential. Instead, the project rather put the focus on the achievement of ecological and cost-efficient, multifunctional added value through the use of recycled materials for selected industrial uses.
Key content areas
In the course of the project work, four key areas were prioritised:
- Definition of requirements for materials, processes and components
- Technology development in the field of material and process technology for hybrid nonwovens
- Technology development in the area of digital value creation and ecology of hybrid nonwovens
- Demonstration of technology usability through component realisation and -evaluation
As examples, the experts looked at the application areas of e-machines for the energy transition, e-mobility and aviation. In the course of developing damping elements for e-machines and housing covers for e-motors, the partners utilised hybrid nonwovens with a blend of thermoplastic fibre components and recycled high-performance fibres, as well as nonwovens based on 100 % recycled high-performance fibres.
Results achieved
After several optimisation loops, the experts succeeded in developing damping
elements for e-machines based on hybrid nonwovens with improved damping properties and comparable stiffness to the reference. By using these new, better damping support elements, any vibrations that occur can be reduced much more quickly, which leads to a reduction in the load on the conductor rails and therefore extends the service life of the insulation system.
For the prototype production of housing covers, the first step was to develop a mould for producing the component based on rCF nonwovens on the basis of a structural analysis. Through several optimisation loops in the process control, it was finally possible to manufacture components with a recycled fibre content of 100%. Compared to the variant made from primary carbon fibres in the RTM process, a 14% reduction in CO2 equivalent is possible with the same performance. The calculation for using the prepreg process with a bio-resin system even shows a potential for reducing the CO2 equivalent by almost 70 %.
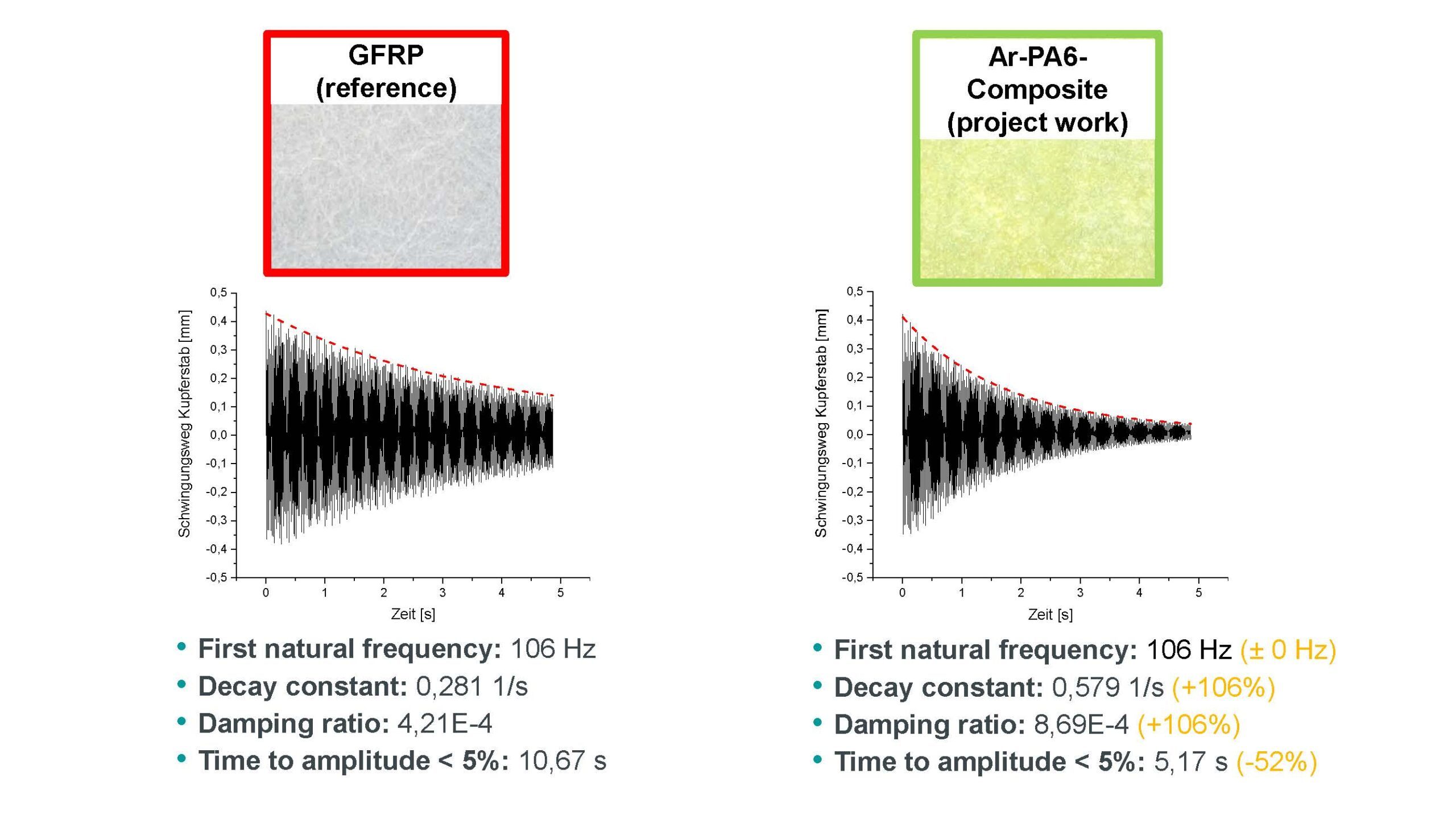
Contact:
Sächsisches Textilforschungsinstitut e. V. (STFI), Chemnitz
Dipl.-Ing. (BA) Marcel Hofmann
Leiter Transfer
+49 371 52 74 205
The VliesComp project was funded by the Federal Ministry for Economic Affairs and Climate Action as part of the „Lightweight Construction Technology Transfer Programme (TTP Leichtbau)“ on the basis of a decision by the German Bundestag.