The latest results with the diversification of the central technology platform of single-stage direct processing were presented at the thermoPre® symposium in Chemnitz. This also includes the effiLOAD technology for the continuous production of near-net-shape, load-path-compliant and waste-reduced preforms for high-performance components.
The project partners of the thermoPre® growth core developed a new technology platform of single-stage direct processing for the production of continuous fiber-reinforced, thermoplastic semi-finished products. This high-volume technology was expanded in the follow-up project thermoPre® plus to include the processing of high-performance and high-temperature polymers. The new plant can now produce continuous fiber-reinforced tapes up to 600 mm wide with different reinforcing fibers and the matrices PA6, PA6.6, PPS and PET.
New goals, new approaches
The mechanical, economic and ecological demands placed on modern lightweight structures are often disparate and increasingly require the targeted combination of novel materials, intelligent construction methods and efficient manufacturing technologies. This is taken into account by the newly developed effiLOAD technology for the continuous production of near-net-shape, load-path-compliant and waste-reduced preforms for high-performance components.
In this process, fully consolidated, continuous fiber-reinforced thermoplastic UD tapes of defined width are deposited in layers on top of one another close to the final contour and load path on a continuously moving carrier material and thermally fixed. In addition to the flat, near-net-shape semi-finished structure, continuous reinforcing fibers are laid as hybrid rovings in a continuous process to match the load path.
Depending on the number of multi-tape laying heads, even larger component dimensions can be produced in a single operation. These preforms are cut out of the carrier web and stacked by a handling system to form a component-specific preform stack of effiLOAD blanks.
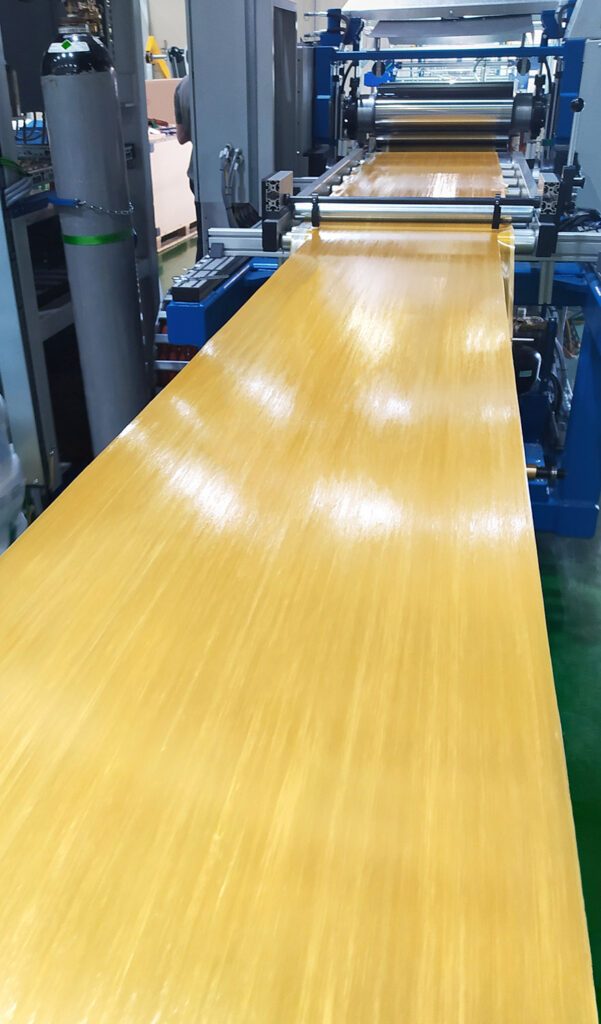
Fit for more lightweight design
The new technology is characterized by significantly improved resource efficiency and energy savings, particularly for cost-intensive carbon fiber applications. Depending on the component, the amount of waste and thus the use of carbon fibers can be reduced by up to 70% while maintaining the same performance.
The energy-intensive carbon fibers used in production are only used partially along the load paths. The effiLOAD process thus contributes to the conversion to low-CO2 and climate-neutral production technologies in the long term. In addition, the significantly increased cost-effectiveness, resource efficiency and productivity opens up new fields of application for continuous fiber-reinforced thermoplastic fiber composite materials. The novel effiLOAD process is thus carrying intelligent and climate-friendly lightweight design solutions into widespread industrial application.
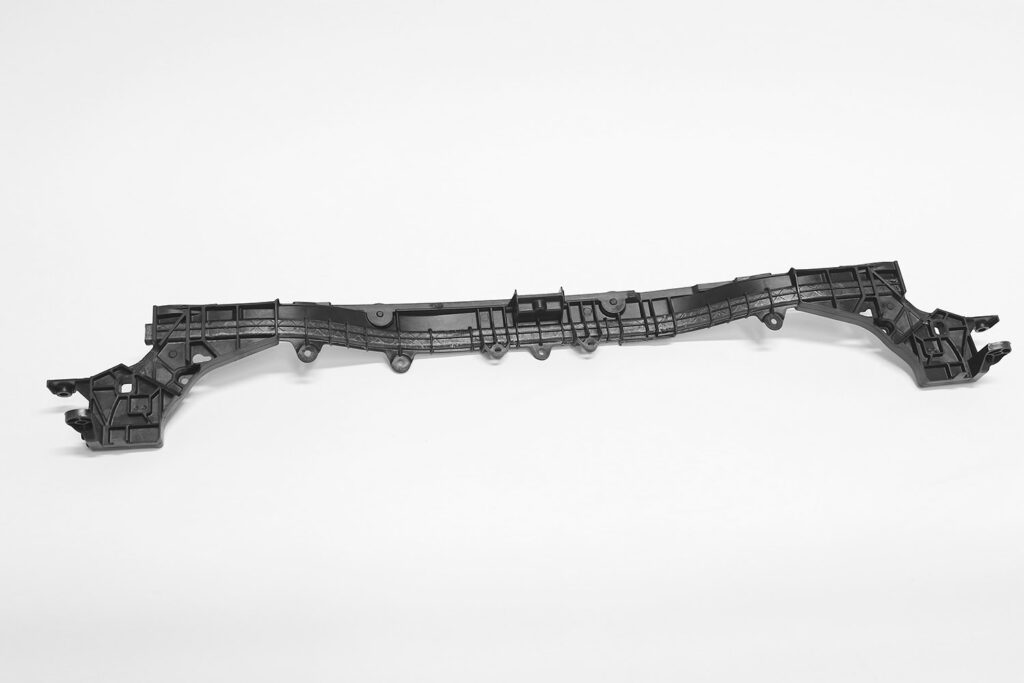
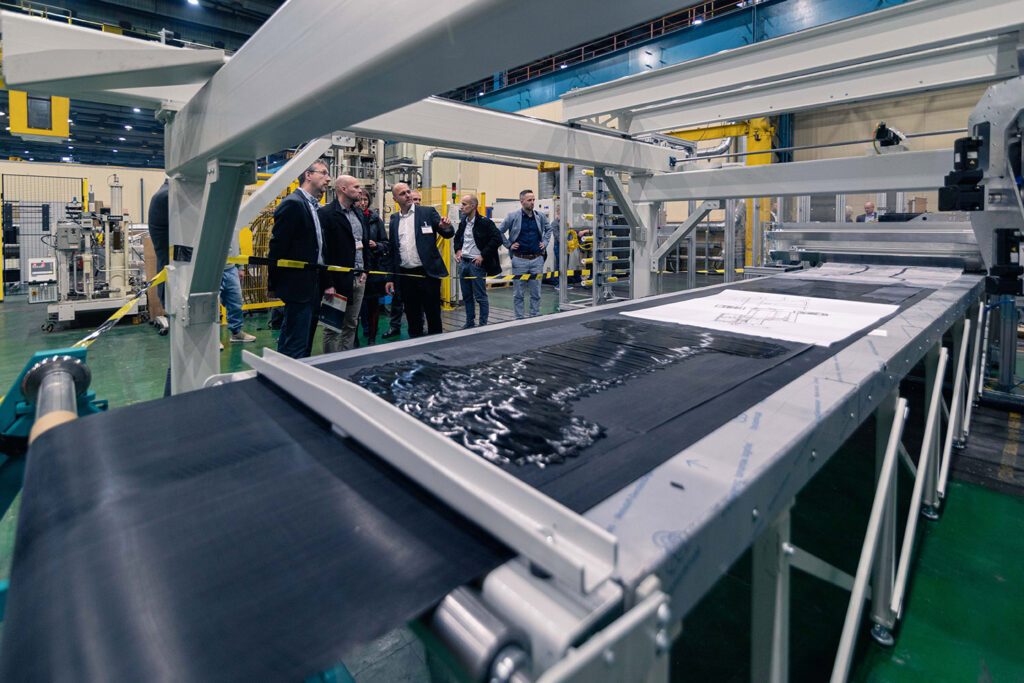
Like the regional growth core thermoPre®, its follow-up project thermoPre® plus was also funded by the German Federal Ministry of Education and Research (BMBF), Innovation Initiative Neue Länder „Unternehmen Region“. The aim was to explore new approaches to the more resource- and cost-efficient production of functionally integrated thermoplastic high-performance components with continuous fiber reinforcement and to take them to a level 4 technology maturity level (TRL). In seven collaborative projects, 24 companies, three research institutes and three associated partners developed, among other things, new modules and equipment as well as the effiLOAD technology.
With effiLOAD technology, a completely new process has been developed that occupies a central position within the entire growth core and is protected by patent No. EP3 257 663 B1.
Contact:
TU Chemnitz
Prof. Dr.-Ing. Wolfgang Nendel
Stv. Leiter Strukturleichtbau und Kunststoffverarbeitung | Ansprechpartner Bündnis Wachstumskern thermoPre plus
+49 371 531-325 45
www.thermopre.de
thermoPre ENGINEERING GmbH, Chemnitz
Sebastian Iwan, Geschäftsführer
+49 176 20 74 23 28
sebastian.iwan@thermopre-gmbh.de
www.thermopre-gmbh.de
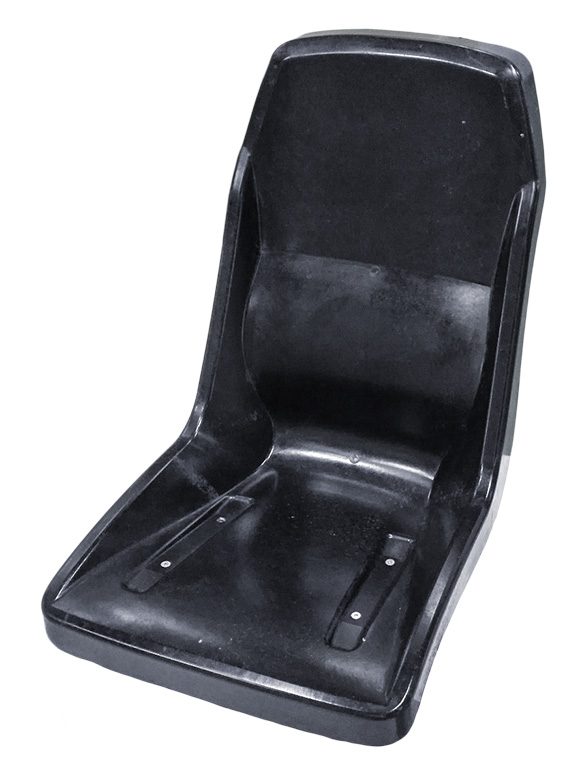