As part of the “UniFix” joint project funded by the German Federal Ministry for Economic Affairs and Climate Action (BMWK), experts in Automation and Production Technology at the Fraunhofer Institute for Manufacturing Technology and Advanced Materials IFAM in Stade, together with cooperation partners and Airbus Operations GmbH (Stade) as an associated project partner, have developed a unique mobile holding fixture. This fixture is able to flexibly accommodate various large components, such as aircraft tail planes and landing flaps, in a wide variety of types up to eight meters in length, and to align and transport them accurately and sustainably in terms of shape. (Video: https://s.fhg.de/SS6)
Focused on machining processes in the production sequence, this holding fixture is able to considerably relieve a machining system of time-consuming, non-value-adding secondary activities by passing through various process stations in advance with the optimally and precisely aligned large components, at which preparatory work can be carried out in parallel and simultaneously.
A milestone, because in the increasingly automated production, machining, and assembly of large components made of weight-saving carbon fiber-reinforced plastics (CFRP), the transition from manually pulsed production to flow-line production is currently imminent in aircraft production. As in other industries, e.g. automotive manufacturing, this flow-oriented production makes it possible to reduce throughput times and thus increase productivity, efficiency and cost-effectiveness, and consequently competitiveness in the international market. The advantages of flow-oriented manufacturing lie primarily in the reduction of manual handling operations and non-productive time. In addition, there are efficiency gains through specialization of the individual plants, reduced throughput times due to harmonized cycle times, as well as an associated decrease in buffer stocks and faster reaction to process deviations.
Challenges in the manufacturing of large CFRP structures
Both the vertical tail plane and the landing flaps of an aircraft are assembled from large flat shell elements stiffened by ribs. Before joining the shell elements, it is necessary to bring them to the required exact final contour by automated milling. Today, this machining process represents a bottleneck in production. It is also extremely prone to risk, as errors at a high stage of the value chain can lead to considerable costs due to rejects or correction of the component.
Flow-Line-Production
“In order to significantly accelerate the process – while simultaneously minimizing risk – we decided in the “UniFix” project to implement mechanical machining in the manufacture of the vertical tail planes or landing flaps of a passenger aircraft as flow-line production”, explains project manager Christoph Brillinger from Fraunhofer IFAM in Stade. “This allows us to avoid time-intensive secondary operations in the machining plant and thus significantly reduce its workload. At the same time, we meet the highest precision requirements in aircraft construction at all stations, which is a very special challenge, especially with regard to the size and the production-related unique characteristics of the CFRP components”, Brillinger emphasizes and adds: “In Stade, we have developed a comprehensive referencing process which makes it possible to carry out measurement processes with regard to the component optimally positioned in the holding fixture independently of the machining station. At the machining station itself, only a quick referencing consisting of a few measuring points is then necessary.”
On the relieving way to the processing plant – The stations of the Flow-Line
Before the newly developed, versatile, mobile clamping device finally transports the large CFRP components to the machining system, it passes through two subsequent process stations:
In the first station, the holding fixture specially developed by project partner FFT Produktionssysteme GmbH & Co. KG (Fulda), which can handle ten different landing flap or vertical tail plane shell elements with lengths of up to eight meters, is configured in an automated routine to pick up the respective component. Afterwards, a new type of multicamera system (“camera arena”) from the project partner Hexagon AICON ETALON GmbH (Braunschweig) checks the shape accuracy. This ensures that the configured holding fixture optimally positions the CFRP component into the necessary target shape for the following precise machining. Finally, the insertion, positioning and clamping as well as the securing of the component follows.
For transport to the second station, the holding fixture including the component is connected to two Automated Guided Vehicle (AGV) systems. These newly developed AGV systems from the project partner Stäubli WFT GmbH (Sulzbach-Rosenberg) are capable of virtual coupling – which means they exchange data in order to be able to move synchronously without being mechanically connected to each other. This enables them to transport large loads in synchronized operation through several vehicles in a coordinated manner.
Fraunhofer IFAM in Stade developed the second station, where the fixed CFRP component is measured with high precision and automatically using a laser line scanner. This measurement is essential because the component has a high shape variance – and therefore a unique character – due to the manufacturing process. The measurement data can be used to determine the nominal machining paths and the nominal position of the hole positions for the component. The component is now prepared for machining and can be moved from the mobile holding fixture to the machining system.
The third station is the machining system. Since the conventional secondary activities of the machining system have already taken place at the first two stations, only a quick referencing – consisting of the measurement of a few reference points – is necessary here before the actual machining task can be carried out immediately.
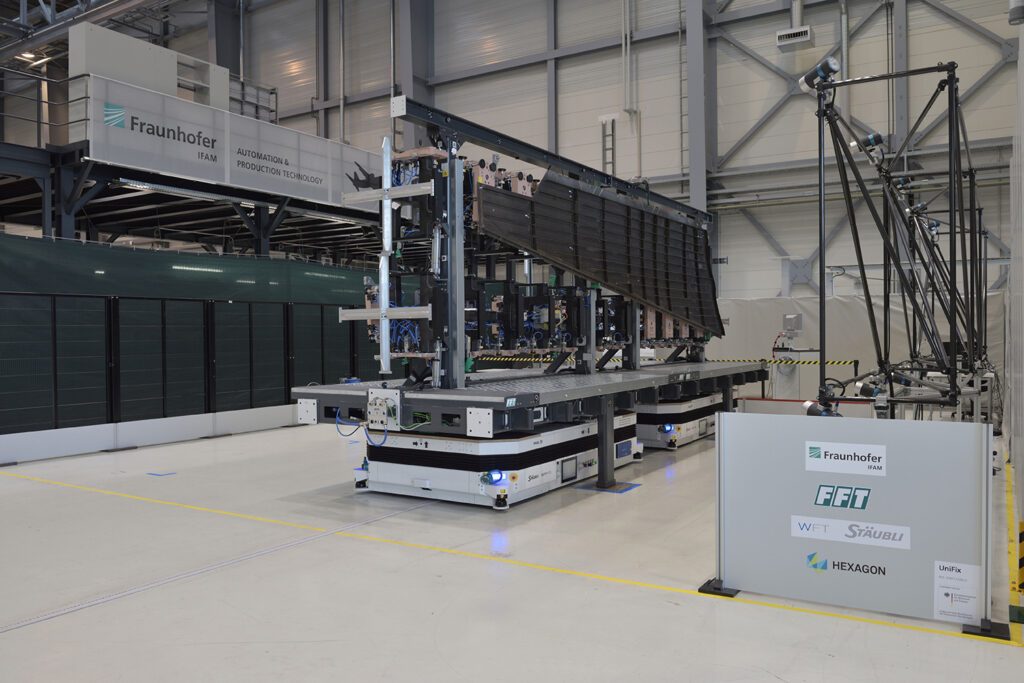
Perspectives
The knowledge gained and technologies developed in the “UniFix” research project can not only be further advanced and implemented for aircraft production, but can also be transferred to the production processes of other industries – such as wind turbine, rail vehicle, commercial vehicle, automotive or shipbuilding – in order to increase efficiency.
In the “InProNi” (Innovative Production Systems from Lower Saxony) project funded by the state of Lower Saxony, Germany, which started on January 1, 2022, the concepts developed in
the “UniFix” research project will be pursued further. The focus is on milling processes at the holding fixture in the machining plant as well as advanced referencing strategies.
Willy Messerschmitt Student Award 2021
The master’s thesis “Automated Scanning Process of a Large Scale CFRP Component” by Satheesh Kumar Kallipalayam Murugesan, which was carried out in cooperation with the Institute of Production Management and Technology (IPMT) at Hamburg University of Technology, Germany, addresses the implementation of automated component measurement of the second station. It was awarded the Willy Messerschmitt Study Prize in 2021 by the German Society for Aeronautics and Astronautics (DGLR).
Project Funder
After a period of approximately three years, the research project “UniFix” (“Universal mobile component holding and fixing device for the processing of fiber composite structures”), funded by the German Federal Ministry for Economic Affairs and Climate Action (BMWK), terminated at the end of 2021; funding code: 20W1722A-D. On behalf of all project partners, Fraunhofer IFAM would like to thank the BMWK for the funding provided.