Highly innovative new tool geometries
The MAI ProCut project group has been working on the question of how it is possible to optimise the finishing of carbon fibre reinforced plastics (CFRP).
The economic evaluation of the cutting performance depends essentially on the machining speed on the one hand and on its abrasion behaviour on the other. Given the same allocations and conditions, including the machining quality to be achieved and the machines used, both factors are the essential measure of the productivity of the tool. Hufschmied Zerspanungssysteme GmbH in Bobingen has developed completely new and highly innovative tool geometries for various different material groups in close cooperation with GFD – Gesellschaft für Diamantprodukte mbH.
Significant productivity gains in virtually any application
In the field of mechanical engineering, a variety of materials are often used for component production due to different requirement profiles and quality criteria.
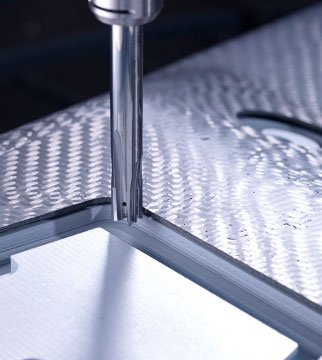
© Hufschmied Zerspanungssysteme
At Schunk Kohlenstofftechnik it has been shown that even in these cases economic potentials can be raised by individually adapting the tool geometry and the diamond coating, which are clearly above 35%.
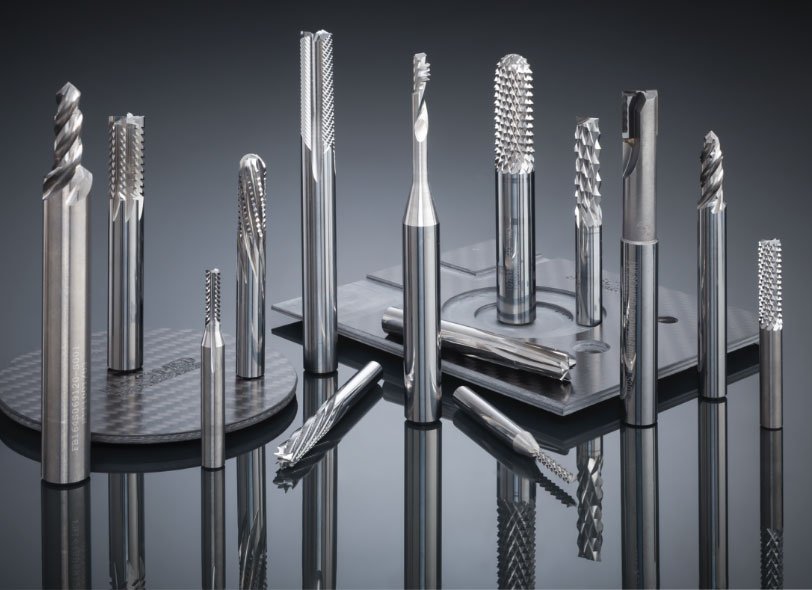
© Hufschmied Zerspanungssysteme
With CMC materials, completely new ways of processing components could be found and validated. The example of a turbine blade from the hot gas area of the German Aerospace Center (DLR) showed that CMC materials do not have to be processed exclusively by grinding. For these materials considerable productivity advantages can be achieved by using milling cutters with suitable cutting edge geometry, too. The use of these tools with coordinated geometry reduces the machining time from several hours to less than 30 minutes in the present case, without compromising the quality of the component.
Using a generic CFRP demonstrator component, additional efficiency improvements of more than 50% were demonstrated. With the newly developed geometries and coatings, this value was achieved and in some cases even exceeded for all materials and processes investigated in the project. This was only possible because the machining speed and at the same time the respective tool life could be increased.
Hufschmied Zerspanungssysteme was nominated for the Supplier Innovation Award 2016 of BMW AG for its contribution to the machining of carbon and was awarded in the “Productivity” category. In addition, Hufschmied Zerspanungssysteme was able to secure and expand the international competitive situation due to the excellent work.
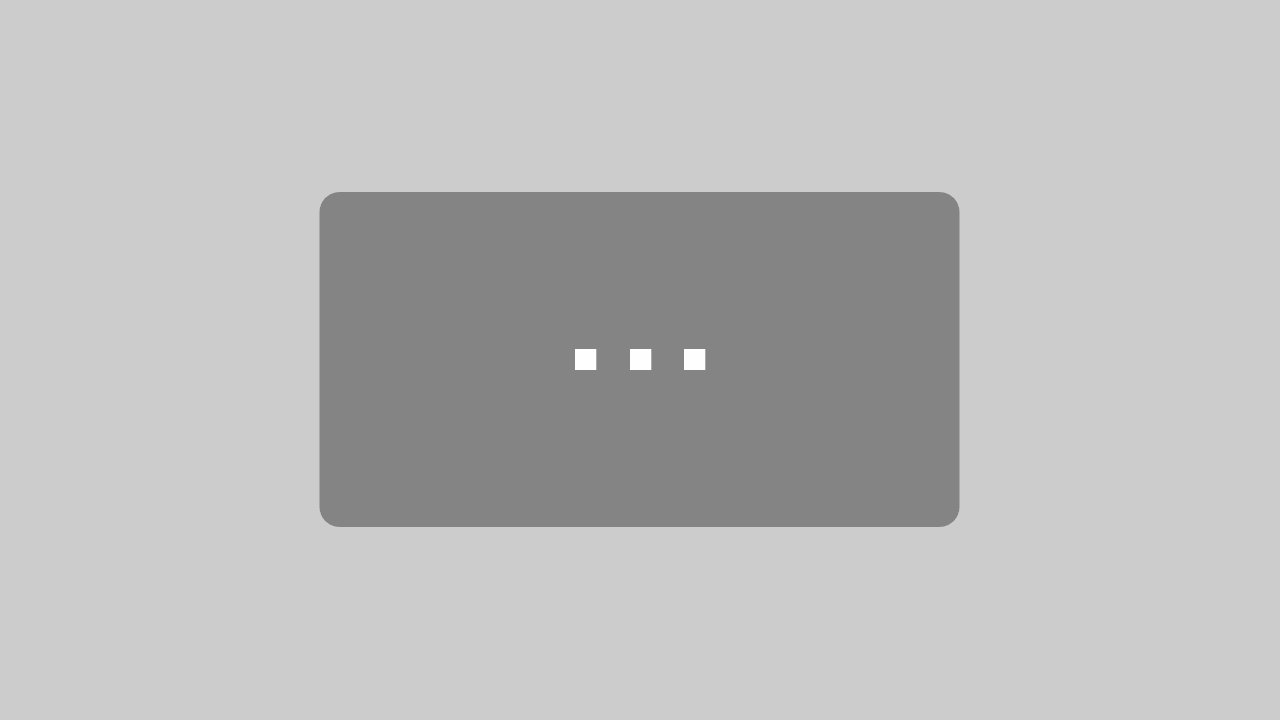
By loading the Video you accept the privacy policy of Vimeo.
Read More
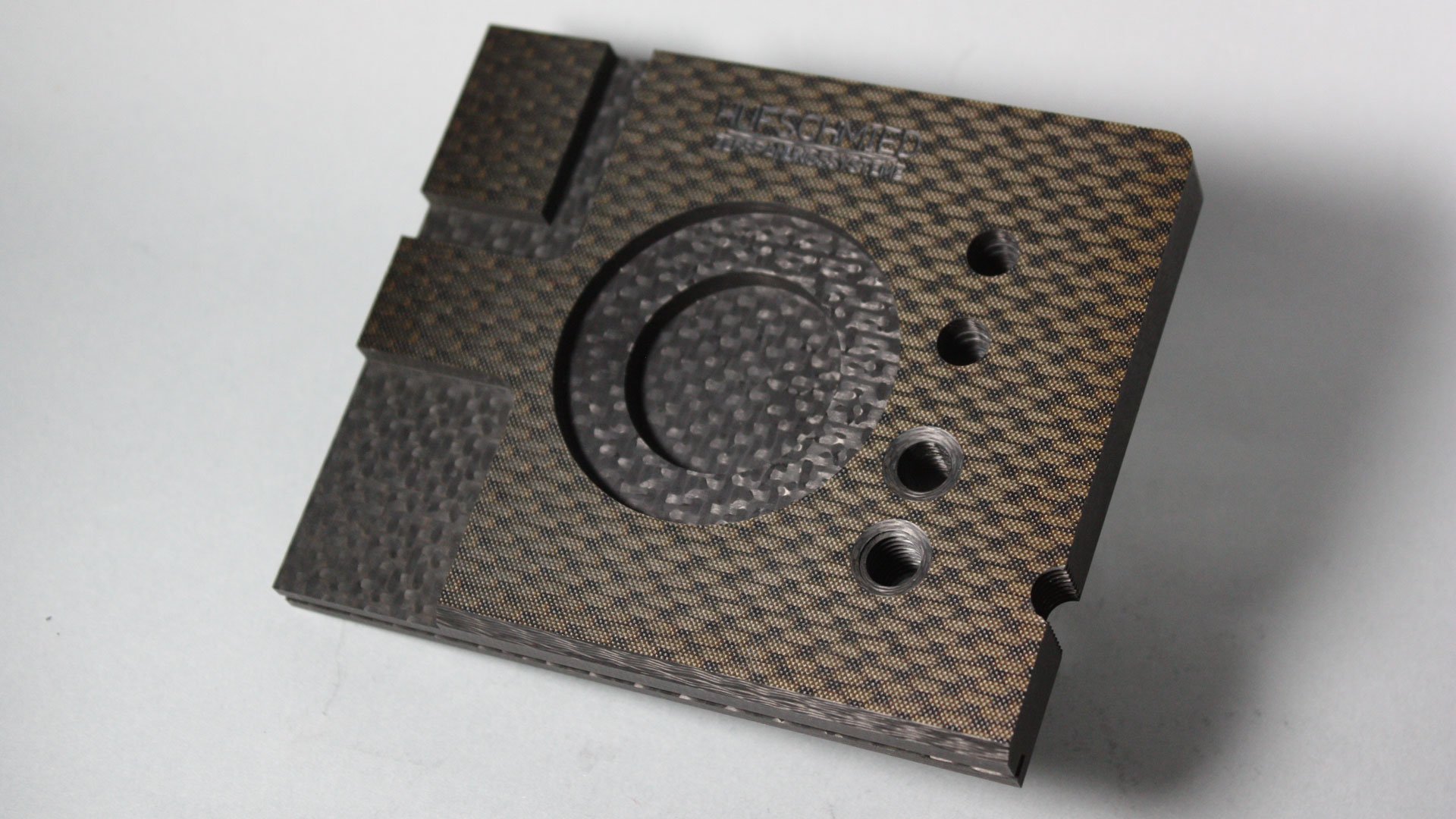