The skeleton construction using the example of a roof bow
In the MAI Skelett funding project, the strategic objective of significantly reducing the costs of CFRP components using a new design and production technology approach was developed and confirmed by using the example of a roof bow. For the roof bow, the load-path-compatible design of the roof bow is implemented by a few unidirectional but strong strands of continuous fibre-reinforced carbon fibres along the bow and thus in the transverse direction of the vehicle, which are connected by a ribbed structure in the sense of a framework (skeleton construction). In terms of production technology, the manufacturing process is limited to three known, industrially used, robust processes for component production. The pultrusion of continuous fibre-reinforced carbon fibres into unidirectional strands with a thermoplastic matrix, the forming of the rods into a product-specific fibre reinforcement, whereby even strong changes in cross-section are possible, and the overmoulding of these profiles in the sense of inserts. Recycled carbon fibres are used as injection moulding material.
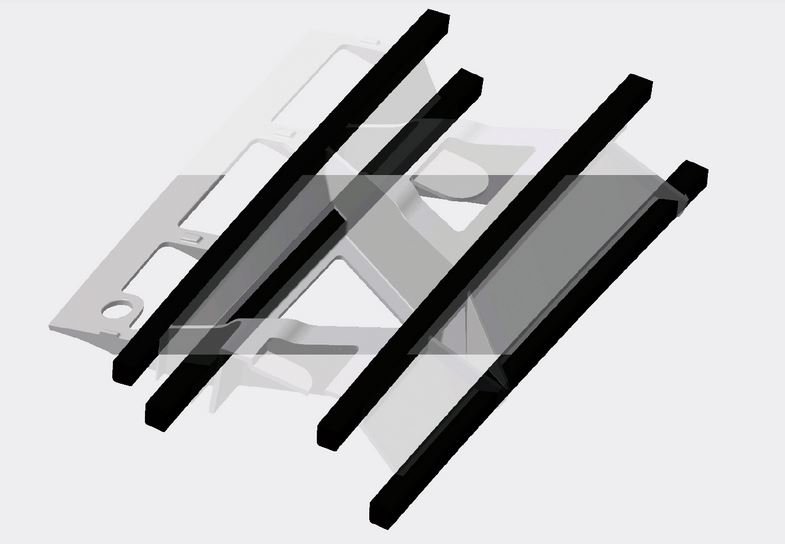
© BMW Group
The potential of a long-fibre reinforced carbon injection moulding compound has been fundamentally investigated in parallel tests.
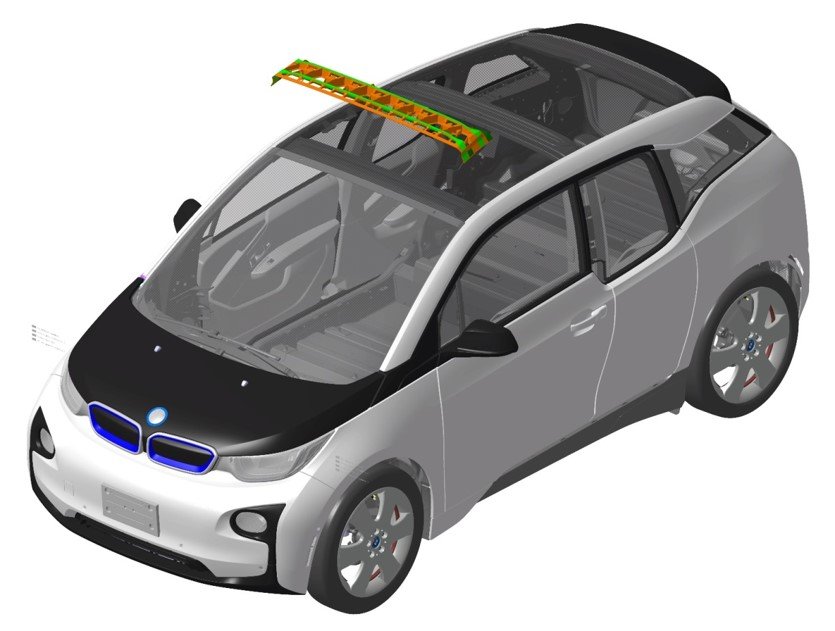
© BMW Group
In addition to the material variance for the injection moulding material, the geometrical freedom of the injection moulding process was used for the optimal design of the component as well as the functional integration, e.g. of screw-on elements. Thanks to the committed cooperation of the partners, who focused their efforts along the process chain, it was possible to carry out the tests based on the concept within a short project period. The partners were: BMW AG (concept, design, rod forming, testing); SGL Automotive Carbon Fibers GmbH & Co KG (carbon fibre reinforced injection moulding materials); CirComp GmbH (pultrusion of rods); P+Z Engineering GmbH (design) and Eckerle GmbH (injection moulding).